For small businesses in the apparel industry, creating labels and tags that last and represent the brand effectively is crucial. Choosing the right material can be a challenge, especially when balancing durability, aesthetics, and cost. This guide explores Tyvek®, a unique synthetic material developed by DuPont, offering practical insights into its use for apparel labels and tags.
Discover why this material, often mistaken for paper, provides exceptional durability and water resistance, making your branding elements resilient through wear and washing. Understanding Tyvek® can help elevate your product presentation and ensure essential information remains intact, supporting small businesses in building a quality brand image. Let’s start!
1. Understanding Tyvek: Beyond its Paper-Like Appearance
1.1 The Core Material: Flashspun High-Density Polyethylene (HDPE) Fibers
Despite its appearance, Tyvek® is fundamentally different from paper. The core material is 100% High-Density Polyethylene (HDPE), a common synthetic material (plastic), not cellulose derived from trees. DuPont manufactures Tyvek® using a unique flashspun process.
This technique involves spinning extremely fine, continuous polyethylene fibers and then bonding them together using heat and pressure, without chemical binders, to form a strong nonwoven sheet. This results in a material that combines some characteristics of paper, film, and fabric. An important consideration for sustainability is that Tyvek® is a recyclable plastic.
Read more: What is LDPE & HDPE Plastic? Differences & Uses Explained
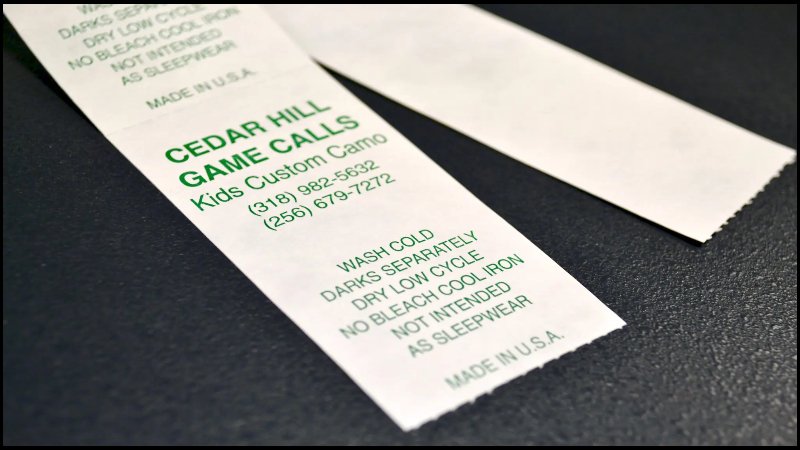
1.2 Key Difference: Hard vs. Soft Structures for Labels
Tyvek® isn’t monolithic; it comes in different styles, primarily distinguished by their structure and feel. For label applications, understanding these differences is key:
- Hard Structure: This type feels stiffer and more paper-like. Its rigidity makes it well-suited for applications requiring structure, such as hang tags or durable patches that need to maintain their shape. This variant is generally more common and easier to source for typical label printing needs.
- Soft Structure: As the name suggests, this version is more flexible and has a softer, more fabric-like texture and drape. While its flexibility might seem appealing for sewn-in labels intended to lie flat against the skin, it’s often less common for standard apparel labeling compared to the hard structure types.
2. Why Tyvek Matters for Apparel: Essential Properties & Material Science
2.1 Exceptional Durability & Tear Resistance
One of Tyvek’s most significant advantages for apparel applications is its remarkable durability and tear resistance. The material boasts a high strength-to-weight ratio, meaning it’s incredibly strong despite being lightweight.
This resilience stems from its structure: a network of continuous nonwoven fibers randomly distributed and bonded. Unlike paper, which tears easily along grain lines, or woven fabrics that can unravel or fray, Tyvek’s structure disperses stress across multiple fibers, making it exceptionally difficult to tear.
This robust quality ensures that labels and tags maintain their integrity throughout the garment’s life, even with frequent washing and wear. The material exhibits high tensile strength (resistance to breaking under tension), contributing significantly to its overall performance as a label material.
2.2 Water and Chemical Resistance
Tyvek’s composition of 100% HDPE makes it inherently hydrophobic, meaning it repels water rather than absorbing it. This water resistance is crucial for apparel labels, ensuring they don’t weaken, disintegrate, or become illegible when exposed to moisture, whether from rain, sweat, or the washing machine.
Furthermore, Tyvek® exhibits good resistance to many common chemicals, including detergents and cleaning agents frequently encountered during laundering. Because the material itself is chemically inert and has a neutral pH, printed information tends to remain legible, and the label’s structure isn’t compromised by standard washing processes.
This means branding, sizing, and care instructions stay sharp and readable for longer. While not entirely waterproof under prolonged submersion or high pressure, its resistance is more than sufficient for typical garment use and care.
2.3 Lightweight Nature
Despite its strength, Tyvek® is exceptionally lightweight. This low weight and minimal bulk are advantageous for apparel labels, ensuring they don’t add noticeable heft or stiffness to the garment. This is particularly relevant for lightweight fabrics, activewear, or layered pieces where a heavier label could potentially affect the drape or comfort.
The material composition allows for durable labeling without compromising the feel or design of the clothing item itself.
2.4 Printability on a Unique Surface
Tyvek® provides a reliable printing substrate suitable for detailed graphics, logos, care instructions, and text, making it effective for branding and informational labels. However, its synthetic nature means it has a non-porous surface, unlike absorbent paper or many fabrics. This characteristic requires specific printing techniques to ensure ink adheres properly and achieves durability, particularly through washing.
Methods like thermal transfer and UV inkjet printing are commonly recommended for achieving crisp, lasting prints on Tyvek®. Standard water-based inkjet inks, for instance, will not bond effectively. Successfully printing on this unique surface is key to leveraging its benefits for high-quality labels.
2.5 Breathability
Tyvek® possesses a unique property known as breathability, meaning moisture vapor can pass through its microscopic pores, even though liquid water is repelled. This characteristic is a result of the nonwoven process and is highly valued in applications like protective apparel or construction wraps.
However, for the relatively small surface area of typical clothing labels and tags, the direct benefit of breathability is often less significant compared to its durability, printability, or water resistance. While it doesn’t trap moisture vapor like a solid plastic film might, its impact on garment comfort when used as a small label is minimal.
The relevance might increase for larger applications, like decorative back patches or internal panel linings.
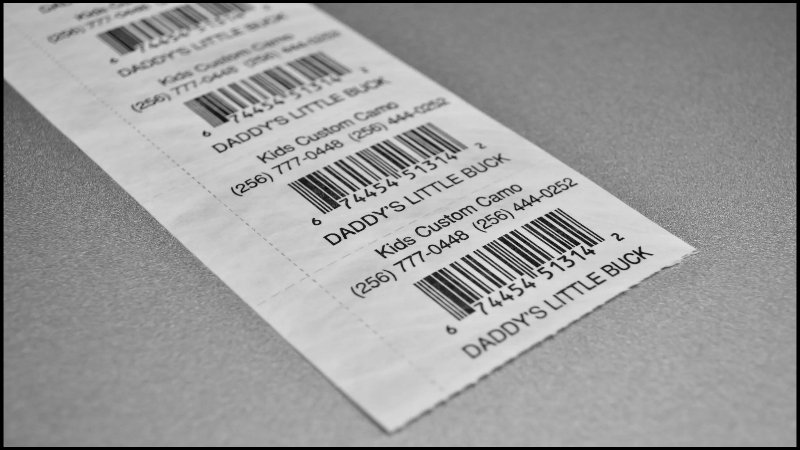
2.6 Sewability for Garment Application
A critical practical consideration is that Tyvek® sheets exhibit good sewability, allowing them to be securely attached to garments using standard sewing techniques. Both industrial and domestic sewing machines can handle the material, making it straightforward to incorporate sewn Tyvek® labels during production.
This ability to be stitched directly onto fabric is essential for creating permanent, durable branding and information labels integral to the garment application. Its physical properties allow it to withstand needle penetration without easily tearing along the stitch line when appropriate techniques are used.
3. The Advantages of Using Tyvek for Clothing Labels & Tags
3.1 Long-Lasting Branding That Endures
The inherent properties of Tyvek® translate directly into significant advantages for apparel branding. Its exceptional durability, water resistance, and tear resistance ensure that brand logos, sizing information, and care instructions remain clear and attached throughout the garment life.
Unlike paper tags that disintegrate or woven labels that can fray and become illegible after multiple washes, Tyvek® labels maintain their integrity and appearance. This resilience protects the brand image, conveying professionalism and quality long after the initial purchase, ensuring essential information is always accessible to the consumer. Investing in durable labels like Tyvek® contributes to a perception of overall product quality.
3.2 Unique Aesthetic Potential: Modern & Technical
Beyond its functional strengths, Tyvek® offers a distinct visual and tactile appeal that can enhance a garment’s design. Its characteristic matte finish, subtle texture, and typically bright white appearance contribute to a modern, technical, or even minimalist aesthetic.
This makes it a compelling choice among label materials for specific clothing styles, such as streetwear, outdoor gear, technical apparel, workwear, and accessories like bags or backpacks. The unique aesthetic can signal innovation, durability, and attention to detail, aligning the label itself with the brand’s identity. Its somewhat industrial feel can be leveraged as a deliberate design element.
3.3 Performance Under Pressure: Ideal for Demanding Uses
Tyvek® truly shines in applications where labels face harsh conditions. Its inherent robustness makes it ideal for demanding uses and specific apparel categories requiring high performance. Consider its suitability for:
- Activewear: Resists sweat, friction, and frequent washing cycles.
- Swimwear: Holds up well against chlorine, saltwater, and sun exposure.
- Children’s clothing: Withstands the rigors of frequent laundering and rough wear.
- Workwear: Resists abrasion, potential chemical exposure, and demanding physical environments.
In these contexts, the durability of Tyvek® ensures that branding and critical information (like safety warnings or care instructions) remain intact and legible, outperforming less resilient label materials.
3.4 Cost-Effectiveness in the Long Run
While the upfront cost of Tyvek® labels might differ from basic paper or lower-quality synthetic options, evaluating cost-effectiveness requires looking at the bigger picture, especially for small businesses balancing budget and quality.
The exceptional durability means labels are less likely to require replacement due to damage or illegibility during the garment’s lifespan. More importantly, a high-quality, enduring label contributes positively to brand perception and customer satisfaction.
Investing in a label that reflects the quality of the garment itself can be seen as a strategic investment in brand building, offering better long-term value than options that quickly degrade and detract from the product experience.
4. Working with Tyvek: Practical Tips for Printing & Attachment
4.1 Printing Your Designs on Tyvek Labels
Achieving durable, high-quality prints on Tyvek® requires understanding its unique surface properties. As a non-absorbent synthetic material, standard printing techniques designed for paper often yield poor results. For reliable label production, consider these methods:
- Thermal Transfer Printing: This is a widely recommended method. The process uses heat to transfer ink from a specialized ribbon directly onto the Tyvek® surface. When paired with the correct ribbon formulation (often resin-based for maximum durability), thermal transfer produces sharp, resilient images resistant to abrasion and washing. The quality of the print offers good wash fastness.
- UV Inkjet Printing: In this process, liquid ink is applied and then instantly cured (hardened) by exposure to ultraviolet (UV) light. This method achieves excellent adhesion on non-porous synthetic materials like Tyvek®, resulting in durable, vibrant prints suitable for demanding applications.
Methods generally not recommended include:
- Standard Desktop Inkjet Printers: These typically use water-based inks that will not properly absorb into or dry on Tyvek’s surface, leading to smudging and poor durability.
- Most Laser Printers: The heat generated during the fusing process in many laser printers can exceed Tyvek’s relatively low melting point (approximately 135°C / 275°F), potentially causing the material to shrink, warp, or even melt inside the printer.
Choosing the appropriate printing method and inks specifically designed for synthetic substrates is crucial for ensuring logo clarity and information legibility throughout the life of the garment.
4.2 Sewing Tyvek Labels onto Garments
Tyvek’s structure allows for straightforward sewing and attachment to fabrics, demonstrating good sewability. However, following best practices ensures a clean application and preserves the material’s integrity:
- Needle Choice: Use sharp, fresh sewing machine needles designed for piercing tightly woven or dense materials. Sharp needles or Microtex needles in sizes like 70/10 or 80/12 generally work well, creating clean holes without excessive fiber disturbance.
- Thread Selection: Opt for a strong, 100% polyester thread. Polyester thread offers durability and resistance to moisture and chemicals encountered during washing, matching the resilience of the Tyvek® label itself.
- Stitch Length: Select a slightly longer stitch length than typically used for standard fabrics, perhaps around 3.0 mm. Shorter stitches create more perforations close together, which could potentially weaken the tear resistance along the seam line due to the nature of the bonded HDPE fibers.
- Testing: Always test your machine settings (tension, stitch length) on a scrap piece of Tyvek® before sewing onto the final garment. This allows for adjustments to achieve the best result without damaging the label or fabric.
Proper sewing techniques ensure the label remains securely attached without compromising the material’s inherent strength.
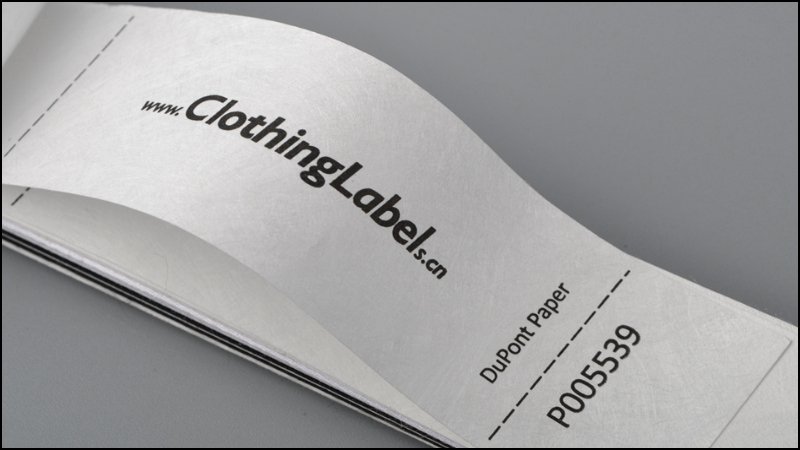
5. Important Considerations for Apparel Businesses
5.1 Washability & Care Instructions
While the Tyvek material itself exhibits excellent washability and holds up extremely well against water and detergents, it’s crucial to understand that the longevity of the printed information is highly dependent on the printing technique and ink quality used.
A label printed with unsuitable inks or methods may fade, smudge, or wear off long before the Tyvek® itself degrades. Therefore, providing accurate care instructions requires confidence in both the substrate and the print.
Before committing to large-scale production, it is strongly advisable to conduct thorough testing by subjecting prototype labels (attached to fabric) to multiple home laundry cycles (washing and drying according to intended care instructions) to verify the print’s durability and legibility under real-world conditions.
5.2 Recycling & Sustainability Perspective
From a sustainability standpoint, Tyvek® presents a nuanced picture. The material is made from HDPE (#2 plastic), which is technically recyclable. However, its recyclability in practice can be challenging. Because Tyvek® is a flexible, nonwoven sheet rather than a rigid container, it typically cannot be processed alongside bottles and jugs in standard municipal curbside recycling programs.
It often requires specialized collection streams designed for flexible HDPE films, similar to grocery bag drop-off points at retail locations. Availability of such programs varies significantly, so businesses and consumers should check local facilities to confirm acceptance.
DuPont has historically offered mail-back programs for Tyvek® recycling, but the scope and availability should be verified directly with the company. Using synthetic materials like Tyvek® inevitably involves considering the broader environmental impact associated with plastic production and end-of-life management. Transparency about the material type and realistic recycling options is important.
5.3 Feel Against the Skin
The tactile experience, or feel, of a Tyvek® label is an important consideration, particularly for garments worn close to the body. Standard hard structure Tyvek® often has a noticeable stiffness and can feel somewhat crinkly, especially when new. While it may soften slightly after repeated washing, it generally retains a different texture compared to traditional fabric labels.
For items where label placement is directly against sensitive skin (like an inner neck label), this stiffness might be perceived negatively by some wearers. Designers should consider placing such labels on exterior locations or seams where contact is minimized.
Alternatively, exploring soft structure Tyvek® variants, which offer greater flexibility, could be an option, although sourcing might require more effort. Evaluating the trade-off between durability, aesthetic, and tactile feel is key.
6. Related Questions
6.1 Is Tyvek the same as paper?
No, Tyvek® is fundamentally different from paper. While it might share a visual resemblance, Tyvek® is composed entirely of HDPE plastic (High-Density Polyethylene). It’s manufactured through a unique flashspun process that bonds fine polyethylene fibers using heat and pressure, without binders.
Paper, conversely, is typically made from cellulose fibers derived from wood pulp. This core material difference results in distinct properties: Tyvek® is highly waterproof and tear-resistant, whereas paper is absorbent and tears relatively easily.
6.2 Can you iron Tyvek labels?
It is strongly advised not to iron Tyvek® labels directly. Tyvek® is heat sensitive and has a relatively low melting point, around 135°C (275°F). Applying direct heat from an iron will cause the material to shrink, distort, melt, or potentially damage the iron itself. Always ensure garments with Tyvek® labels are ironed carefully, avoiding direct contact between the hot iron surface and the label.
6.3 How does Tyvek compare to polyester or nylon labels?
Tyvek® offers a different set of characteristics compared to common polyester labels or nylon labels. Key differences include:
- Texture: Tyvek® typically has a stiffer, more paper-like or slightly crinkly feel, whereas polyester and nylon labels are generally softer and more fabric-like.
- Tear Resistance: Tyvek® boasts exceptional tear resistance due to its nonwoven structure, often exceeding that of standard woven polyester or nylon labels which can fray.
- Aesthetic: Tyvek® often provides a more ‘technical’ or ‘industrial’ aesthetic, while polyester/nylon offer a wider range of finishes (satin, taffeta) often perceived as more traditional for apparel. Printing methods also differ, with polyester/nylon often utilizing dye sublimation or screen printing.
6.4 Where can small businesses buy custom Tyvek labels?
Small businesses looking for custom Tyvek labels can source them through several channels. Specialized apparel trim suppliers often carry Tyvek® or similar synthetic materials. Contacting label printers directly is another option, particularly those equipped with thermal transfer or UV inkjet printing capabilities suitable for synthetics.
Additionally, various online platforms specializing in custom branding materials may offer Tyvek® label printing services. It’s beneficial to seek out suppliers or printers with specific experience working with Tyvek® to ensure quality results. Companies specializing in branding solutions, like the services offered here, can also provide consultation and production for these types of labels.
Read more:
In summary, Tyvek® emerges as a distinctive and highly functional synthetic material for apparel labels and tags. Its unique composition delivers exceptional durability and water-resistant properties, ensuring that crucial branding elements and care information withstand the rigors of wear and washing.
Beyond its robustness, Tyvek® offers a unique aesthetic and is highly printable using appropriate techniques, allowing businesses to create lasting and visually appealing labels. For brands seeking resilient, high-performance tags and labels that offer significant long-term value, exploring Tyvek® is a worthwhile consideration.
Should you need specific advice tailored to your garment types and branding goals, don’t hesitate to consult experts familiar with this versatile material.