Are you exploring the world of garment decoration and looking for the perfect printing method? Perhaps you’re seeking an alternative to traditional techniques like screen printing or DTG, or maybe you’re simply curious about the latest innovations in textile printing. If you’re unfamiliar with Direct-to-Film (DTF) printing, you’re in the right place.
Choosing the wrong printing method can result in subpar quality, inflated costs, and production bottlenecks. This makes understanding your options, like DTF, essential for making informed decisions. This comprehensive guide introduces you to the world of DTF printing.
You’ll gain a clear understanding of the process, its advantages and disadvantages, and how it stacks up against other popular printing methods. By the end, you’ll be equipped to assess whether DTF printing is the right solution for your specific garment decoration needs, whether you’re a business owner, a DIY enthusiast, or simply curious about this versatile technology.
1. What is DTF printing? A detailed explanation
1.1 The DTF printing process: Step-by-step
- Printing: The design is printed onto a special PET film using specialized DTF pigment inks. It’s crucial to use DTF-specific inks, not regular inkjet inks. A layer of white ink is typically printed as a base, especially important for vibrant transfers on dark fabrics. Some DTF printers can print color and white ink simultaneously, while others require separate passes.
- Powder application: After printing, a hot-melt adhesive powder is applied evenly over the wet ink. This powder only adheres to the printed areas. Different types of powder exist (white and black being common), chosen based on the fabric color and desired feel.
- Shaking and curing: Excess powder is carefully shaken off. Then, the film undergoes a crucial curing process. This involves melting the adhesive powder, either by hovering a heat press (without clamping down) over the film or, preferably, using a curing oven. Proper curing, typically around 150-170°C (300-340°F) for 1-3 minutes, is essential for the print’s durability.
- Heat transfer: The cured film, now carrying the design, is placed onto the fabric, and a heat press is used to transfer the design. Typical settings range from 150-170°C (300-340°F) with medium to high pressure for 10-20 seconds, but these can vary. Explore more heat transfer labels here!
- Cold peel: After heat pressing, the transfer must be allowed to cool completely – this is known as cold peeling. This step is vital; peeling the film while hot can lift the design from the fabric.
Always follow the ink and powder manufacturer’s recommendations for specific settings, as these can vary.

1.2 Essential equipment and supplies for DTF printing
To successfully execute the DTF printing process, you’ll need the following:
- DTF printer: These are often modified inkjet printers specifically designed to handle DTF inks and PET film.
- Heat press: A good quality heat press that provides even heat distribution and consistent pressure is essential for successful transfers.
- PET film: This special film comes in various types (single-sided, double-sided, rolls, and sheets). Choose the type that best suits your printer and project needs.
- DTF inks: These are pigment-based inks specifically formulated for DTF printing.
- Adhesive powder: As mentioned earlier, different types (white, black) are available for different applications.
- Curing oven (Optional but Recommended): While a heat press can be used for curing, a dedicated curing oven provides more consistent and even heat distribution, leading to better results.
2. Advantages of DTF printing
2.1 Versatility: Printing on almost any fabric
One of DTF printing’s greatest strengths is its exceptional versatility. Unlike some other printing methods (like DTG, which works best on cotton), DTF can be used to print on a remarkably wide range of materials. This is because the adhesive powder used in the DTF process bonds directly to the fabric, rather than relying on a chemical reaction with specific fibers. You can successfully print on cotton, polyester, blends, nylon, leather, denim, and many other materials.
2.2 High-resolution prints with vibrant colors and fine detail
DTF printing is capable of producing high-resolution prints with vibrant colors and fine detail. The print quality is often comparable to that achieved with DTG, allowing for intricate designs, gradients, and even photographic images. This makes DTF a versatile option for a wide range of design styles.
2.3 No pre-treatment required: Saving time and money
A significant advantage of DTF printing over DTG is that it eliminates the need for pre-treatment of the fabric. In DTG printing, fabrics (especially darker ones) require a pre-treatment solution to be applied and dried before printing. This adds an extra step to the process, increasing both time and cost. DTF’s no pre-treatment required workflow streamlines production and reduces expenses.
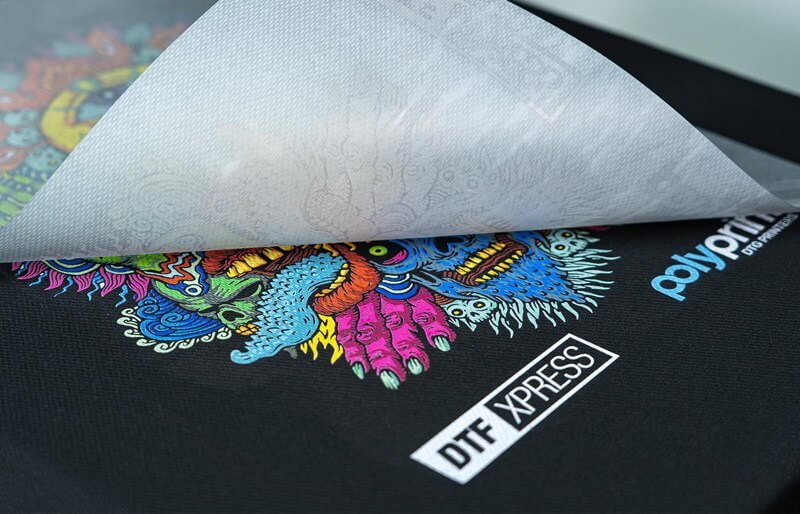
2.4 Durable and washable prints
When applied and cured correctly, DTF prints are known for their durability and washability. They can withstand repeated washing without significant fading or cracking. However, proper curing during the transfer process is crucial for achieving optimal durability. To maximize the lifespan of DTF-printed garments, it’s recommended to wash them inside out in cold water on a gentle cycle and avoid harsh detergents or bleach.
2.5 Cost-effectiveness for small to medium production runs
DTF printing is particularly cost-effective for small to medium production runs. Unlike screen printing, which requires expensive screen setup for each design, DTF has no such setup costs. This makes it an economical choice for printing small batches of custom garments or for testing out new designs without a large upfront investment. It can also be competitive for medium-sized runs, depending on the specific project requirements.
3. Disadvantages of DTF printing
3.1 The “hand feel”: Addressing the plasticized feel
One common concern with DTF printing is the potential for a slightly “plasticized” feel, particularly with large, solid areas of print. This is due to the adhesive powder and the layer of ink that sits on top of the fabric. However, this can be minimized through several techniques:
- Using high-quality adhesive powder: “Soft-hand” powders are specifically designed to create a softer feel.
- Using the correct amount of powder: Applying too much powder can contribute to a stiffer feel.
- Proper curing: Over-curing can make the print feel harder and more plastic-like.
- Choosing lighter-colored fabrics: Lighter fabrics require less white ink, which can reduce the overall thickness and feel of the print.
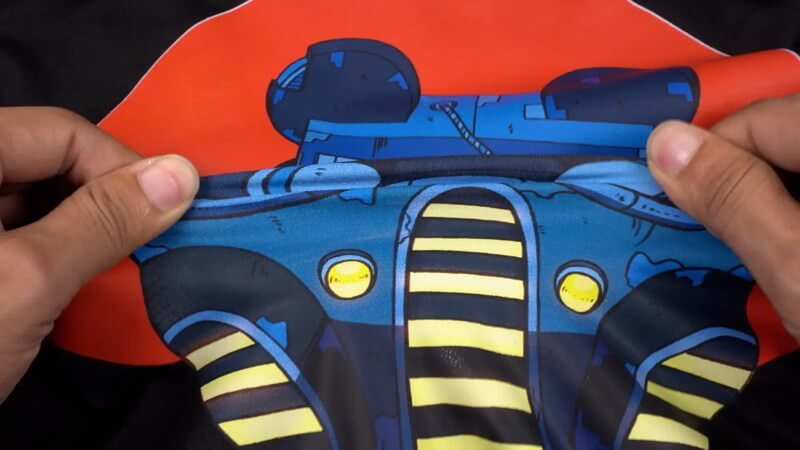
3.2 Slower than screen printing for very large orders
While DTF is cost-effective for small to medium runs, screen printing remains the most efficient method for very large orders (thousands of prints). The screen printing process, once set up, allows for rapid, high-volume production. DTF, being a digital printing method, is inherently slower for mass production.
3.3 The learning curve: Mastering the process
Although DTF printing is relatively easy to learn compared to some other garment decoration methods, there is a learning curve to achieving consistent, high-quality results. Mastering the process involves understanding the optimal printer settings, powder application techniques, curing parameters, and heat pressing procedures. It takes practice and experimentation to fine-tune these variables for different fabrics and designs.
3.4 High initial equipment costs
This method requires a significant initial investment for specialized printers, adhesive films, and inks. This can be a barrier to entry for those starting out with limited capital.
4. DTF printing vs. other printing methods: A detailed comparison
To make an informed decision, it’s helpful to compare DTF printing to other popular garment decoration techniques.
4.1 DTF vs. dtg (direct-to-garment)
Feature | DTF | DTG |
Fabric Compatibility | Almost any fabric | Best for cotton and high-cotton blends |
Pre-treatment | No pre-treatment required | Pre-treatment required (especially darks) |
Hand Feel | Can be slightly plasticized | Generally softer |
White Ink | Handles white ink easily on dark fabrics | Can be more challenging on dark fabrics |
Cost | More cost-effective for small/medium runs | Can be more cost-effective for large runs on cotton |
Durability | Good, if applied and cured correctly | Good, if applied and cured correctly |
Summary: DTF offers greater fabric versatility and eliminates the need for pre-treatment, making it a more streamlined process. DTG often provides a softer hand feel, but is more limited in fabric compatibility.
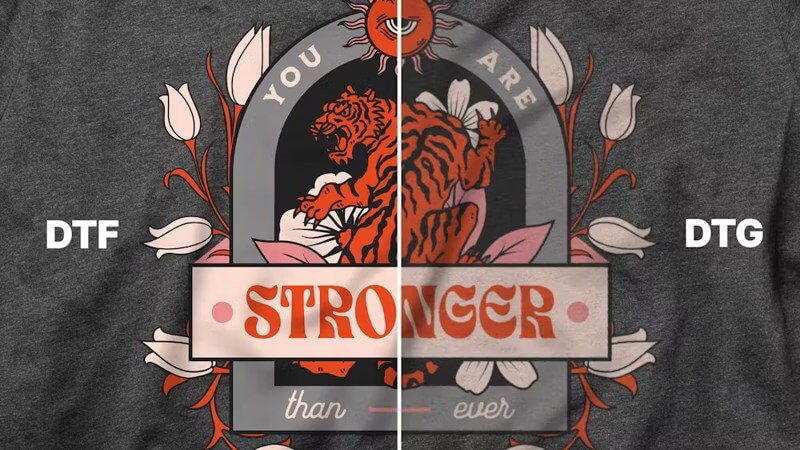
4.2 DTF vs. screen printing
Feature | DTF | Screen Printing |
Setup Costs | No setup costs | Significant setup costs per color/screen |
Order Quantity | Ideal for small to medium runs | Ideal for very large runs |
Design Complexity | Handles complex, full-color designs | Better for simpler designs, fewer colors |
Hand Feel | Can be slightly plasticized | Varies depending on ink type |
Cost | More cost-effective for small/medium runs | More cost-effective for very large runs. |
Summary: DTF excels in low-volume, complex designs due to its lack of setup costs. Screen printing is more efficient and economical for high-volume, simpler designs.
4.3 DTF vs. sublimation
Feature | DTF | Sublimation |
Fabric Compatibility | Almost any fabric | Limited to polyester and polymer-coated items |
Hand Feel | Can be slightly plasticized | No hand feel (ink infuses into fabric) |
Color | Vibrant, good color reproduction | Extremely vibrant, especially on white |
Durability | Very durable | Very durable |
Summary: DTF’s primary advantage over sublimation is its fabric versatility. Sublimation offers a completely soft hand feel and exceptional vibrancy, but is restricted to specific materials.
4.4 DTF vs. heat transfer vinyl (htv)
Feature | DTF | Heat Transfer Vinyl |
Design Complexity | Full color, complex design | Simpler designs with solid color |
Hand Feel | Can be slightly plasticized | Varies on vinyl type |
Weeding | No weeding | Required weeding |
Summary: DTF allows for much more complex and full-color designs than HTV. It also eliminates the time-consuming weeding process required with HTV.
5. Faqs about DTF printing
5.1 Can DTF printing be used on dark fabrics?
Yes, DTF printing works exceptionally well on dark fabrics. A layer of white ink is printed first, acting as a base for the colored inks. This allows for vibrant and opaque colors to be printed on even the darkest materials.
5.2 What is the lifespan of a DTF print?
With proper care, DTF prints can be very durable and long-lasting. They can withstand many washes without significant fading or cracking. The exact lifespan depends on several factors, including the quality of the DTF inks, adhesive powder, and the precision of the application and curing process. Always follow care instructions (washing inside out in cold water on a gentle cycle) to maximize the print’s longevity.
5.3 Is DTF printing eco-friendly?
The eco-friendliness of DTF printing depends on the specific materials used. Some suppliers offer eco-friendly, water-based DTF inks and recyclable PET film. Choosing these options can significantly reduce the environmental impact of the process. It’s always best to inquire about the sustainability practices of your chosen supplier.
5.4 Can i use a regular inkjet printer for DTF printing?
No, a regular inkjet printer cannot be used for DTF printing. DTF printing requires a specialized DTF printer. These printers are modified to handle the thicker PET film and use specialized DTF pigment inks that are formulated to work with the adhesive powder and heat transfer process. Regular inkjet printers use dye or pigment inks that are not compatible with DTF.
5.5 What kind of designs are best for DTF printing?
One of the greatest strengths of DTF printing is its design versatility. It can handle virtually any design, including photographs, intricate logos, gradients, fine text, and complex, full-color illustrations. This makes it a highly adaptable printing method for a wide range of creative applications.
6. Packlove – Providing DTF printing service
While Packlove’s primary expertise lies in crafting high-quality custom woven labels, tags, zipper bags, and poly mailers, we understand that garment decoration often requires a multifaceted approach. With over 8 years of experience in the garment industry, we’ve built strong relationships with trusted partners.
Therefore, while we don’t offer in-house DTF printing, Packlove can connect you with reputable DTF printing partners who meet our rigorous standards for quality, reliability, and customer service. We leverage our industry expertise to help you find the right printing solution for your specific needs, ensuring your garments are decorated to the highest standards.
Contact us today to discuss your project and explore how we can assist you in finding the perfect DTF printing partner: Packlove
Read more:
DTF printing offers a compelling combination of versatility, quality, and cost-effectiveness, making it an excellent option for many garment decoration projects. It’s particularly well-suited for small to medium runs, intricate designs, and a wide variety of fabrics. However, it’s essential to weigh the pros and cons, consider your specific needs, and invest in quality equipment and supplies to achieve optimal results.