Understand what debossing is and how it adds subtle sophistication to your apparel branding. This finishing technique creates elegant, sunken designs pressed into materials like paper hang tags and leather patches using a custom die and pressure.
Unlike raised embossing, debossing provides unique depth and a refined tactile feel. This guide explores the process, compares techniques, and discusses optimal design and material considerations. Learn how debossing elevates perceived value and offers an understated aesthetic, making a lasting impression for your brand through enhanced texture and quality cues.
1. What Does Debossing Mean?
1.1 Defining Debossing
Debossing is a finishing technique used to create a recessed pattern—such as a logo, text, or graphic—pressed *down into* the surface of a material like paper, cardstock, or leather. This process results in a design that is sunken or indented relative to the surrounding surface, the opposite effect of embossing, which creates a raised design. The primary outcome of debossing is the creation of noticeable depth and texture. This method is a specific type of impression technique (applying pressure to create a mark).
1.2 The Debossing Process
The creation of a debossed effect follows a straightforward technique. First, a custom metal plate, known as a ‘die’, is crafted with the mirror image of the desired design engraved into it. This die is then pressed onto the chosen material (the substrate) using considerable pressure.
For certain materials, particularly leather or thicker cardstock, controlled heat application may be used alongside the pressure. This combination helps to achieve a sharper, cleaner indentation. The core process involves the die applying force to the material, resulting in the sunken design.
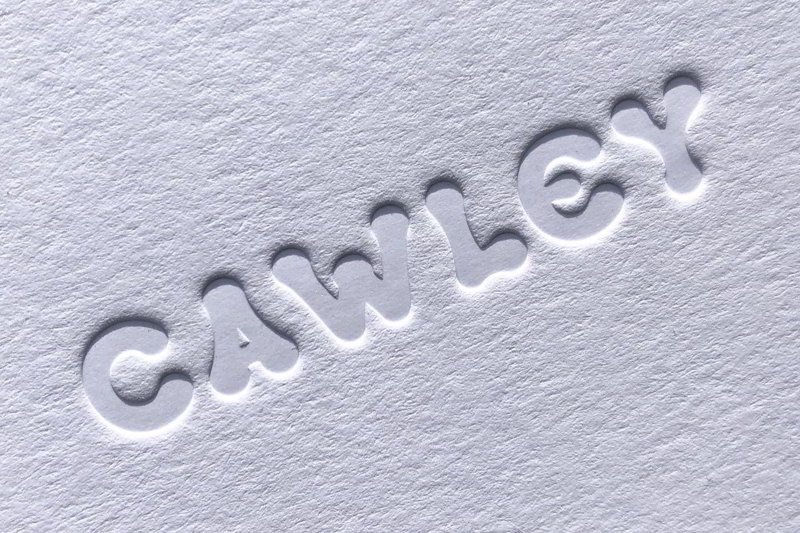
2. Debossing vs. Embossing: Spotting the Key Differences for Your Tags & Labels
Understanding the distinction between debossing and embossing (a process creating a raised design) is crucial when selecting finishes for apparel branding elements. While both techniques manipulate the material surface to add dimension, they produce opposite effects.
2.1 Raised vs. Sunken
The core comparison lies in the direction of the impression. Debossing creates a design pressed *down into* the material, resulting in a sunken look. Conversely, embossing pushes the design *up from* the material’s surface, creating a raised effect. This difference is immediately apparent visually and through tactile feel. Running a finger over a debossed area means dipping *into* the indentation, while an embossed area feels like running over a protrusion.
Here’s a quick comparison:
Feature | Debossing | Embossing |
---|---|---|
Effect | Sunken / Indented | Raised / Protruding |
Visual | Design sits below the surface level | Design stands out above the surface level |
Tactile Feel | Finger dips into the recessed design | Finger runs over the raised design |
2.2 How Each Technique Affects Your Material
The material impact differs significantly between the two methods, especially concerning the back of the substrate. Because embossing physically pushes the material upwards from behind, a mirrored, raised impression (called a ‘bruise’ or ‘debossed’ effect on the back) is naturally created on the reverse side.
Debossing, pressing from the front, typically has less material impact on the backside. On thicker, sturdy materials often favored for quality hang tags or patches (like heavy cardstock or leather), the front indentation may cause little to no visible mark on the reverse. However, be aware that with very thin paper or cardstock, some slight impression might show through on the back even with debossing.
2.3 Choosing the Right Impression for Apparel Items
Selecting between debossing and embossing often comes down to brand aesthetic and desired impact:
- Choose Embossing: Opt for embossing when aiming for a bolder, more prominent effect that physically stands out. The raised design catches light differently and offers a strong visual presence. Consider if the mirrored effect on the back aligns with your design needs (e.g., on a single-sided tag).
- Choose Debossing: Select debossing for a more subtle, understated, and sophisticated feel. The sunken impression provides texture and elegance without overt protrusion. This is often preferred for a refined look, and the minimal backside impact on thicker materials can be advantageous.
Consider the material choice and whether a visible impression on the back is acceptable or desirable for your specific tag or label application.
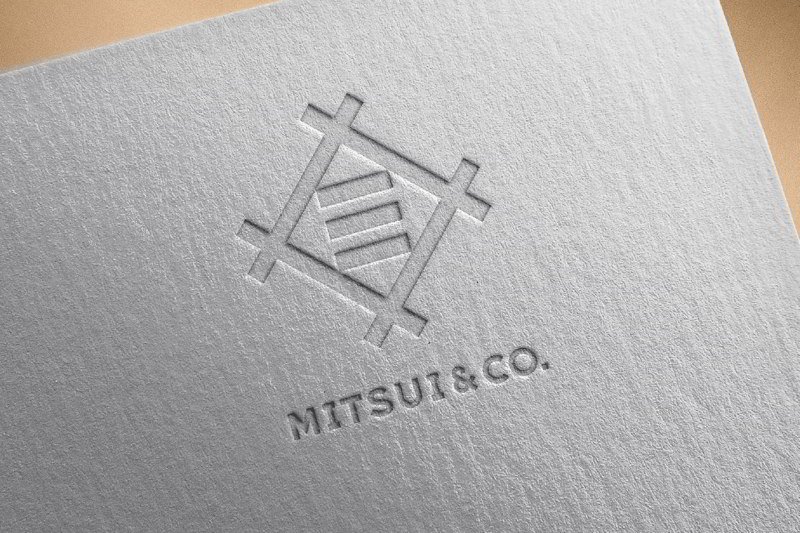
3. Applying Debossing to Enhancing Apparel Brand Touchpoints
Debossing offers versatile applications beyond just a visual effect; it adds a tactile dimension that can elevate various branding elements associated with apparel. From hang tags to packaging, this technique introduces subtle sophistication.
3.1 Paper Hang Tags
On paper or cardstock hang tags, debossing introduces an element of perceived luxury and tactile interest. The indented design invites touch, creating a memorable interaction with the brand before the garment is even worn. This technique is highly effective for rendering logos, monograms, or key graphic elements with distinction. Options include:
- Blind Deboss: The impression alone, relying solely on shadow and texture for a subtle, elegant effect.
- Deboss with Ink/Foil Fill: Filling the recessed area with color or metallic foil adds visual contrast and emphasis while retaining the textural depth.
Applying debossing to hang tags subtly communicates attention to detail, potentially increasing the perceived value of the product itself.
3.2 Leather & Faux Leather Patches
Debossing is particularly well-suited for leather patches and faux leather (leather goods). The technique creates a clean, crisp impression that is highly durable, as the design is pressed into the material rather than sitting on the surface. This inherent durability makes it ideal for items expected to withstand wear and washing. The result is a sophisticated, often permanent mark associated with quality craftsmanship.
While debossing offers detail and refinement, it’s useful to compare it with alternatives:
- Stamping: Often a simpler process, stamping might use pressure (sometimes heatless) for basic shapes or text but may offer less fine detail or depth control than debossing.
- Engraving: Laser engraving burns the design into the leather, creating a different look and feel, often darker and with a distinct texture.
For detailed logos or refined branding on leather, debossing often provides superior clarity and elegance.
3.3 Specialty Woven Label Patches
It’s important to clarify that standard, thin woven labels typically lack the structure for effective debossing. However, the technique can be applied to specialty woven patches. These are typically thicker, denser, and more structured items, sometimes referred to as high-density or padded woven patches.
On these specific types of patches, a subtle debossed effect can add an extra layer of dimension and texture, enhancing intricate woven designs without creating significant depth. This remains a niche application, suitable only for appropriately constructed patches.
3.4 Packaging Considerations
Extend the tactile branding experience to your packaging elements. Debossing works beautifully on thicker paper goods used for presentation, such as:
- Heavy cardstock inserts within garment bags
- Rigid presentation boxes
- Quality thank-you notes or stationery
Incorporating a consistent debossed element across these touchpoints reinforces brand identity. However, it’s crucial to note that debossing is not suitable for thin, flexible materials like standard poly mailers. These materials lack the rigidity required to hold a crisp, lasting impression.
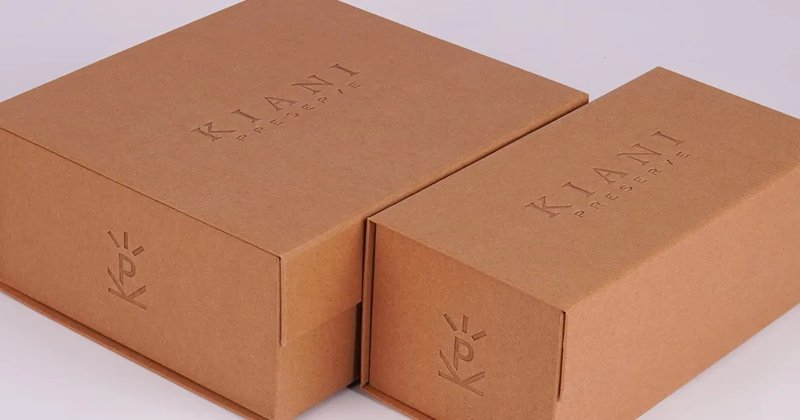
4. Key Considerations Before Choosing Debossing
Before committing to debossing for your apparel branding elements, several factors warrant careful thought to ensure the best results and alignment with your brand goals. Proper material selection and thoughtful design tips are paramount.
4.1 Material Selection
The success of debossing heavily relies on the chosen substrate. Not all materials yield the same quality of impression.
- Paper/Card Stock: For hang tags, opt for heavier weight paper stock. Aim for materials like heavyweight cardstock, typically at least 14pt (around 300 GSM) or higher. Thicker, denser paper allows for a deeper, more defined debossed effect without easily showing marks on the reverse side. Material thickness is crucial here.
- Leather/Faux Leather: Most leather types and quality faux leathers accept debossing well. Smoother finishes generally produce cleaner, sharper impressions compared to heavily textured leathers. The density and firmness of the leather influence how well fine details are captured.
The interplay of applied pressure, heat (if used), and material properties determines the final look.
4.2 Design for Debossing
Not all designs translate perfectly into a debossed format. Consider these design tips for optimal clarity and visual impact:
- Use Bold Elements: Opt for clean lines, relatively bold graphics, and medium-weight typography.
- Avoid Fine Detail: Extremely intricate patterns or very small text can lose definition or fill in during the debossing process, becoming illegible.
- Ensure Adequate Spacing: Allow sufficient ‘white space’ or negative space around the debossed elements. This helps the indented design stand out and prevents areas from merging.
- Consider Depth: If aiming for a deeper deboss, ensure the design elements are substantial enough to support the depth without compromising clarity.
4.3 Blind Deboss vs. Ink/Foil Combinations
Debossing offers several aesthetic variations based on whether the impression is left plain or filled:
- Blind Deboss: This is the impression alone, with no ink or foil added. The effect relies purely on the shadows and texture created by the indentation, offering a subtle, sophisticated, and often minimalist look.
- Deboss with Ink Fill: The debossed area is filled with ink. This adds color and contrast, making the design more visually prominent while maintaining the textural feel of the indentation.
- Deboss with Foil: Foil stamping is applied into the debossed area. This creates a high-contrast, often luxurious effect using metallic or pigmented foils, combining the depth of debossing with the shine or opacity of foil.
4.4 Durability Insights for Apparel Applications
The debossed impression itself offers good durability because the design is recessed into the material, protecting against surface abrasion. However, when considering tags or patches attached to garments, the overall longevity depends on several factors beyond the debossing technique:
- Patch/Tag Material: The inherent durability of the chosen paper, card, or leather/faux leather significantly impacts how well the item withstands handling, washing (if applicable), and wear.
- Attachment Method: How the tag or patch is attached (e.g., sewn securely, quality adhesive) is critical to its lifespan on the garment.
While the debossed design is robust, the item’s overall resilience is tied more closely to the base material quality and how securely the branded element is affixed.
5. Is Debossing a Good Fit for Your Brand?
Debossing offers distinct advantages but also comes with specific considerations. Evaluating these points will help determine if this technique aligns with your brand’s aesthetic, budget, and production needs.
5.1 The Upsides: Why Choose Debossing?
- Subtle Elegance: Creates a sophisticated, understated look that avoids overt flashiness, conveying a sense of refinement and elegance.
- Enhanced Tactile Appeal: Adds a unique textural dimension that invites touch, making your branding elements more engaging and memorable.
- Improved Quality Perception: The distinct finish and textural detail often elevate the perceived value and quality of the product it adorns.
- Impression Durability: The sunken nature of the design provides inherent protection against surface wear, especially effective on robust materials like leather or thick cardstock.
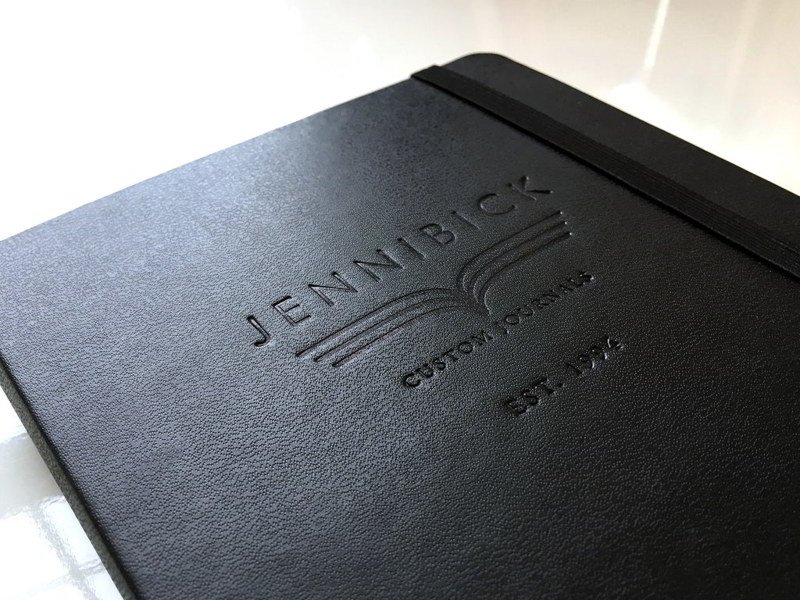
5.2 Potential Downsides & Things to Keep in Mind
- Cost Considerations: Generally involves higher setup (die creation) and per-piece costs compared to standard flat printing methods due to the specialized equipment and additional process step.
- Design Limitations: Not ideal for extremely fine lines, intricate details, or very small text, as these elements may lose clarity or fill in within the recessed area.
- Material Requirements: Achieves the best results on thicker, firmer materials (heavy cardstock, leather); less impactful or unsuitable for very thin or flexible substrates.
- Process Specificity: Requires specialized machinery and expertise, potentially limiting supplier options or adding turnaround time compared to simpler printing techniques.
6. Related Questions
6.1 Can you deboss directly onto clothing fabric?
No, debossing is generally not feasible directly onto typical clothing fabric like cotton jersey, polyester weaves, or denim. These materials lack the necessary firmness, structural integrity, and density to hold a crisp, permanent debossed impression. The process requires a more rigid substrate – materials such as heavy paper, cardstock, leather, faux leather, or specially constructed thick patches possess the stability needed for the die to create and maintain a clear indentation.
6.2 Is debossing or stamping better for leather patches?
The choice between debossing and stamping for leather patches depends largely on the desired aesthetic and level of detail. Debossing, often utilizing controlled heat and pressure, typically allows for finer detail, sharper edges, and more consistent depth, resulting in a more refined appearance.
Stamping, which may sometimes use only pressure or simpler heat application, can be more cost-effective for basic logos or text but might yield softer edges or less uniformity, particularly with intricate designs. Laser engraving offers another alternative, burning the design into the leather for a different textural and visual effect.
6.3 What kind of detail works best with debossing?
For the clearest results with debossing, designs featuring clean, reasonably bold lines, distinct logos or icons, and medium-weight typefaces are most effective. Overly complex patterns, extremely fine lines, or very small, delicate text should be avoided, as these details risk becoming illegible or filling in within the recessed area. Crucially, ensuring sufficient spacing between design elements helps maintain definition and allows the debossed effect to stand out visually.
6.4 Does debossing cost more than regular printing?
Yes, generally debossing does incur a higher cost than regular flat ink printing. There are two primary reasons for this: first, debossing requires the creation of a custom metal die specifically tooled for your design, which represents an initial setup expense.
Second, debossing is an additional production step performed *after* any standard printing, requiring a separate machine process and handling. These factors contribute to both the setup and per-item costs being higher than printing alone.
Read more:
Debossing stands out as a distinctive finishing technique, creating a sunken impression that adds a layer of subtle sophistication to apparel branding elements. By introducing unique texture and depth, primarily to items like hang tags and leather patches, this method offers brands a way to enhance perceived value and cultivate a refined aesthetic.
The unique tactile impression it provides serves as a memorable differentiator in a visually crowded market. Carefully consider how the understated elegance of debossing might align with and elevate your specific brand identity. Exploring this technique further with finishing specialists can help determine the best way to incorporate this impactful detail into your products.