For businesses navigating the complexities of clothing production, ensuring consistent garment quality and sizing across different styles and production runs is a persistent challenge. Missteps in defining garment measurements can lead to costly errors, inconsistent fit, and ultimately, damage to brand trustworthiness. This article delves into the critical concept of measurement points (POM) – the specific locations on a garment where measurements are taken.
Understanding and accurately defining these points within your specification sheets is fundamental to successful apparel production, enabling clear communication with manufacturing partners, effective quality control, and the delivery of consistently fitting clothing that meets customer expectations. Readers will gain insight into what POMs are, why they are non-negotiable for achieving reliable garment quality, and how to implement them effectively in their processes.
1. Decoding measurement points: the blueprint for your garments
1.1. Beyond the tape measure: defining points of measure (POM)
Points of measure (POM) refer to precisely defined locations on a piece of clothing or its corresponding pattern where specific dimensions are taken. Think of them not as measurements of the human body, but as specific coordinates on the garment itself used to verify its finished size and shape.
For instance, a POM might define the exact spot to measure the chest width or the sleeve length directly on the apparel item. These established garment measurement points ensure everyone involved in production is assessing the same dimension from the same location.
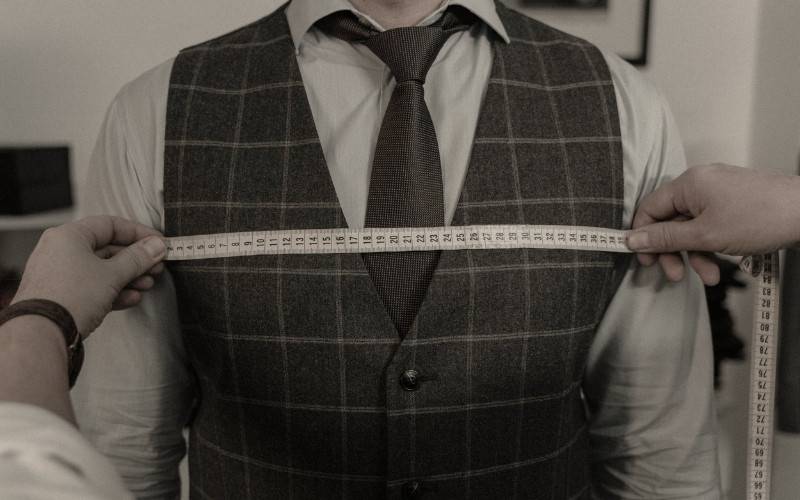
1.2. Why standardized locations matter
Defining standard locations for each measurement is crucial for consistency in clothing production. Imagine trying to give directions without using standard street names or coordinates – instructions would be unclear and lead to errors. Similarly, standardized POMs act like map coordinates for a garment.
They provide a universal reference point ensuring that the designer, the pattern maker, the quality control (QC) team, and the manufacturing facility are all aligned. This shared understanding eliminates ambiguity, promoting repeatability and reliability throughout the manufacturing process. Without this standard, achieving consistent results across different production batches becomes significantly more challenging.
2. The business imperative: why accurate POMs are non-negotiable
2.1. Achieving consistent fit across sizes and production runs
Accurate points of measure are the foundation for achieving the desired fit for your garments consistently. These fit points are critical inputs for the grading process, where pattern makers scale the base size pattern up or down to create the full range of sizes offered in your size chart.
If the initial POMs defining the base size are incorrect or measured inconsistently, those errors will be magnified across all sizes during grading. This leads directly to poor fit consistency – a major source of customer dissatisfaction and costly return rates.
Precise POMs ensure that the intended silhouette and proportions are maintained across your entire size range and from one production batch to the next, enhancing sizing reliability and customer satisfaction.
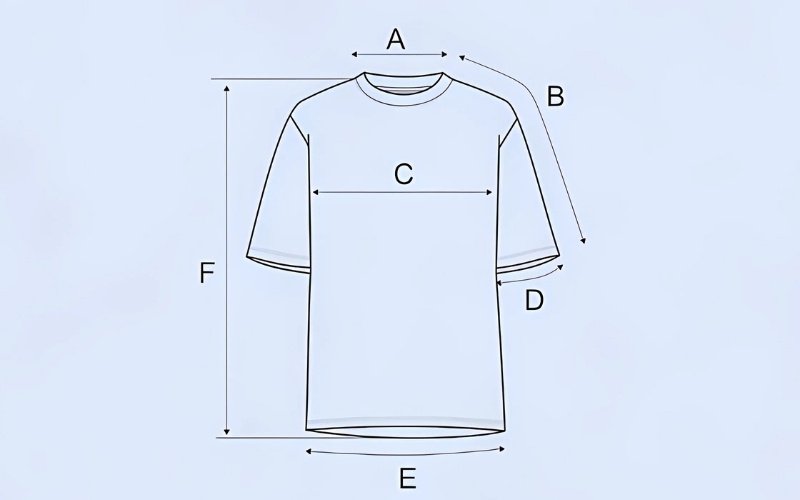
2.2. The backbone of effective quality control (QC)
Well-defined POMs are indispensable for effective quality assurance (QA). During production, quality control personnel rely heavily on the measurement chart within the specification sheet, which lists each POM, its target dimension, and the acceptable tolerance (the permissible variation).
Inspectors use this list as a checklist, physically performing each measurement on randomly selected production garments. They compare the actual measurements against the specifications. If a measurement falls outside the defined tolerance for a critical POM, the garment may be flagged or rejected.
This process transforms quality checks from subjective assessments into objective, data-driven evaluations, ensuring products meet the required standards before shipment.
2.3. Clear communication: speaking the same language as your factory
A comprehensive technical package, with clearly defined POMs detailed in the specification sheet, serves as a universal language between your brand and your manufacturing partner. Clear, unambiguous measurement points and instructions minimize the potential for misunderstandings, assumptions, and errors, especially crucial when working with overseas factories where language barriers might exist.
Standardized POMs ensure everyone involved in apparel production is referencing the exact same points and dimensions, leading to smoother workflows, fewer disputes, and a more efficient production cycle. Effective communication built on precise specifications is key to a successful partnership.
2.4. Protecting your bottom line: cost, waste, and brand image
Inaccuracies in defining or measuring POMs can have significant negative financial impacts. If initial samples are made to incorrect specifications due to poorly defined clothing dimensions, they will require costly revisions and remakes, delaying timelines.
Garments produced with measurements falling outside acceptable tolerance levels might be rejected during QC, leading to wasted materials, labor, and potentially impacting the unit cost. Furthermore, inconsistent fit resulting from measurement issues can lead to increased customer returns, lost sales, and significant damage to brand trustworthiness.
Prioritizing accurate POMs is a fundamental step in waste reduction and safeguarding your brand’s reputation and financial health.
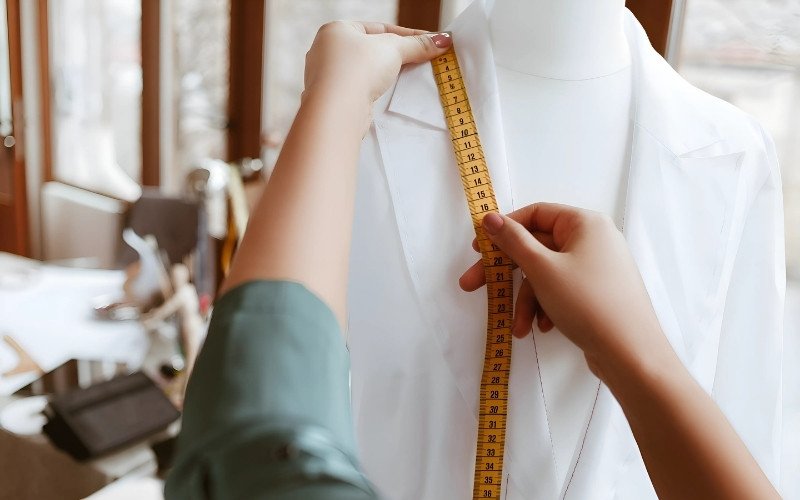
3. Putting measurement points to work: spec sheets & technical packages
3.1. The role of the specification (spec) sheet
The specification sheet, often called a spec sheet, serves as the comprehensive blueprint provided to the factory for producing a garment. While containing numerous details like materials and construction methods, a critical section is the measurement chart.
This chart is the designated home for listing all the required points of measure (POMs), their target garment measurement dimensions for the base size, and the acceptable variance, known as tolerance. Effectively, the spec sheet translates the design intent into measurable instructions for manufacturing.
3.2. Documenting POMs: clarity is key
Clear documentation of each point of measure is paramount to avoid errors in production. Ambiguity is the enemy of consistency. Common methods for documenting POMs within a specification include:
- Standard POM codes: Using industry-recognized abbreviations (e.g., HPS for High Point Shoulder, CB for Center Back Length, SL for Sleeve Length, WAIST for waist width) provides a shorthand, but requires mutual understanding.
- Technical sketches/diagrams: Clear, simple line drawings of the garment showing precisely where each measurement should be taken using arrows or lines.
- Detailed how to measure (HTM) descriptions: This is crucial. Alongside codes and diagrams, written instructions explaining how the measurement is performed are essential. For example, specifying “measure flat, edge to edge,” “measure along the curve, following the seam,” or “measure waistband relaxed, aligned straight across.” A dedicated measurement guide section within the technical package containing these HTM details adds significant clarity.
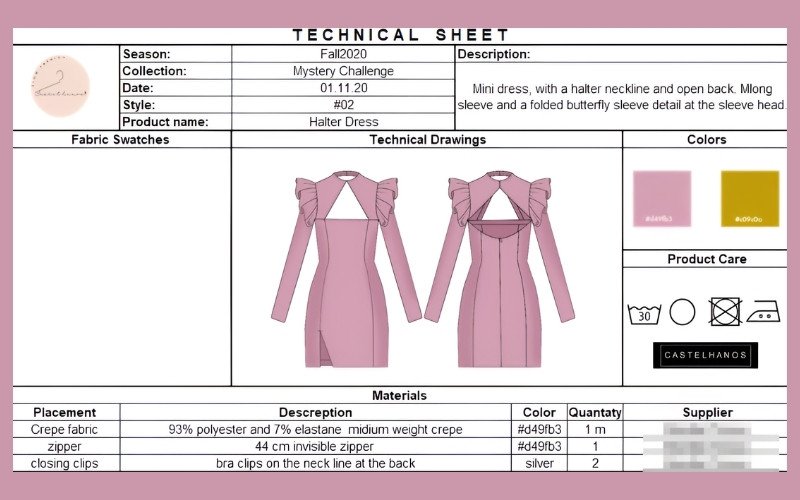
3.3. Understanding and setting tolerances
Measurement tolerance refers to the acceptable range of variation (+/-) from the target dimension specified for a point of measure. Manufacturing processes inherently involve slight variations, making perfect adherence to exact measurements impractical. Therefore, defining a realistic tolerance is necessary.
Setting tolerances requires careful consideration: if they are too tight (e.g., +/- 0.1 cm), production becomes extremely difficult and expensive, potentially leading to high rejection rates. Conversely, if tolerance levels are too loose (e.g., +/- 2 cm), the final garment’s fit and quality consistency can be compromised.
The appropriate measurement tolerance often varies depending on the specific POM (critical fit points usually have tighter tolerances than less critical ones), the fabric type, and the overall expected quality assurance standards for the product.
4. Essential measurement points: Common examples for apparel
4.1. Key POMs for tops (e.g., t-shirts, shirts)
While the specific points of measure (POMs) needed will vary based on the garment’s design, here are some fundamental examples commonly used for tops like t-shirts and shirts, typically measured flat:
- Chest Width: Measured straight across the garment, typically 1 inch below the armhole seam, from side edge to side edge.
- Body Length from HPS (High Point Shoulder): Measured vertically from the highest point of the shoulder (usually where the shoulder seam meets the collar) straight down to the bottom hem edge.
- Across Shoulder: Measured straight across the back, from the outer edge of one shoulder seam to the outer edge of the opposite shoulder seam.
- Sleeve Length (from Shoulder): Measured from the outer shoulder seam down along the top fold or seam of the sleeve to the edge of the sleeve opening/cuff.
- Sleeve Opening: Measured straight across the edge of the sleeve opening, parallel to the hem.
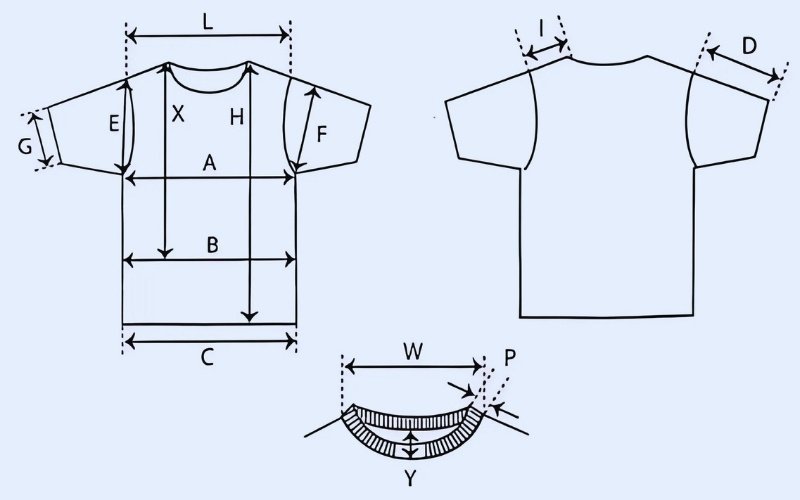
4.2. Crucial POMs for bottoms (e.g., pants, skirts)
Similar to tops, the essential POMs for bottoms depend on the style. Here are common examples for items like pants and skirts, usually measured flat:
- Waistband Width (Relaxed): Measured straight across the top edge of the waistband, from side edge to side edge, with the waistband lying naturally flat (not stretched).
- Hip: Measured straight across the garment at a specified distance below the top of the waistband (e.g., 7-9 inches down, depending on the style/rise), from side edge to side edge. The location needs to be clearly defined.
- Front Rise: Measured from the crotch seam intersection point up along the front center seam to the top edge of the front waistband.
- Inseam: Measured along the inside leg seam, from the crotch seam intersection point down to the bottom edge of the leg opening/hem.
- Leg Opening: Measured straight across the bottom edge of the leg hem, from side seam to side seam (or edge to edge if no side seam).
4.3. A note on other garments (dresses, jackets)
It’s important to recognize that more complex apparel items like dresses, jackets, coats, or items with intricate design features will require additional and sometimes different critical measurements. For example, a fitted dress might need POMs for bust darts, waist placement, and skirt sweep, while a tailored jacket would include measurements for lapel width, vent length, and shoulder pad placement.
The selection of POMs must always be tailored to accurately define the specific garment type and its unique construction and fit requirements. The complexity increases with the garment’s design.
5. Expert advice for small businesses: mastering your measurement points
5.1. Garment vs. body measurements: know the difference
A frequent point of confusion, especially for businesses new to technical specifications, is the difference between body measurements and garment measurements. Spec sheets almost exclusively use finished garment measurements, which are dimensions taken directly from the physical clothing item, usually when laid flat (‘measured flat’). Body measurements, found on a typical size chart used by customers, relate to the dimensions of the person intended to wear the garment.
Directly transferring body measurements onto a spec sheet without accounting for design ease (the difference between body size and garment size needed for comfort and style) and construction details will invariably lead to incorrectly sized samples and production errors. Understanding this distinction is a crucial first step in avoiding a common pitfall.
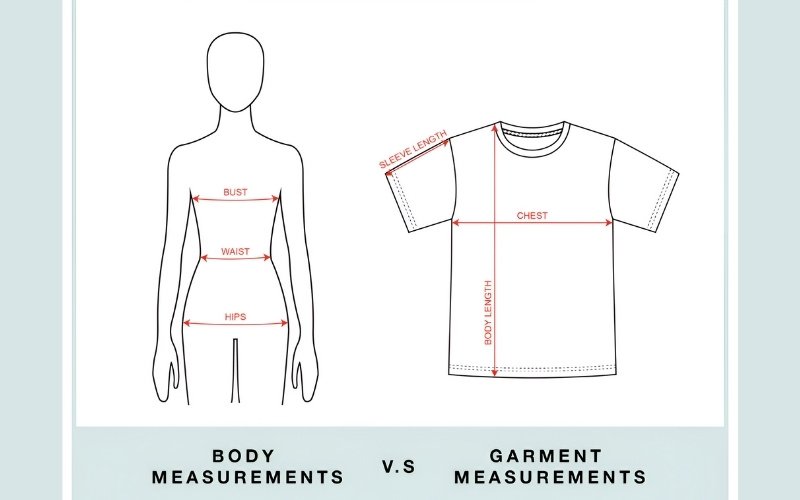
5.2. The value of a clear how-to-measure (HTM) guide
Investing time in creating a dedicated how-to-measure (HTM) guide for your brand is highly recommended. Even a simple document containing clear sketches or photographs illustrating exactly how each specific POM used by your brand should be measured, accompanied by concise descriptive text, provides immense value.
This HTM guide becomes the single source of truth for measurement method, ensuring consistency not only within your internal team (designers, technical designers, QC staff) but also critically, with your factory partners. A clear HTM guide significantly minimizes disputes over whether a garment is within the specified tolerance, preventing costly delays and disagreements related to factory communication.
5.3. Consistency across the board: training and communication
Defining clear POMs and creating an HTM guide is only effective if they are used consistently by everyone involved. Ensure that all relevant personnel – designers, technical designers, pattern makers, internal QC staff, and your primary contacts at the factory – understand and adhere to the same definitions and measurement methods outlined in your brand’s HTM guide.
It is advisable to share your HTM guide with your factory and request confirmation that they understand and agree to follow it precisely. This commitment to consistency in training and communication fosters alignment and reduces the chances of measurement discrepancies slipping through the cracks.
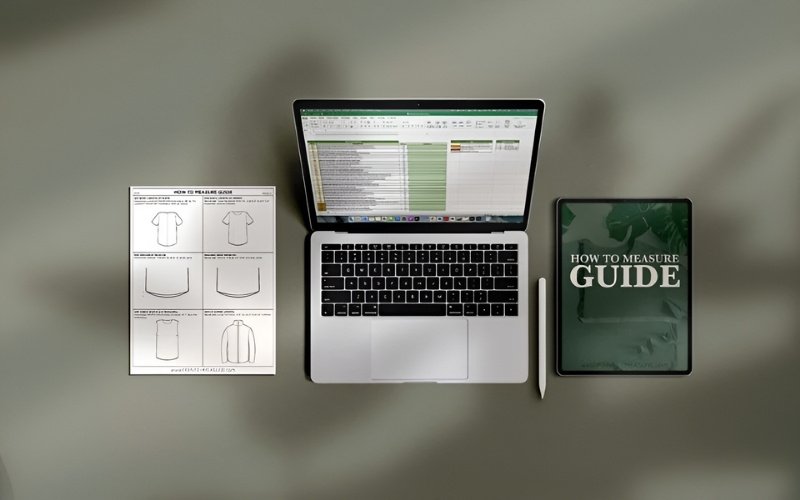
5.4. Continuous improvement: reviewing fit and specs
Treat your specification sheets and associated measurement points as living documents that can benefit from refinement over time. Establish a process for continuous improvement by carefully reviewing the measurements taken from pre-production samples and comparing them against the specs.
Conduct fit sessions, ideally using professional fit models whose body dimensions align with your target customer base, to evaluate how the actual garment measurements translate to the intended fit on a body. Critically analyze customer feedback and return data specifically related to fit issues.
This valuable information can highlight areas where POMs, target dimensions, or tolerances in your specification sheet may need adjustment for future production runs, leading to better-fitting products and increased customer satisfaction.
6. Related questions
6.1. How many measurement points do I need for a simple t-shirt?
For a basic t-shirt, a core set of 5 to 10 measurement points often suffices for ensuring fundamental fit and performing effective quality control. These typically include critical points like chest width, body length, across shoulder width, sleeve length, and sleeve opening.
However, the exact number depends on your brand’s specific quality standards, the complexity of the t-shirt design (e.g., unique seams, pockets), and the level of detail required to accurately capture the intended fit.
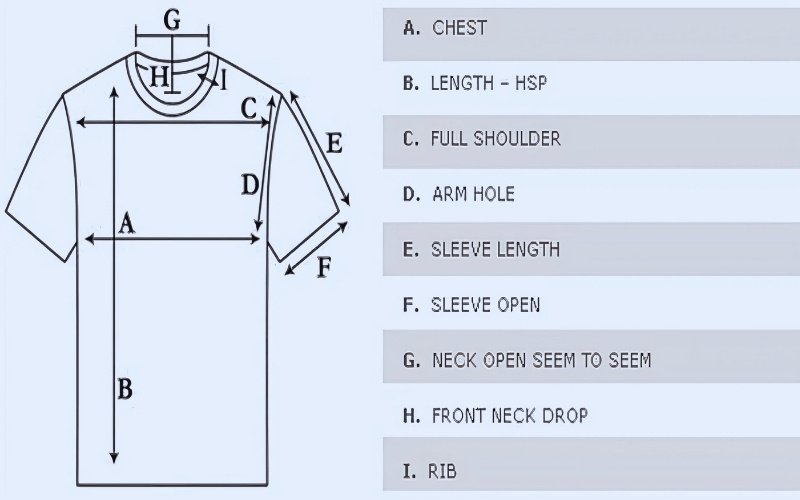
6.2. What’s a common tolerance for garment measurements?
While there’s no single universal standard, common tolerance levels for many garment measurements often fall within +/- 0.5 inches (approximately +/- 1.25 cm) to +/- 0.75 inches (approximately +/- 1.9 cm). However, this can vary significantly.
Critical fit points (like waistband or chest) usually require tighter tolerances, while less critical points (like hem sweep on a loose garment) might allow for wider tolerance levels. Factors like fabric type (stretchy knits often allow slightly more tolerance than stable wovens) and the overall product quality level also influence appropriate settings. Avoid applying one single tolerance value across all measurements.
6.3. Can I just use a standard measurement chart I found online?
It is strongly advised against directly copying a generic measurement chart found online to use as the basis for your product’s specification sheet. While online size charts or sample spec sheets can serve as a reference or starting point for understanding common POMs, they do not reflect your brand’s unique fit intent, specific base patterns (blocks), or established grading rules (how sizes increase/decrease).
To achieve your desired fit consistently, you must develop a customized list of POMs and corresponding measurement specifications tailored precisely to your garments. Using generic charts directly often leads to poor fit and inaccurate production.
Read more:
Mastering measurement points (POM) is a non-negotiable aspect of successful apparel production. These precise locations on garments serve as the foundation for defining dimensions, ensuring sizing consistency across production runs, and enabling effective quality control.
Clearly documented POMs within comprehensive specification sheets facilitate unambiguous communication with manufacturing partners, minimizing errors and costly rework. Ultimately, a diligent approach to defining, measuring, and managing POMs directly impacts your bottom line by reducing waste, lowering return rates, and building brand trustworthiness through reliable product quality and fit.
Investing the time to establish and refine your measurement standards is crucial for any clothing business aiming for consistent results and satisfied customers. Should developing detailed technical packages or implementing robust qc processes seem daunting, seeking guidance from experienced technical designers or production consultants can provide valuable support.