For small clothing businesses striving to make their mark, grappling with inconsistent sizing, generic styles that blend into the crowd, and the unexpected costs of endless alterations can be significant hurdles. Mastering custom patterns offers a powerful way to gain control over these critical aspects of your brand.
High-quality pattern making is foundational to achieving a consistent fit that delights customers and minimizes returns. Furthermore, developing your own patterns unlocks the potential for truly unique designs that differentiate your clothing brand and establish a distinct identity. Effective garment construction begins with a precise blueprint.
1. What exactly is clothes pattern making?
1.1 Defining the pattern: The blueprint for your garments
In sewing and garment construction, a pattern serves as the essential blueprint. Think of these sewing patterns as detailed templates, traditionally drawn on paper, that represent every individual piece needed to create an article of clothing.
The pattern dictates the precise shape and dimensions for cutting the fabric and includes crucial markings that guide the assembly process, ensuring all components connect correctly to form the final garment.
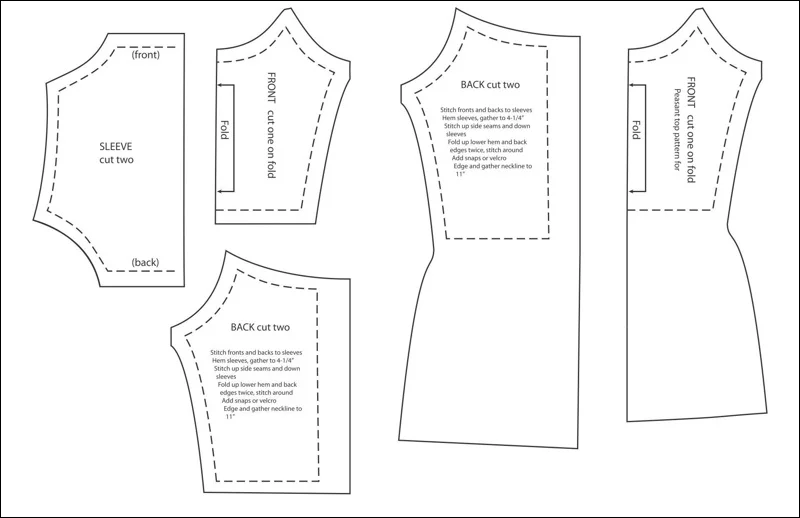
1.2 Why it matters for small brands like yours
For small brands, investing time or resources into developing proper patterns yields significant advantages that directly impact business success and brand identity:
- Consistent sizing: Well-drafted patterns are fundamental for achieving consistent sizing across different production batches or when working with multiple sewers. This consistency builds customer trust, reduces return rates, and is a cornerstone of effective quality control.
- Unique designs: Creating proprietary patterns empowers you to bring unique designs to life. This ability to offer distinct styles helps solidify your brand identity and differentiates your products in a crowded marketplace.
- Superior garment fitting: Custom patterns allow for tailoring the fit specifically to your target customer demographic, moving beyond generic industry standards. Offering a demonstrably better garment fitting experience can become a powerful selling point and foster customer loyalty.
- Improved cost management: While developing patterns requires an initial investment, accurate patterns minimize costly errors during cutting and sewing in apparel manufacturing. Reducing fabric waste and the need for extensive post-production alterations contributes positively to long-term cost management.
2. Core methods: Understanding flat pattern drafting vs. draping
2.1 Flat pattern drafting: Precision from a blueprint
Flat pattern drafting is a method that translates body measurements into a two-dimensional pattern on paper. The process typically starts with a foundational template called a sloper or block (a basic, fitted pattern without seam allowance or design ease, customized to specific measurements).
Using precise measurement taking and applying principles of geometry, pattern makers manipulate these blocks – employing techniques like dart manipulation (moving darts to shape the fabric over body curves) and slash and spread (cutting and spreading or overlapping the pattern to add fullness or contouring) – to create the desired garment style. This is one of the fundamental pattern drafting techniques.
Key tools for this method include various rulers (straight grid rulers, L-squares), specialized curves (french curve, hip curve) for shaping armholes and necklines, pattern paper (often sturdy manila paper), pencils, erasers, and measuring tapes.
- Pros: High accuracy and repeatability, excellent for achieving consistent sizing, well-suited for structured garments (like trousers or tailored jackets), relatively easier to grade into multiple sizes.
- Cons: Can feel less intuitive for highly fluid or organic shapes, requires a solid understanding of technical skill and drafting principles.
2.2 Draping: Sculpting fabric in 3D
Draping, in contrast, is a three-dimensional approach. This technique involves manipulating fabric, typically inexpensive muslin, directly onto a dress form that represents the intended body size and shape. Using pins, the designer sculpts the fabric, creating style lines, darts, and pleats directly on the form.
Once the desired look is achieved, crucial lines and points are marked onto the muslin using specialized marking tools. The shaped muslin is then carefully removed from the form, laid flat, and transferred onto paper to create the final pattern pieces. Essential tools include the dress form, muslin, plenty of pins, marking pencils or chalk, and sharp fabric shears.
Draping techniques allow for immediate 3D visualization of how the fabric will behave and drape.
- Pros: Excellent for developing designs with complex or organic shapes where drape is crucial, allows for a highly creative and visual process, facilitates achieving a custom fit directly on the form, often associated with couture techniques.
- Cons: Requires a correctly sized dress form, may initially be less precise for exact repeatability compared to flat drafting (though the resulting paper pattern establishes this), can be slower for developing basic block patterns.
2.3 Choosing the right method for your business needs
The optimal choice between flat pattern drafting and draping often depends on your specific business needs, product type, and brand aesthetic.
- Flat pattern drafting is generally more efficient for foundational garments requiring consistency and precision, such as trousers, skirts, basic shirts, and outerwear. Its strengths in accuracy and grading make it ideal for items produced in multiple sizes.
- Draping excels when creating unique, flowing, or intricately shaped garments like evening gowns, bias-cut pieces, or experimental designs where visualizing the fabric’s behavior in 3D is paramount.
Many professional pattern makers utilize a hybrid approach, perhaps developing a base structure using flat pattern drafting techniques and then refining specific design elements or achieving a particular drape through draping. Consider the types of garments central to your brand and the skills you or your team possess or plan to develop when deciding which method(s) to prioritize.
3. Essential toolkit: Gathering your pattern making supplies
3.1 Must-have tools for flat pattern drafting
Equipping yourself with the right pattern making tools is crucial for accuracy in flat drafting. Here are the essentials to get started:
- Grid ruler: A clear plastic ruler with grid markings (often 18″ or 24″ long and 2″ wide) is indispensable for drawing straight lines and measuring accurately.
- Curves (french curve, hip curve): These specialized rulers help draw smooth, curved lines for areas like necklines, armholes, and hip lines.
- Pattern paper: Large rolls or sheets of paper are needed to draft the patterns. Manila pattern paper (a sturdy, buff-colored paper) is a common professional choice, but craft paper or plotter paper can also work.
- Mechanical pencil and eraser: A sharp pencil (0.5mm lead is good) allows for precise lines, and a quality eraser is vital for making corrections cleanly.
- Measuring tape: A flexible fiberglass or plastic tape measure is necessary for taking body measurements and measuring pattern pieces. Ensure it doesn’t stretch.
- Paper scissors: Dedicate a pair of scissors only for cutting paper patterns. Using fabric shears on paper will dull them quickly.
- Awl: A pointed tool used to punch small holes through pattern paper, often for marking dart points or pocket placements that need to transfer accurately to fabric.
- Tape: Clear tape (like Scotch tape) is useful for joining paper pieces or making pattern adjustments.
3.2 Essential tools for draping (if pursuing)
If you plan to explore draping, you’ll need these additional tools specifically suited for working in three dimensions:
- Dress form: A pinnable mannequin representing the size and shape you intend to design for. The quality and accuracy of the dress form significantly impact the results.
- Muslin: Inexpensive, plain-weave cotton fabric used for draping mock-ups. Choose a weight similar to your intended final fabric.
- Pins: Plenty of sharp dressmaker pins are needed to secure the muslin to the form and create style lines.
- Marking tools: Fabric marking pencils, chalk, or disappearing ink pens specifically designed for marking on fabric.
- Fabric shears: Sharp scissors dedicated only to cutting fabric.
- Twill tape: Narrow woven tape often used to define key style lines (like waistline, center front/back) directly on the dress form for guidance.
3.3 Sourcing your tools & initial investment
You can find pattern making supplies through various channels, including professional sewing suppliers online, local sewing machine dealers, art supply stores, and sometimes even office supply stores for basic paper and pencils. Sourcing tools represents an upfront investment in your brand’s capability.
While it’s tempting to start with the cheapest options, prioritizing quality for key items like rulers, curves, and especially a dress form (if draping) will pay off in accuracy and longevity. View these tools as a necessary business cost that enables better product development.
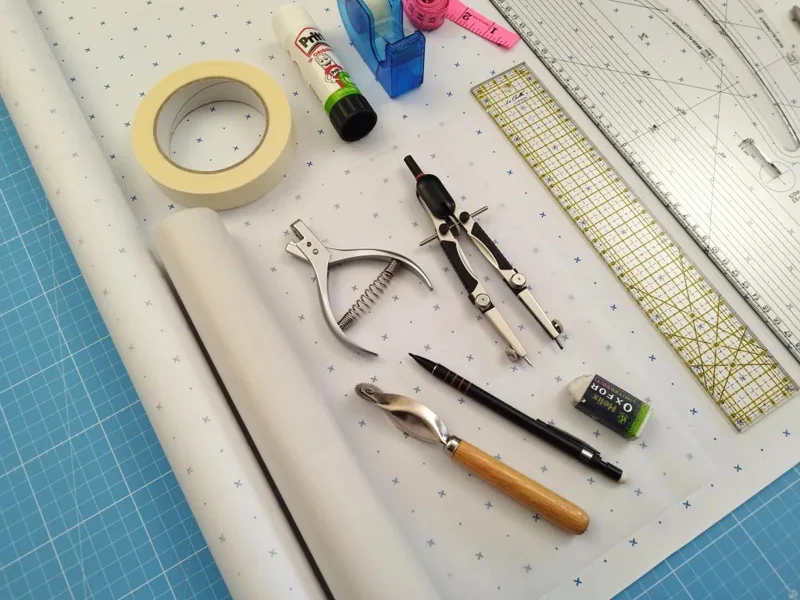
4. The pattern making journey: Skills, time, and first steps
4.1 Key skills and mindset: Beyond just sewing
While sewing skills are related, pattern making demands a distinct set of abilities and a specific mindset. Success hinges on precision and meticulous accuracy; even small errors on the pattern can lead to significant fit issues in the final garment.
A comfort level with basic math and geometry, particularly fractions and spatial reasoning, is essential for calculating measurements and manipulating shapes. Beyond the technical aspects, patience is paramount. Pattern making is often an iterative process involving drafting, testing, and refining.
Cultivating a methodical problem-solving approach is key, as you’ll inevitably encounter challenges that require careful analysis and adjustment. This is a technical skill that rewards attention to detail and persistence.
4.2 Realistic time investment for proficiency
Learning pattern making requires a significant time investment and consistent practice. Don’t expect to master complex designs overnight. Drafting even a basic sloper pattern accurately often involves several attempts and refinements. Creating muslin mock-up garments to test the fit and making necessary adjustments can take days or weeks, especially initially.
Achieving genuine proficiency – the ability to confidently draft and adjust patterns for various designs – typically develops over months of dedicated effort and application. Understand that there is a definite learning curve; embrace the process and allow yourself the necessary time commitment to build solid foundational skills.
4.3 A recommended learning path for business owners
For business owners aiming to incorporate pattern making skills, a structured approach is most effective. Here’s a suggested learning path:
- Solidify sewing basics: Ensure you have strong fundamental sewing skills. Understanding garment construction helps you visualize how pattern pieces come together.
- Master accurate measurement taking: Learn the precise techniques for accurate measurement taking on the body. This is the bedrock of good pattern drafting.
- Draft basic slopers: Using a reputable pattern making book or pattern drafting tutorial, focus on drafting your first basic sloper set (bodice, skirt, and perhaps sleeve) based on accurate measurements.
- Sew muslins & learn basic fitting: Create muslin mock-ups from your slopers. Learn the fundamentals of evaluating fitting and making common fitting adjustments directly on the muslin or translating them back to the paper pattern. This step is crucial for understanding how the 2D pattern translates to a 3D form.
- Practice simple pattern manipulations: Once comfortable with slopers and basic fitting, begin experimenting with simple pattern manipulations like moving darts or adding basic fullness, following guidance from your chosen learning resource (online courses focusing on pattern making can also be helpful here).
5. Foundational techniques demystified
5.1 Working with slopers/blocks: Your base camp
Slopers or blocks represent the foundational base template in pattern making. These are core patterns meticulously drafted to specific body measurements, capturing the basic shape of the torso, skirt, sleeve, or trousers with a close fit.
Crucially, a true sloper is a foundation pattern created without design ease (extra room for comfort or style) or seam allowance (the fabric added beyond the stitching line for construction). All other designs are developed by manipulating these fundamental blocks.
5.2 Dart manipulation: Shaping the fabric
Dart manipulation refers to the techniques used for moving darts (the triangular folds that provide shaping to a flat pattern piece so it conforms to body curves) to different locations on the pattern. For example, a bust dart originating from the side seam can be relocated to the shoulder or waist.
The primary purpose of dart manipulation (sometimes called dart relocation) is to alter the style lines of the garment while maintaining the original fit around key body contours, such as the bust apex (the fullest point). This allows for diverse design possibilities stemming from the same basic block.
5.3 Adding seam allowance & hem: Ready for construction
Once the basic pattern shape and style lines are finalized, seam allowance must be added to the edges of each pattern piece. This allowance provides the necessary fabric width for joining pieces together during sewing and executing the appropriate seam finish.
Similarly, hem allowance is added to the bottom edges of garments or sleeves for clean finishing. While standard widths for seam allowance (e.g., 1/2 inch or 5/8 inch) and hems exist, the key is maintaining consistency within a single project for accurate construction. These construction details are vital for assembling the garment correctly.
5.4 Trueing seams & adding notches: Ensuring accuracy
Trueing seams is the essential step of checking that the lengths of adjacent pattern seams, which will be sewn together, match precisely. Any discrepancies are adjusted to ensure smooth sewing and prevent puckering or unevenness. Notches are small marks added perpendicular to the cutting line on pattern pieces.
These assembly marks serve as critical points of alignment during construction, helping the sewer match corresponding pieces correctly (e.g., matching points along a sleeve cap and armhole). Both trueing seams and adding notches are fundamental for pattern accuracy and achieving a professional finish, contributing significantly to overall garment accuracy.
6. Resources to kickstart your learning
6.1 Essential pattern making books
Investing in reputable pattern making books provides foundational knowledge and serves as ongoing resources. These often function as comprehensive textbooks or reference guides. Consider exploring titles from established authors:
- Helen Joseph Armstrong’s Patternmaking for Fashion Design: Widely regarded as a standard text, particularly comprehensive for flat pattern drafting techniques, covering everything from basic slopers to complex design manipulations.
- Books by Connie Crawford: Known for a clear, systematic approach often favoured in educational settings, providing detailed instructions for creating base patterns and adapting them.
These books delve deep into the principles and offer detailed diagrams and instructions crucial for understanding the mechanics of pattern development.
6.2 Structured online courses & workshops
For those who prefer guided learning, numerous online courses and workshops offer structured paths into pattern making. Platforms like Craftsy and Skillshare host a variety of classes taught by experienced professionals.
Additionally, many specialized fashion schools and independent designers offer dedicated online learning modules. When choosing, look for courses specifically focusing on foundational skills like accurate measuring, sloper creation, basic fitting adjustments, and introductory pattern drafting tutorial content. A structured course can provide valuable step-by-step guidance and visual demonstrations.
6.3 Local classes & mentorship
Exploring local classes can offer benefits that self-study or online learning might not fully provide. Check community colleges, adult education centers, local sewing studios, or fashion incubators in your area. The primary advantage here is the potential for direct, hands-on feedback from an instructor who can observe your technique and offer personalized guidance.
Finding mentorship through these channels or local industry connections can also significantly accelerate the learning process.
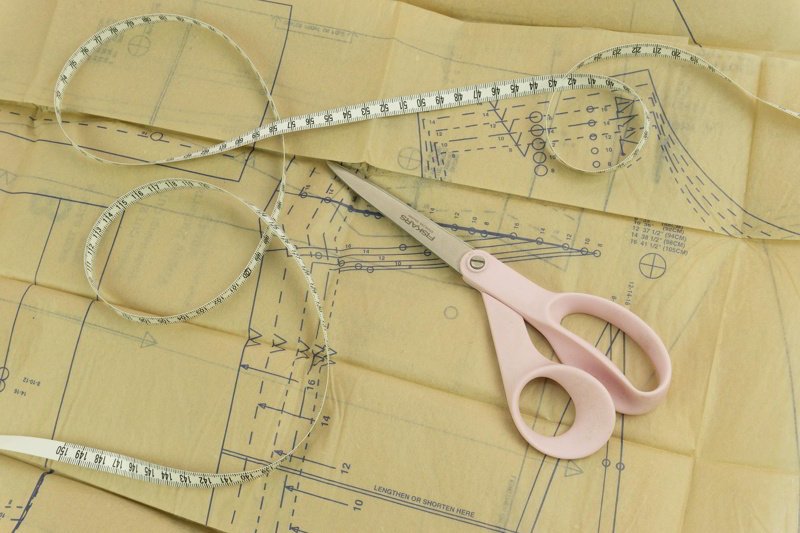
7. Scaling up: Digital tools and pattern grading for your brand
7.1 Introduction to digital pattern making software
As your business grows, transitioning to digital pattern making can offer significant advantages. Using software streamlines the digital workflow, making it easier to store, modify, and share patterns electronically. Digital files are less prone to physical damage and simpler to back up. Editing patterns digitally is often faster and more precise than manual adjustments. Furthermore, many digital tools facilitate pattern grading (creating multiple sizes).
For simpler needs or those already proficient in graphic design, vector programs like Adobe Illustrator can be adapted for pattern drafting, especially when combined with specialized plug-ins. However, dedicated fashion CAD (Computer-Aided Design) software offers more specialized tools and features tailored specifically for apparel development.
High-end options like CLO3D even allow for 3D virtual prototyping. It is crucial to understand, however, that proficiency with the software does not replace a solid understanding of fundamental pattern drafting techniques. The software is a powerful tool, but the knowledge of how garments fit and are constructed remains essential.
7.2 Understanding pattern grading: Sizing your designs
Pattern grading is the process of systematically increasing or decreasing the size of a base pattern to create a range of sizes (e.g., small, medium, large, XL) while maintaining the original shape, fit characteristics, and style proportions. This step is absolutely critical for selling apparel to a diverse customer base. Without accurate grading, garments will not fit consistently across the offered size range.
Grading can be done manually using specific measurement charts and grade rules, which requires precision and practice. Increasingly, digital pattern making software is used for grading, offering potentially faster and more automated methods, though still requiring skilled input to ensure accuracy.
Regardless of the method (whether manual or digital), achieving accurate pattern grading is vital for maintaining fit consistency and minimizing returns, ultimately impacting customer satisfaction and brand reputation. The resulting production patterns must reflect the intended size chart accurately.
8. Alternatives & strategic choices for your business
8.1 Modifying existing commercial patterns
One alternative approach, especially when starting, is to use commercially available sewing patterns as a base and make pattern alteration modifications.
- Pros: Can be a faster way to produce initial samples compared to drafting from scratch; may seem cheaper upfront per pattern.
- Cons: Severely limits design originality as you’re working within an existing framework; standard commercial pattern fit often requires significant alteration anyway; most importantly, there are critical ethical and legal limitations regarding the use of commercial patterns for garments intended for resale. Check the pattern’s usage rights carefully – most prohibit commercial use. This makes it problematic for building a unique, scalable brand.
While useful for learning construction or personal projects, relying heavily on modifying commercial patterns for a business is generally not a sustainable strategy for establishing a distinct brand identity.
8.2 Hiring a professional pattern maker
Engaging a professional pattern maker is a common and often necessary step for growing brands.
- Pros: Immediate access to specialized expertise and experience; saves significant time, allowing you to focus on other business areas; ideal for complex designs or when high precision is paramount from the start.
- Cons: Represents a higher upfront cost per pattern; requires excellent communication – clear technical sketches (tech packs) detailing measurements, construction, and materials are essential; finding the right pattern maker who understands your aesthetic and target fit takes effort.
When considering hiring, factor the pattern maker’s fees into your garment costing and development budget. This is a professional service requiring clear briefs and collaborative feedback.
8.3 Utilizing made-to-measure pattern services
A newer option involves using online pattern services that generate custom patterns based on specific measurements you input. Services allow users to enter body measurements or adjust standard blocks, and the service generates a downloadable digital pattern.
- Pros: Can provide a personalized fit relatively quickly; potentially faster than learning drafting from scratch; may be less expensive per pattern than hiring a dedicated professional for simpler items.
- Cons: Design possibilities are often limited by the service’s pre-defined blocks and modification options; you have less direct control over the nuances of the pattern compared to DIY drafting; represents a recurring cost if used frequently for new styles (MTM patterns).
These made-to-measure patterns can be a viable middle ground, particularly for businesses focused on custom fit or needing patterns generated quickly based on specific dimensions.
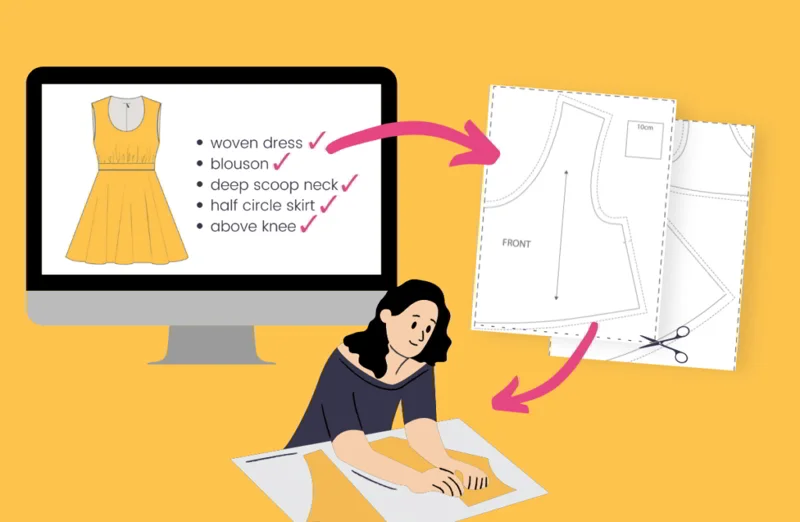
8.4 Making the right decision: Strategy for your brand
Choosing the right approach requires a careful strategic choice based on your unique business context. Weigh these factors:
- Budget: How much capital can you allocate to pattern development (tools, software, courses, hiring)?
- Time: How much time can you realistically dedicate to learning and practicing pattern making versus outsourcing?
- Design complexity: Are your designs relatively simple or highly intricate?
- Uniqueness: How critical is complete design originality to your brand identity?
- Production volume: Are you making one-offs, small batches, or planning larger production runs?
- Long-term goals: Do you envision pattern making as a core in-house skill, or is it something you prefer to outsource?
A phased approach might be suitable. You could start by modifying patterns (for learning only) or using pattern services for initial products, then invest in developing in-house skills or hiring a professional as your brand grows and requires more complex or unique designs. This decision making process is key to aligning your pattern strategy with your overall business objectives.
9. Related questions
9.1 How much does it cost to start making my own patterns?
The initial cost to acquire basic pattern making tools (rulers, curves, paper, etc.) can range roughly from $50 to $200+, depending on quality and where you source them. If pursuing draping or wanting a tool for fit assessment, a dress form represents a more significant investment, potentially costing several hundred dollars or more for a quality adjustable or professional form.
Books or online courses add to the expense. However, the most significant factor is the time investment required to learn and practice effectively. Compared to hiring a professional (which can cost several hundred dollars per pattern) or using pattern generation services (often charged per pattern), the direct financial outlay for DIY tools is lower, but the time commitment is substantial.
9.2 Can I make patterns from clothes I already own?
Yes, it is possible to make patterns from existing clothes. This process is often referred to as “rubbing off” or “cloning” a garment. It typically involves carefully tracing the seam lines and shapes of a deconstructed or carefully laid-out existing garment onto paper. This can be a useful exercise for understanding how garments are constructed.
However, achieving high accuracy can be challenging without deconstructing the original piece. Furthermore, it is crucial to be aware of copyright issues; directly cloning commercial designs for resale purposes is unethical and likely illegal. Using this method for personal learning is different from using it for commercial production.
9.3 What’s the difference between a sloper and a commercial pattern?
A sloper (or block) and a commercial pattern serve different purposes. A sloper is a basic template representing a specific set of body measurements with a close fit and no added ease (room for movement/comfort) or seam allowance. It’s the foundation from which designs are developed.
In contrast, a commercial pattern purchased in a store includes ease appropriate for the intended style, seam allowances for construction, and all the design details (like collars, pockets, closures) for a specific garment style. Commercial patterns are designed for standard size ranges and often require alterations for an individual fit, whereas a sloper is the starting point for creating a custom fit.
9.4 How do I ensure my patterns will fit different body types?
Ensuring a good fit across different body types within your target size range involves more than just drafting the initial pattern. Accurate pattern grading is the first essential step, using established grade rules or digital software to scale the pattern pieces correctly for each size. However, grading alone isn’t enough. Thorough testing is crucial.
This means creating sample garments or muslin mock-ups in key sizes (e.g., the smallest, middle, and largest sizes you plan to offer) and conducting fitting sessions on actual fit models who represent the variety of shapes within your target customer base. Gathering and incorporating feedback from these fitting sessions is vital for refining the patterns to achieve the best possible fit across the intended size range.
9.5 Do I need a dress form to start pattern making?
No, a dress form is not strictly required to start pattern making, particularly if you focus on the flat pattern drafting method, which relies primarily on measurements translated onto paper. However, a dress form is absolutely essential for the draping technique.
Even if you primarily use flat drafting, a dress form corresponding to your base size or target customer size can be extremely helpful for visualizing fit, checking the drape of the fabric, and making adjustments during the pattern development process. It provides a 3D representation that paper patterns alone cannot offer, making it a valuable, though not initially mandatory, tool for DIY pattern making, although starting without one is possible.
Read more:
Understanding the fundamentals of clothes pattern making is empowering for any clothing business. Whether you choose to develop the skill yourself, hire expert help, or utilize pattern services, engaging with the pattern creation process gives you crucial control.
This control extends to achieving consistent fit, maintaining high quality standards, and developing truly unique designs – all core components that build brand value and customer loyalty in the competitive fashion landscape. Creating custom clothing starts with a well-executed pattern.
Assess your business’s specific needs, resources, and long-term goals to determine the most strategic approach to pattern making. Explore the resources available, whether books, courses, or professional connections. Taking deliberate steps to manage your pattern development will significantly impact your brand’s success and ability to deliver exceptional products.
For further guidance on integrating pattern strategies into your production workflow or sourcing related supplies like custom labels and tags that reflect your brand’s quality, consulting with experts familiar with the complete apparel journey can provide valuable insights.