Many apparel businesses start with standard rectangular labels and hang tags – they’re functional, familiar, and often the default option. However, relying solely on basic shapes might mean missing a significant opportunity to make your brand truly stand out.
Imagine clothing racks filled with similar items; a uniquely shaped tag or label can instantly capture attention and differentiate your products. This is where die cutting comes into play. Die cutting is a manufacturing process that allows you to create custom shapes for your apparel branding elements like labels and tags.
Moving beyond simple rectangles opens up a world of creative possibilities. A distinctive shape can subtly communicate your brand’s personality, enhance perceived value, and make your items more memorable to consumers.
This article serves as a guide for apparel businesses looking to explore custom shapes. You’ll gain a clear understanding of what die cutting involves, the different methods available, and how leveraging unique shapes can significantly boost your brand identity. We’ll explore how this fabrication method works and why it’s a valuable tool for any clothing line aiming for distinction!
1. Decoding Die Cutting: A Simple Explanation
1.1 What Does “Die Cut” Actually Mean?
Think of die cutting as using an industrial-strength cookie cutter. At its core, this fabrication method uses a specialized tool called a die – essentially a custom-shaped metal die (often made of steel rules or machined metal) with sharp edges. This die (tooling) is pressed with significant pressure onto the material (often fed as a continuous roll or sheet, sometimes called a web).
The pressure causes the die’s sharp edges to shear through the material, precisely creating the desired custom shapes. This process is highly accurate and works effectively on various materials commonly used for apparel labels and tags, including paper stocks, cardboards, certain fabrics, and synthetic materials. The result is a clean, precisely die cut shape, identical every time.
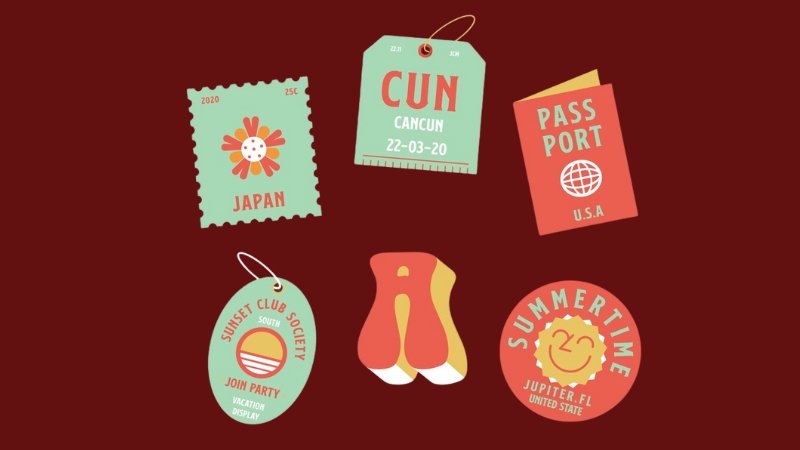
1.2 The Basic Process: How Custom Shapes Are Made
The fundamental die cutting process for creating shaped cutouts is straightforward:
- Material Positioning: The chosen material (paper, fabric, etc.) is placed correctly onto the cutting surface or fed into the machine.
- Die Application: The custom die is brought into contact with the material.
- Pressure & Cutting: Sufficient pressure is applied, forcing the die’s sharp edges through the material, following the precise outline specified by the die line (the digital line in the design file indicating where the cut should be).
- Waste Removal: The excess material surrounding the cut shape, known as the matrix, is removed, leaving behind the finished die-cut label or tag. Understanding the matrix removal is key, as overly intricate designs can sometimes make this step challenging.
2. Common Die Cutting Methods Relevant for Apparel Labels & Tags
2.1 Rotary Die Cutting: Speed and Efficiency for Larger Orders
For brands needing large quantities of labels or tags consistently, rotary die cutting is often the preferred manufacturing process. This method utilizes a cylindrical die mounted on a rotary press. The material, typically fed continuously from a roll (web-fed), passes between the rotating die cylinder and a smooth anvil cylinder.
As the die rotates, it cuts the shapes quickly and precisely. The primary advantage of using a Rotary die cutter is its speed, enabling high throughput and ensuring excellent consistency across extensive runs. This makes it highly efficient for large-scale label production where uniformity and speed are paramount.
2.2 Flatbed Die Cutting: Versatility for Unique Materials or Smaller Runs
In contrast to the continuous motion of rotary cutting, flatbed die cutting involves a different mechanism. Here, a flat die (shaped like a cookie cutter) is pressed vertically onto the material, which is usually positioned in sheets or placed stationary on a flat surface (the “bed”). A Flatbed die cutter applies pressure from above, punching out the shape.
This method offers greater versatility, particularly excelling with thick materials or more rigid substrates often used for premium hang tags. While generally slower than rotary cutting, flatbed die cutting can be more cost-effective for lower volume runs or projects involving unique materials, as the initial tooling cost for a flat die can sometimes be less complex than for a rotary die.
2.3 Kiss Cutting: The Secret Behind Custom Stickers & Easy-Peel Labels
Kiss cutting is a specialized die cutting technique crucial for producing adhesive labels and stickers commonly used in apparel – think size strips, logo stickers, or branding seals. Unlike standard die cutting that cuts through all layers, a Kiss cut die is precisely calibrated to cut only through the top layer of the material (the face stock) while leaving the backing liner completely intact.
This precision allows the sticker or label shape to be easily peeled away from the backing sheet. It’s the technique that makes peeling individual stickers from a sheet effortless, essential for efficient application in label production and packaging processes.
3. Why Choose Die Cut Labels and Tags for Your Clothing Line?
3.1 Stand Out on the Rack: Unique Brand Identity with Custom Shapes
In a crowded marketplace, standard rectangular labels and tags can easily blend in. Utilizing custom shapes achieved through die cutting offers a powerful way to achieve visual differentiation. A unique silhouette instantly draws the eye, making your product more noticeable amidst competitors. Think beyond the basic square:
- A tag shaped like your brand’s logo reinforces brand identity immediately.
- A shape reflecting the garment’s theme (e.g., a leaf shape for organic cotton items, a surfboard shape for beachwear) creates a stronger connection.
- Unexpected geometric or abstract forms can pique curiosity.
These custom shapes, whether created using intricate thin metal dies for precision or robust steel-rule dies for standard materials, transform a simple label or tag into a memorable element. This physical distinction aids brand recall and elevates the perception of your apparel. Effective label design leverages shape as much as color and typography for maximum impact through customization.
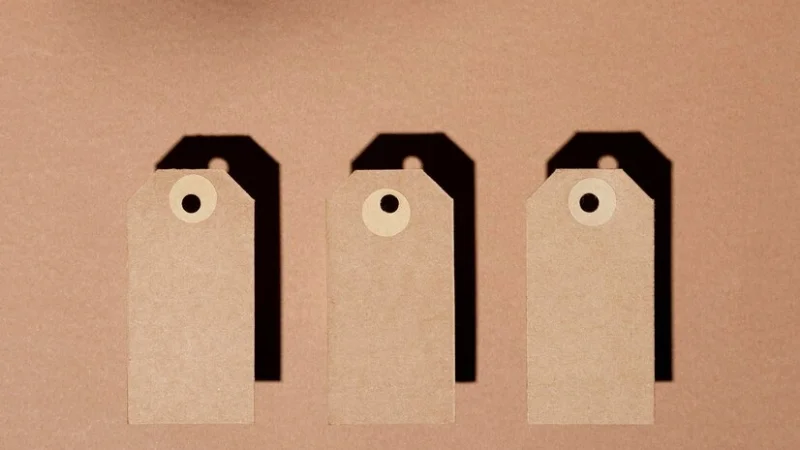
3.2 Reinforce Your Brand Style & Story
The shape of your label or tag is more than just an outline; using specific shape language is a subtle yet effective way to communicate your brand aesthetic. Sharp, angular cuts might convey an edgy, modern feel, while soft, curved, or organic shapes could suggest natural materials, comfort, or approachability.
A luxury brand might opt for a classic, elegant die-cut shape, reinforcing sophistication. The physical form of the tag becomes an extension of your brand style, contributing to the overall narrative you’re telling customers about your clothing line and what makes your brand unique. Choosing a shape that aligns with your brand’s personality ensures cohesive messaging.
3.3 Functional Design Possibilities
Die cutting isn’t solely about aesthetics; precision cutting enables clever functional design elements within your labels and tags. Consider these practical applications:
- Unique Hang Tag Holes: Instead of a standard punched hole, create a custom-shaped opening designed to work perfectly with specific types of ribbons, cords, or safety pins, adding a touch of bespoke detail.
- Integrated Folds or Scores: Die cutting can incorporate score lines, allowing hang tags to fold neatly into multi-panel mini-booklets, providing extra space for brand stories, care instructions, or social media details without increasing the overall tag footprint significantly.
- Purposeful Shaping: Design tags shaped to tuck neatly into a specific pocket, follow the contour of a neckline, or wrap smoothly around a button, enhancing the user experience and integrating the tag more seamlessly with the garment.
4. Designing and Ordering Die Cut Items: Expert Tips for Apparel Businesses
4.1 Material Matters: Choosing the Right Stock for Labels & Tags
Selecting the appropriate material is a foundational step that should happen before finalizing your die-cut design. The choice significantly impacts the final look, feel, and performance of your labels and tags, as well as the feasibility of the die cutting process itself. For apparel, key factors determining material suitability include:
- Durability & Washability: How will the label or tag hold up to wear, washing (for sew-in labels), and general handling? Materials range from sturdy cardstocks for hang tags to durable synthetics (a high-density polyethylene fiber material known for strength and water resistance) or woven fabrics for sew-in applications.
- Texture & Feel: The material’s surface contributes heavily to brand perception. Does your brand call for a smooth, coated finish, a natural, textured paper, soft satin, or rustic cotton?
- Printability: Ensure the chosen stock readily accepts your desired printing method and yields crisp, clear results. Some textures or coatings can affect ink adhesion.
- Sustainability: Consider options like recycled paper, organic cotton, or biodegradable materials if environmental responsibility is part of your brand ethos.
- Die Cutting Behavior: Very thin or very brittle materials might be challenging to cut cleanly without tearing, especially with complex shapes. Thicker materials might necessitate flatbed cutting over rotary.
Material | Typical Use | Durability | Feel/Texture | Printability | Die Cut Suitability | Notes |
---|---|---|---|---|---|---|
Cardstock | Hang tags | Moderate | Varies (smooth, textured) | Excellent | Good to Excellent | Wide range of weights and finishes. |
Coated Paper | Hang tags | Moderate | Smooth | Excellent | Excellent | Good for vibrant graphics. |
Recycled Paper | Hang tags | Moderate | Often textured | Good | Good | Eco-friendly option. |
Tyvek® | Sew-in, Hang tags | High | Smooth, papery | Good | Good | Water/tear-resistant. |
Woven Polyester | Sew-in labels | High | Soft, flexible | N/A (Woven) | Good | Durable for washing. |
Woven Cotton | Sew-in labels | Moderate-High | Soft, natural | N/A (Woven) | Good | Natural feel, softer than poly. |
Satin | Sew-in labels | Moderate | Smooth, shiny | Good (Printed) | Fair to Good | Prone to fraying if edge isn’t sealed. |
Leather/Faux | Patches, Hang tags | High | Varies | Fair (Emboss/Deboss best) | Fair to Good | Requires specific die/pressure. |
4.2 Design Considerations for Clean Cuts & Professional Results
Creating a design that translates well to die cutting requires attention to certain technical details. Following these design tips ensures cleaner cuts, easier matrix removal (peeling away the waste material), and more professional results:
- Avoid Extremely Sharp Internal Corners: Very acute angles (less than 30-45 degrees) inside a shape can be weak points where the material might tear during cutting or when the surrounding matrix is pulled away. Opt for slightly rounded internal corners where possible.
- Maintain Adequate Spacing: Elements that are too close together or extremely thin strips (generally less than 1mm-1.5mm, depending on material) risk tearing or being unstable after cutting. Ensure sufficient material remains between cut lines and around edges.
- Incorporate Bleed: If your design has color or graphics extending to the cut edge, you must include bleed in your artwork preparation. Bleed is extra image area (typically 1.5mm to 3mm) extending beyond the intended cut line (die line). This ensures that even if there’s minuscule shifting during the cutting process, you won’t have unprinted white edges showing on the final piece.
- Provide a Clear Die Line: Your artwork file must include a distinct, separate vector line (often designated in a specific spot color like magenta) indicating precisely where the die should cut. This die line should be separate from your printable artwork layers. Ambiguous or unclear die lines lead to errors.
- Consider Material Grain: For some paper stocks, cutting intricate shapes against the grain might increase the risk of tearing. While often managed by the provider, complex designs might benefit from discussing orientation.
4.3 Partnering with Your Label & Tag Provider
Effective communication with your chosen label provider or tag provider is crucial for successful die-cut projects. Clearly articulate your vision, intended use, material preferences, and quantity needs. Understand that creating a custom shape requires manufacturing a unique die, which involves initial tooling costs. These costs are separate from the per-piece price and vary based on complexity and die type (rotary vs. flatbed).
Alternatively, inquire if the provider has existing standard dies (like circles, ovals, or common burst shapes) that might meet your needs without incurring custom tooling fees. Always insist on reviewing a digital proof, and if possible for larger orders or complex designs, a physical prototype or sample before committing to mass production.
Treat the proofing stage seriously – this is your final check to ensure the shape, size, material, and printing align perfectly with your expectations. A good supplier relationship is collaborative, ensuring the final product matches your branding goals.
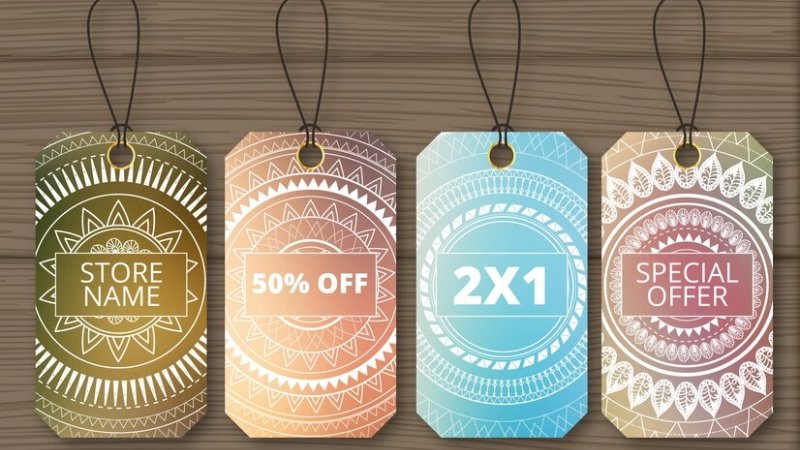
5. Related Questions
5.1 Is die cutting expensive for custom shapes?
The primary die cutting cost associated with custom shapes is the initial investment in creating the custom die (the metal tool). This tooling cost is a one-time expense per design. Once the die is made, the per-piece cost for die cutting is generally quite low, especially for larger production runs where the tooling cost is amortized over many items.
Using a provider’s existing standard shape die avoids this initial tooling cost entirely. Therefore, while there’s an upfront investment for unique shapes, the process becomes very cost-effective at volume.
5.2 What’s the difference between die cut and kiss cut labels?
The main difference lies in the cutting depth. A standard die cut cuts completely through both the label material (face stock) and its backing liner, resulting in individual, separate pieces shaped exactly like the die. In contrast, a kiss cut only cuts through the top layer (the face stock) of the labels, leaving the backing liner intact. This creates stickers or labels that can be easily peeled off a larger sheet or roll, as the liner holds them together until peeled.
5.3 Can any shape truly be die cut?
While die cutting is very versatile, there are practical limitations. Extremely intricate designs with very fine details, sharp internal corners, or exceptionally thin elements (less than 1-1.5mm) can be challenging. These features may risk tearing the material during the cutting or matrix removal process (stripping away the waste).
While technology allows for complex shapes, overly complicated designs might require adjustments for optimal production results or may be better suited for alternative methods like laser cutting.
Die cutting uses a physical metal die and pressure to shear through material. Laser cutting uses a high-powered, focused laser beam to burn or vaporize the material along a programmed path. For labels and tags:
- Die Cutting: Generally faster and more cost-effective for high volumes once the custom die is made. Edge quality can be very clean depending on the material and die sharpness. Less suited for extremely intricate designs compared to lasers.
- Laser Cutting: Ideal for highly intricate designs or prototypes as no physical die is needed (lower setup cost for unique shapes in small quantities). Can handle complex patterns die cutting cannot. However, it’s typically slower per piece, potentially less cost-effective for mass production, and can sometimes leave slightly discolored or burnt edges on certain materials (like paper or fabric).
Read more:
Ultimately, die cutting offers apparel businesses a powerful avenue for customization, moving beyond standard formats to create truly distinctive labels and tags. Embracing custom shapes is more than an aesthetic choice; it’s a strategic tool for enhancing brand identity and achieving standout visual identity in a competitive market.
This versatile cutting technique allows for unique expressions of your brand’s personality directly on your products, making them more memorable and engaging for consumers. Considering how shape can complement your logo, colors, and materials is an integral part of building a cohesive brand presence.
Exploring the possibilities of die-cut designs can significantly contribute to how your brand is perceived and remembered. For specific projects or to better understand material and design constraints, consulting with label and tag specialists can provide tailored guidance.