For apparel business owners navigating the world of garment trims, selecting the appropriate label finish can be intricate. Understanding options such as the straight cut label is fundamental, influencing factors ranging from production cost and durability to the overall brand presentation and specific sewing application requirements.
This article serves to clarify the nature of the straight cut label, delving into its features, benefits, drawbacks, and suitable applications. The goal is to empower apparel business owners like you to ascertain whether this straightforward yet adaptable choice among label finishes aligns with the needs of your clothing line, providing insights into its manufacturing, usage, and impact on both budget and the final product.
1. What exactly is a straight cut label in apparel?
A straight cut label, in the context of apparel trims, is essentially a label finished with simple, straight edges on all four sides, without any folds. Think of it as a small, flat rectangle of fabric or other material, cut precisely to size. This simple finish distinguishes it clearly from other common label types.
Unlike a folded cut label (which includes styles like end fold or center fold, where edges are tucked under) or a die cut label (which is custom-shaped, perhaps matching a logo’s outline), the straight cut label maintains its basic rectangular form.
These labels can be produced as either woven labels, typically crafted from polyester thread (materials like taffeta are common), or as printed labels, frequently utilizing satin labels or sometimes natural materials like cotton fabric. The defining characteristic remains its uncomplicated, straight-edged perimeter, making it a fundamental option in label finishing.
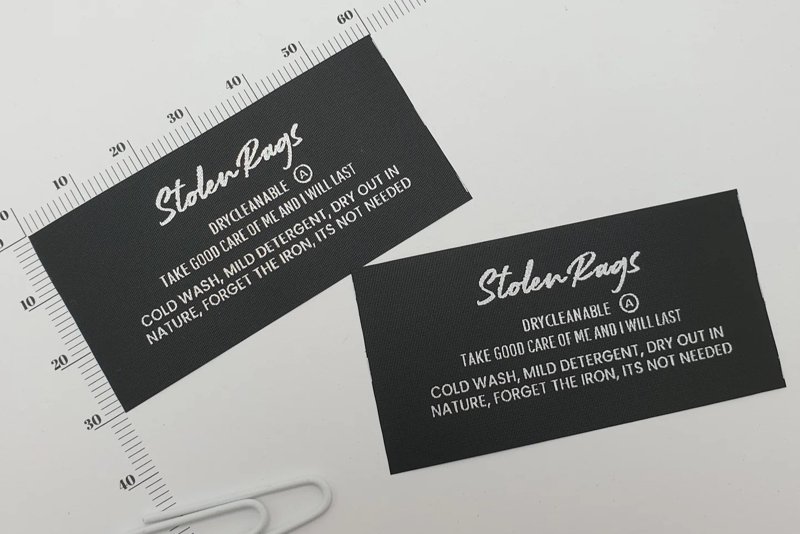
2. How straight cut labels are made
The characteristic clean edge of most straight cut labels, especially those made from synthetic materials like woven polyester or printed satin, is typically achieved through a process called heat cut or hot knife cut. This method utilizes a heated blade or wire (part of a heat cutting machine) that slices through the label material.
The intense heat melts and fuses the synthetic fibers along the cut line simultaneously. This heat sealing action is crucial because it effectively prevents the label edge from unraveling or fraying, significantly contributing to label durability once sewn onto a garment. A properly executed heat cut results in a sealed, slightly firm edge.
Alternatively, labels can be finished using cold cutting (a simple blade cut without heat). However, for synthetic materials prone to fraying, this method is generally less desirable as the edges remain raw and can easily unravel unless carefully sewn into a seam on all sides.
Cold cutting is more appropriate for natural fiber labels where heat sealing wouldn’t work or isn’t necessary. Regardless of the method, quality control is important to ensure the cut is clean, precise, and, in the case of heat cutting, properly sealed to prevent future fraying.
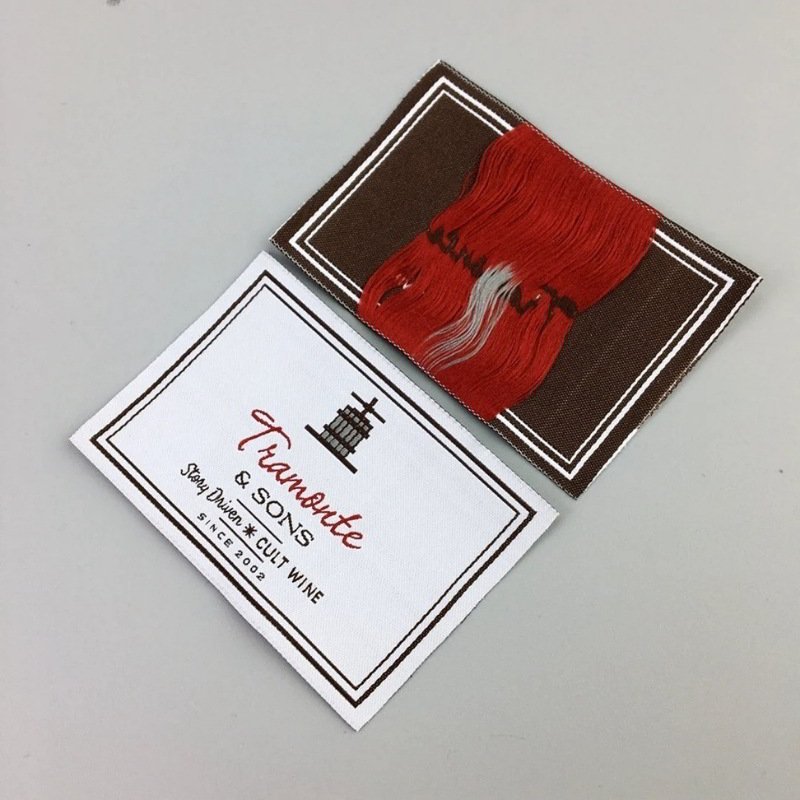
3. Why choose straight cut labels?
Choosing the right label finish involves weighing several factors. Straight cut labels offer distinct benefits that make them a practical choice for many apparel businesses:
- Cost-effectiveness: This is often the primary advantage. The simple finish requires less processing compared to folded or shaped labels. The cutting process is straightforward, leading to lower manufacturing costs. This makes straight cut labels a particularly economical cutting option, especially beneficial when placing bulk label orders.
- Production efficiency: The simplicity of the straight cut translates directly into faster production speed. Less complex machinery and fewer steps are involved in the finishing process, allowing for quicker turnaround times from label manufacturers.
- Flat application: Because they have no folds, straight cut labels lie completely flat. This makes them ideal for sewing directly onto flat application areas of a garment or accessory, such as the surface of a pocket, the inside waistband, or as a hem tag. The flat profile simplifies the sewing process in these contexts.
- Versatility in specific uses: While simple, they are versatile for certain essential functions. They are commonly used for care labels and informational tags placed inside seams or less visible areas. They can also serve as basic brand labels when complex folding isn’t necessary or desired for the design aesthetic.
4. Potential disadvantages & considerations
While straight cut labels offer practicality, it’s important to consider their potential drawbacks to ensure they fit your specific needs:
- Sewing requirements: Unlike folded labels where raw edges are hidden, straight cut labels require careful label application methods. If applied flat onto a surface (not tucked into a seam), all four edges ideally need stitching down to prevent lifting or curling over time. When inserting into a sewing seam, sufficient sewing allowance must be planned for on the edges being caught in the stitch line to secure them properly.
- Edge feel/comfort: The heat-sealed edge, necessary for preventing fraying on synthetics, can sometimes feel slightly stiff or even scratchy against sensitive skin. This is a significant factor impacting garment comfort, particularly for labels placed in direct skin contact areas, like a neck label. For these locations, softer folded labels are often preferred.
- Fraying risk (if improperly handled): Although heat sealing minimizes fraying, an imperfect seal or rough handling during sewing or wear can still potentially lead to a fraying edge over time. Furthermore, if not securely sewn down on all sides when applied flat, the corners are vulnerable.
- Aesthetic simplicity: The straightforward, flat appearance might be perceived as less premium compared to folded or intricately shaped labels. Depending on your brand perception goals, this basic look may or may not align with your desired aesthetic. Some brands prefer the dimensional quality and cleaner edge presentation offered by other finishing types.
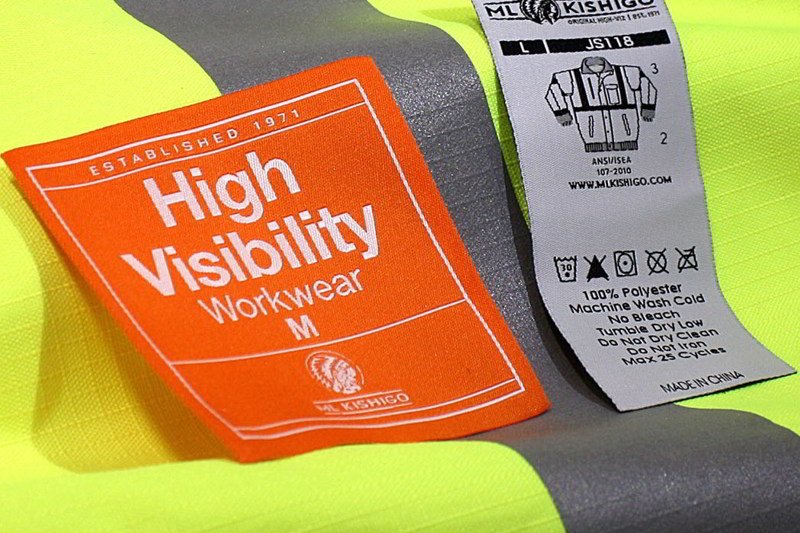
5. Ideal placements & use cases for straight cut labels
Understanding where a straight cut label excels is key to leveraging its benefits effectively. Their flat nature and simple finish make them well-suited for specific label placement scenarios within garment trim applications:
- Inside seams: This is a very common use. Labels can be easily inserted and sewn into seam allowances during garment construction. Typical locations include the side seam label in shirts or trousers, or inside waistbands. Here, the potentially firmer edge is hidden and doesn’t impact comfort.
- Flat surface application: Ideal for areas where the label needs to lie flush against the fabric without bulk. Think of applications on external pockets of bags or jackets, inside linings, or even as a hem tag sewn flat near the bottom edge of a garment. Secure stitching on all sides is recommended for these exposed flat surface placements.
- Information/care labels: Straight cut labels are a standard choice for care label and content labels. Their cost-effectiveness and ability to hold necessary text make them practical for conveying legally required information, often placed discreetly inside the garment. This is a frequent use case for this type of apparel tag.
- Budget-conscious projects: When cost is a primary concern, the lower manufacturing expense of straight cut labels makes them an attractive option compared to more complex folded or die-cut finishes.
- Specific aesthetic choices: Sometimes, the simple, straightforward look of a straight cut label is desired for a particular brand aesthetic, perhaps aiming for a more utilitarian or minimalist feel in clothing tag placement.
6. Straight cut vs. other finishes
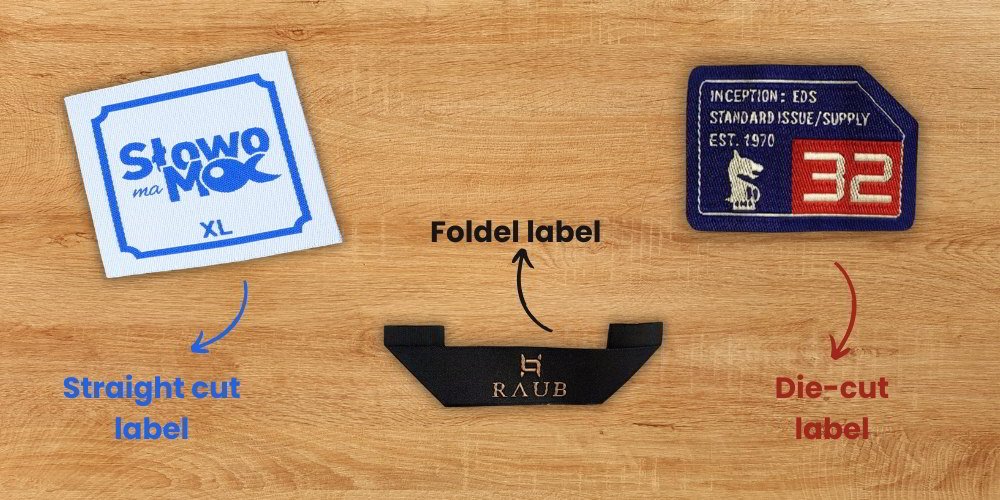
Choosing the right label finish involves understanding how straight cut compares to other common label finishing options. Here’s a brief overview:
- Straight cut vs. end fold: An end fold label has the short ends folded underneath before cutting. This creates softer side edges compared to the heat-sealed straight cut, often improving comfort, especially for neck labels. The fold provides extra material for sewing, making application arguably easier in some cases. However, end folding adds a step, slightly increasing the label cost compared to a basic straight cut. The visual is slightly thicker due to the folds.
- Straight cut vs. center fold: A center fold label is folded in half (like a small booklet) and usually sewn into a seam along the folded edge. This hides all raw edges within the fold or seam, offering a very clean look and good comfort. Often used for brand labels at the neck or care labels in side seams. The cost is generally comparable to or slightly higher than end fold, but definitely more than straight cut due to the folding process. Center folds inherently take up less horizontal space once sewn compared to a flat straight cut label of the same initial width.
- Straight cut vs. die cut/laser cut: Die cut or laser cut labels are custom-shaped, often matching a logo’s contour or creating unique forms. This offers maximum design flexibility and can significantly enhance brand identity elements. However, the process is much more complex and involves custom tooling (for die cuts) or precise laser programming, making these the most expensive options among common finishes. The edge finish can vary (heat-sealed for laser cut synthetics, potentially raw for die-cut naturals), and application depends heavily on the shape. Straight cut is far simpler and more economical.
Ultimately, the decision hinges on balancing factors like budget, required comfort level, intended label placement, and the desired brand aesthetic. Straight cut excels in simplicity and cost-effectiveness for specific applications, while folded and custom cuts offer enhanced comfort, different visual presentations, or unique branding opportunities at a higher price point.
Comparison Summary Table:
Cut Type | Edge Finish | Typical Comfort | Relative Cost | Key Feature |
---|---|---|---|---|
Straight cut | Heat-sealed (synthetics) or raw | Basic to moderate | Lowest | Simple, flat, economical |
End fold | Ends folded under, sides cut/sealed | Moderate to good | Low to medium | Softer side edges |
Center fold | Folded in half, raw edges hidden | Good to very good | Low to medium | Compact, clean |
Die/Laser cut | Cut to custom shape, sealed/raw | Varies by shape/edge | Highest | Unique shape, branding |
7. Related questions
7.1 Can straight cut labels be ironed on?
Whether a label can be iron-on depends entirely on whether an adhesive backing (a heat-activated glue layer) is applied to it after it has been produced and cut, not on the cut type itself. Therefore, a straight cut label certainly can be made into an iron-on label if the manufacturer adds this specific backing. The straight cut finish itself doesn’t prevent this application method.
7.2 What’s the minimum order quantity (MOQ) usually?
The minimum order quantity (MOQ) for clothing labels can vary widely among different suppliers. Factors influencing the MOQ include the label material, size, complexity, and the supplier’s production capacity. However, because straight cut labels involve a simpler finishing process compared to folded or die-cut options, they often have lower or more flexible MOQs, making them accessible for businesses ordering smaller batches. Always confirm the specific MOQ directly with your chosen label suppliers.
7.3 How much sewing allowance is needed?
Adequate sewing allowance is essential when integrating a straight cut label into a seam. A general guideline is to provide at least 1/4 inch (approximately 5-7mm) of extra material on the edge or edges that will be stitched into the garment’s seam.
This ensures the label is securely caught. The exact allowance might need adjustment based on the specific garment construction, the thickness of the fabrics involved, and the precision of the sewing operation. Consider how the label will be attached during the design phase.
Read more:
In essence, the straight cut label represents a fundamental choice in label finishing, characterized by its simplicity, flat profile, typically heat-sealed edges (for synthetics), and significant cost-effectiveness. Its primary advantages lie in production efficiency and suitability for flat applications or insertion into seams.
However, considerations regarding the required application method (potentially needing all sides stitched if applied flat), potential impact on garment comfort due to edge feel, and the need for adequate sewing allowance are crucial.
Ultimately, determining the optimal choice among label finishes is highly context-dependent. There isn’t a single “best” type; the right decision hinges on your specific garment design, intended label placement, budget constraints, and the overall brand identity you wish to project.
Weighing the pros and cons of the straight cut against alternatives like folded or die-cut labels, in light of these factors, will guide you to the most suitable solution for your apparel branding components. If you remain uncertain about which label type best serves your needs, seeking expert advice can provide valuable clarity and ensure your final selection aligns perfectly with your product and brand goals.