For apparel business owners and designers, navigating the world of manufacturing involves countless details. Getting the seams and stitches right is fundamental, yet often overlooked until problems arise. Poor stitch choices can compromise garment quality, leading to customer returns and negatively impacting your brand’s reputation.
Misunderstandings about stitch specifications between your team and the factory can also cause costly delays and rework. This guide cuts through the complexity. By understanding the key industrial sewing stitches, their characteristics, and best uses, you gain control over crucial aspects of production.
You’ll learn how different stitches affect garment durability, appearance, seam strength, and even production cost. Let’s explore these essential stitches.
1. Why understanding sewing stitches is non-negotiable for your brand
The type of stitch used in your garments directly influences their perceived value and longevity. A seam that puckers, breaks easily, or doesn’t stretch appropriately signals poor quality to the customer, potentially leading to dissatisfaction and returns. Selecting the appropriate stitch ensures the garment performs as intended, enhancing durability and customer satisfaction.
Beyond quality, stitch selection has tangible impacts on production efficiency and cost. Some stitches, like the chainstitch, sew faster than others, potentially reducing labor costs. However, these faster stitches might consume more thread or lack the strength of alternatives like the lockstitch.
Understanding these trade-offs allows for strategic decisions balancing speed, cost, and required performance. Clear tech pack specifications detailing the exact stitch types, stitch length, and thread prevent manufacturing mistakes.
Ambiguity can lead to factories using incorrect stitches, resulting in garments that don’t meet quality standards or functional requirements, necessitating expensive rework or rejected orders in apparel manufacturing.
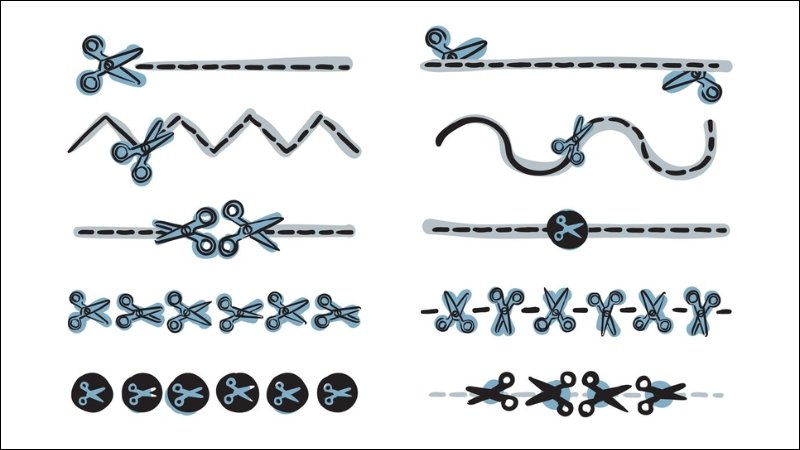
2. Decoding the stitch: basic principles of stitch formation
At its core, machine sewing involves a needle carrying a thread through layers of fabric. How this needle thread interacts with other threads below the fabric determines the stitch type. Two primary mechanisms create most industrial stitches: interlocking and interlooping.
Interlocking typically involves a needle thread passing through the fabric and looping around another thread supplied by a bobbin (a small spool held under the needle plate). This creates a secure ‘lock’ within the fabric layers, characteristic of the lockstitch (Class 300). Think of the two threads knotting together.
Interlooping, used in chainstitches, overlock stitches, and coverstitches (Classes 100, 400, 500, 600), involves the needle thread passing through the fabric and forming a loop on the underside. This loop is then caught and interconnected with loops from subsequent stitches formed by the needle thread itself or by additional threads supplied by loopers (thread-carrying mechanisms distinct from bobbins).
This creates a chain-like structure, often offering more stretch than interlocking stitches.
3. The workhorses: must-know industrial stitch types (ASTM stitch classifications)
To standardize communication and ensure consistency in manufacturing, industrial sewing stitches are categorized into classes based on their formation method. The most widely recognized system is the ASTM International standard (ASTM D6193). Familiarity with these classifications is helpful when communicating with factories. The main classes used in apparel are:
- Stitch Class 100: single thread chainstitches
- Stitch Class 300: lockstitches (formed with needle and bobbin thread)
- Stitch Class 400: multi-thread chainstitches (formed with needle and looper threads)
- Stitch Class 500: overedge chainstitches (stitches formed over a fabric edge)
- Stitch Class 600: covering chainstitches (stitches covering top and bottom surfaces)
Understanding these broad categories helps navigate the specific stitch types commonly employed within them.
3.1 Class 300: the lockstitch (Type 301) – the standard for strength and stability
The Type 301 lockstitch is arguably the most common stitch in apparel manufacturing.
Appearance: forms identical, straight stitches on both the top and bottom surfaces of the fabric (reversible appearance).
Characteristics:
- Very strong and secure seam.
- Minimal stretch or low elasticity, making it stable.
- Relatively flat and low bulk.
- Requires a bobbin thread underneath, which slightly interrupts continuous production and can reduce overall speed compared to bobbin-less stitches.
- Can sometimes contribute to seam pucker (a wrinkled appearance along the seamline) on certain fabrics if tension isn’t optimal.
Ideal uses:
- Seaming woven fabrics (like shirts, trousers, jackets) where stability is desired.
- Attaching collars, cuffs, plackets, and pockets.
- Decorative topstitching for a clean, classic look.
- Areas requiring high seam strength without needing stretch.
The lockstitch’s strength and clean finish make it indispensable, particularly for garments made from stable woven materials.
3.2 Class 400: the chainstitch (Type 401) – built for speed and stretch
The Type 401 chainstitch offers distinct advantages in speed and flexibility compared to the lockstitch.
Appearance: looks like a straight lockstitch on the top side, but forms a distinct looped chain pattern on the underside.
Characteristics:
- Offers good seam elasticity, suitable for seams requiring some give.
- High production speed due to continuous stitching without bobbin changes.
- Consumes more thread than a lockstitch.
- It has a significant drawback known as ‘runback’: if the thread breaks or the end isn’t secured properly, the entire seam can easily unravel from the finishing end.
Ideal uses:
- Seaming areas requiring moderate stretch, especially on heavier knits or wovens where stretch is a factor (e.g., waistband attachment before covering).
- Temporary stitching (basting) during garment assembly.
- Some decorative stitching effects.
To mitigate the runback issue, chainstitch ends must be secured, often by stitching over them with another stitch type (like a lockstitch bartack) or incorporating them into another seam.
3.3 Class 500: overedge/overlock stitches – the knitwear essential for seaming and finishing
Overedge stitches, commonly called “overlock” or “serger” stitches, are fundamental for knitwear and edge finishing. They perform multiple functions simultaneously.
Appearance: stitches loop around the edge of the fabric, encasing it. Often formed with multiple threads (2 to 5). Many overlock machines incorporate knives that trim the fabric edge simultaneously as the stitch is formed, creating a clean edge.
Characteristics:
- Excellent elasticity, moving with stretch fabrics without breaking.
- Neatly finishes fabric edges, preventing fraying on both knit and woven materials.
- Can simultaneously seam and finish edges.
- Can be relatively bulky depending on the thread count.
Ideal uses:
- Primary construction seams for most knit garments (t-shirts, sweatshirts, leggings).
- Finishing raw edges inside garments (woven or knit) to prevent fabric fraying.
- Attaching ribbing, collars, and cuffs on knits.
Common variations:
- Type 503: a 2-thread overedge stitch, often used for light edge finishing (serging) or hemming on t-shirts before coverstitching. Not typically strong enough for major seams.
- Type 504: a 3-thread overedge stitch, the workhorse for seaming knits and general edge finishing. Offers a good balance of stretch and coverage.
Overlock stitches are indispensable for handling the stretch and fraying tendencies of knit fabrics and providing clean internal finishes.
3.4 Class 400/600: coverstitches (Types 406, 602, 605) – the professional hem for stretch fabrics
Coverstitches provide flat, stretchy, professional-looking finishes, especially common for hemming knits and in sportswear.
Appearance: characterized by two or three parallel rows of straight stitching on the top surface and a looper pattern (similar to an overlock or chainstitch) covering the raw edge on the underside. Class 600 stitches include an additional ‘top cover’ thread (also called a spreader thread) that creates a decorative, interwoven pattern on the top surface, mirroring the looper pattern underneath.
Characteristics:
- Excellent seam elasticity, ideal for stretch fabrics.
- Creates a very flat seam appearance, reducing bulk.
- Provides good coverage of raw edges on the inside (and outside for Class 600).
- Can be decorative.
- Consumes a significant amount of thread.
Ideal uses:
- Hemming sleeves and bottoms of t-shirts, sweatshirts, and other knit garments.
- Attaching bindings and elastic.
- Creating flat, strong seams on activewear and sportswear.
- Decorative topstitching effects.
Common variations:
- Type 406: a common 2-needle coverstitch (Class 400), using two needle threads and one looper thread. Straight stitches on top, looper coverage underneath.
- Type 602: similar to 406 but adds a top cover thread/spreader (Class 600), creating looper coverage on both top and bottom. Uses 2 needle threads, 1 looper, 1 top cover thread.
- Type 605: a 3-needle coverstitch with a top cover thread (Class 600). Uses 3 needle threads, 1 looper, 1 top cover thread. Offers wider coverage and more stretch. Type 605 is often referred to more broadly as a ‘covering chain stitch’.
Coverstitches are key to achieving the durable, stretchy, and clean finishes expected in commercial knitwear and performance apparel.
4. Expanding your stitch vocabulary: other useful types in apparel
While the previous stitches form the backbone of garment construction, several others serve specific functional or decorative purposes.
4.1 Zigzag stitch (Types 304, 404)
This stitch forms a side-to-side pattern rather than a straight line. Its primary advantage is accommodating stretch. Uses include:
- Creating stretch seams where elasticity is crucial (e.g., swimwear, lingerie).
- Attaching elastic directly to fabric.
- Creating decorative effects or appliqué (attaching fabric shapes).
- Reinforcing stress points through bartacking (a dense concentration of zigzag stitches). Zigzag stitches exist in both the lockstitch family (Type 304, using a bobbin) and the chainstitch family (Type 404, using a looper).
4.2 Blind stitch (Type 103)
The purpose of a blind stitch is to create hems where the stitching is nearly invisible from the outside of the garment. Typically achieved using a specialized machine with a curved needle, the stitch catches only one or two threads of the outer fabric layer within the hem allowance.
This technique (invisible hemming) is often used on tailored trousers, skirts, and higher-end garments for a clean finish. The most common industrial blind stitch is Type 103, a single-thread chainstitch, which shares the runback tendency of other Class 100 stitches if not secured.
4.3 Safety stitches (Types 515, 516)
Safety stitches are combination stitches, typically involving a row of chainstitch running parallel to an overedge stitch, formed simultaneously on one machine.
- Type 515: combines a 401 chainstitch with a 503 2-thread overedge stitch.
- Type 516 (often called “5-thread safety stitch”): combines a 401 chainstitch with a 504 3-thread overedge stitch. The purpose is to provide enhanced seam security and strength. The chainstitch provides the primary load-bearing seam strength, while the overedge stitch finishes the edge and adds reinforcement. These are commonly used on durable garments subjected to high stress, such as jeans (inseams, side seams), workwear, and outerwear.
5. Choosing wisely: a practical framework for stitch selection
Selecting the appropriate stitch involves considering multiple factors related to the fabric, garment end-use, desired look, and production realities. A systematic approach helps ensure the best choice for each application.
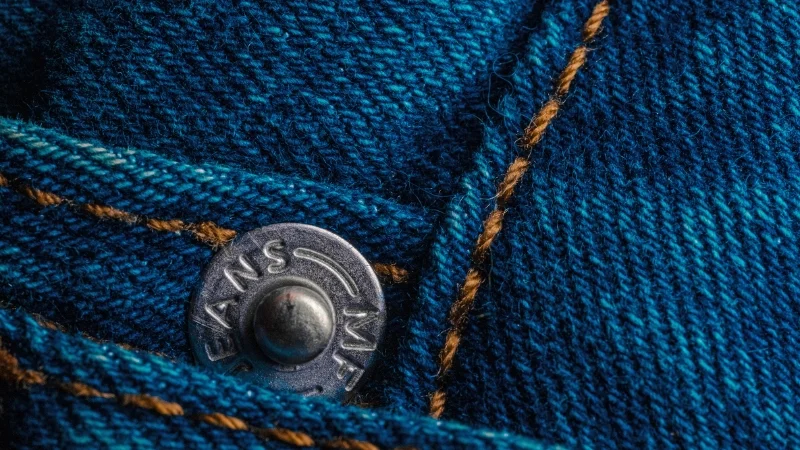
5.1 Factor 1: fabric type is paramount (knit vs. woven)
This is the most critical factor. Fabric properties dictate stitch requirements:
- Woven fabrics: generally stable with minimal stretch. They pair well with stable stitches like the lockstitch (301) for primary construction seams due to its strength and low elasticity. Overlock stitches (e.g., 504) are often used for edge finishing to prevent fraying.
- Knit fabrics: characterized by inherent stretch. Stitches used on knits must be able to stretch with the fabric to prevent seams from popping under stress. This necessitates stitches with good elasticity, such as overlock stitches (503, 504, safety stitches) for seaming and edge finishing, and coverstitches (406, 602, 605) or zigzag stitches (304, 404) for hemming and areas requiring high stretch. Using a standard lockstitch for a main seam on a very stretchy knit garment (like swimwear or leggings) is generally unsuitable and will likely lead to broken stitches during wear.
5.2 Factor 2: garment application and expected stress
Consider how and where the garment will be worn and the stress placed on specific seams:
- High-stress areas: seams in areas like crotches, armholes, and shoulders typically endure more strain. Stronger constructions might be necessary, potentially using a lockstitch (301) on wovens, or a safety stitch (515, 516) on knits or durable wovens like denim. Specific reinforcement like bartacking (using zigzag 304) might be needed at pocket corners or belt loop ends.
- Low-stress areas: seams like side seams on loose-fitting tops or decorative seams may not require maximum strength, allowing for choices based more on aesthetics or fabric type (e.g., a standard overlock 504 on knits).
- Required durability: workwear or activewear demands stitches that can withstand rigorous use and laundering, favouring robust options like lockstitches, safety stitches, or reinforced chainstitches. Formalwear might prioritize appearance and use finer stitches like blind hems.
5.3 Factor 3: desired aesthetics and functional finish
The final look and feel of the garment heavily influence stitch choice:
- Flat seams: if a flat seam profile is desired, especially on activewear or close-fitting garments, coverstitches (406, 600s) or specialized flatlock machines are preferred over potentially bulkier overlock seams.
- Edge finishing: preventing fraying is crucial for garment longevity and a clean interior appearance. Overlock stitches (500 class) are the standard for neatening raw edges. Alternatives include binding or facing, which involve different construction methods.
- Decorative topstitching: when stitching is meant to be visible as a design element, the choice depends on the desired look. Lockstitch (301) provides a classic, clean topstitch. Chainstitch (401) can offer a different texture. Coverstitches (406, 600s) provide parallel lines often seen on sportswear. Zigzag stitches can also be used decoratively.
- Seam types and finishes: the overall construction method (e.g., plain seam, felled seam, french seam) will also dictate appropriate stitch types.
5.4 Factor 4: balancing quality with production efficiency and cost
Practical manufacturing considerations play a role:
- Production efficiency: stitches that don’t require bobbin changes, like chainstitch (401), overlock (500s), and coverstitch (400s/600s), generally allow for faster sewing machine operations compared to lockstitch (301). This can impact labor costs per garment.
- Thread usage: stitches involving multiple loopers, such as overlock and coverstitch, consume significantly more thread per inch or centimeter of seam compared to lockstitch or basic chainstitch. This difference in thread consumption affects the overall material cost.
- Economic considerations: sometimes, a slight compromise on the ‘ideal’ stitch choice might be necessary to meet cost targets or production timelines, provided the chosen alternative still meets essential quality and durability standards for the specific application. Understanding the properties of different stitches allows for informed decisions in this balancing act.
6. Talking the talk: effectively specifying stitches for manufacturing
Clear communication about stitch requirements is essential for successful apparel manufacturing. Vague specifications are a common source of errors, delays, and cost overruns. Providing precise details in your tech pack ensures the factory understands exactly what is needed for each seam and finish.
Key information for a stitch callout includes:
- Stitch type: use the standard ASTM stitch type number whenever possible (e.g., 301, 401, 504, 406). This is the clearest language for manufacturers.
- SPI (stitches per inch) / stitch length: specify the desired stitch density. SPI indicates how many stitches are sewn within one inch. Stitch length is the length of a single stitch. These are inversely related (higher SPI means shorter stitch length). This impacts seam strength, elasticity, and appearance. Typical ranges vary by fabric and application (e.g., 8-12 SPI for many seams).
- Needle information: sometimes critical, specify needle size (e.g., 70/10, 90/14) and type (e.g., ballpoint for knits, sharp for wovens), especially for delicate or challenging fabrics. Also note if single-needle, twin-needle, etc.
- Thread information: specify thread type (e.g., polyester core-spun, textured poly), size/ticket number (e.g., Tex 27, Tkt 120), and color (reference Pantone or thread color code).
If you are unsure of the official stitch type number, include clear photos or diagrams in your tech pack specification. Sending a physical sample garment demonstrating the desired stitch is also highly effective. Don’t hesitate to leverage your factory’s expertise.
Discussing your fabric and garment design with them and asking for their recommendations can lead to optimal stitch choices. Proactive and clear factory communication is key to avoiding manufacturing mistakes.
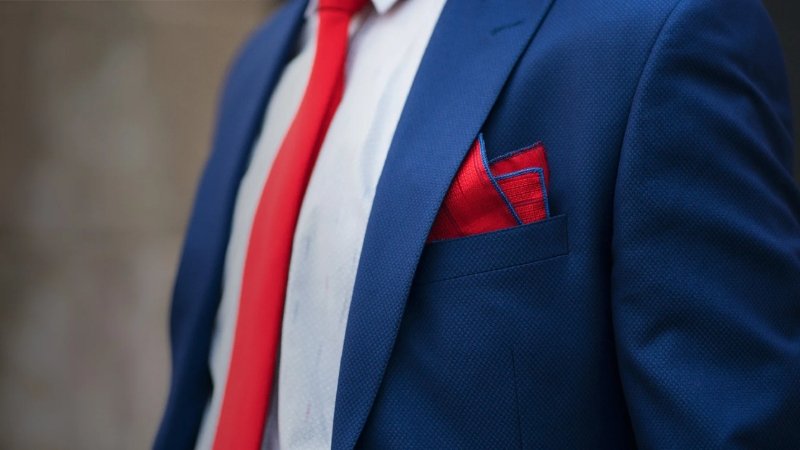
7. Related questions
7.1 What’s the difference between SPI and stitch length?
SPI stands for stitches per inch, measuring the number of stitches within a one-inch length of seam. Stitch length refers to the length of one individual stitch, usually measured in millimeters. They are inversely related: a higher SPI means more stitches are packed into an inch, so each individual stitch must be shorter.
Conversely, a lower SPI means fewer stitches per inch, resulting in a longer stitch length. Adjusting SPI/stitch length affects seam strength (higher SPI generally stronger), elasticity (lower SPI/longer stitches can allow more stretch within the seam line before thread breaks), and production speed (lower SPI is faster).
7.2 Can I use a lockstitch (Type 301) on knit fabrics?
While technically possible, using a standard lockstitch for primary construction seams on most knit fabrics is generally not recommended. Knits stretch, but the lockstitch has very low elasticity. When the knit fabric stretches during wear, the inflexible lockstitch seam is likely to break or “pop.” Stitches designed for stretch, like overlock (Class 500), coverstitch (Class 400/600), or zigzag (Type 304), are much better choices for seaming knits.
Exceptions might include very stable knits with minimal stretch, or specific applications like attaching non-stretch components (e.g., zippers) where stability is needed, often combined with other finishing techniques.
7.3 How can I identify the stitch type used on an existing garment?
Identifying stitches involves close examination: look at the top and bottom appearance – are they the same (likely lockstitch 301) or different (chainstitch 401, coverstitch)? Is the edge encased by threads (overlock 500s)? Does it form parallel lines on top (coverstitch 400s/600s)? Check the seam’s stretch – does it stretch easily with the fabric (likely overlock, coverstitch, zigzag) or resist stretching (likely lockstitch)?
Compare the visual characteristics to reference photos or descriptions like those in this guide. If constructing a similar garment, providing your factory with clear photos, or ideally a physical sample of the garment showing the stitch you want to replicate, is often the most effective way to ensure accuracy, even if you don’t know the official type number.
7.4 Which stitch types use the most thread?
Generally, stitches that involve multiple loopers to cover edges or surfaces consume significantly more thread per unit length of seam compared to simpler stitches. Multi-thread overlock stitches (like Type 504, 516) and coverstitches (Types 406, 602, 605, 607) are high thread consumption stitches due to the complex path of the looper and cover threads.
A basic lockstitch (Type 301) uses the least thread (one needle thread, one bobbin thread). A basic chainstitch (Type 401) uses more than a lockstitch but less than multi-thread overlock or coverstitches. Thread consumption is a factor in overall garment cost.
Read more:
Understanding and correctly specifying sewing stitches is not just a technical detail; it’s a fundamental aspect of creating high-quality apparel, managing production costs effectively, and building a reputable brand. The right stitch enhances durability, ensures comfort, provides the desired aesthetic, and contributes to efficient manufacturing.
By familiarizing yourself with the common industrial stitch types, their strengths, weaknesses, and appropriate applications – from the sturdy lockstitch to the stretchy overlock and coverstitch – you are better equipped to make informed decisions during design and development.
Communicating these choices clearly to your manufacturer via detailed tech packs is crucial for achieving consistent quality control and avoiding costly errors. Investing time in understanding stitches translates directly into better products and smoother production processes.
Beyond stitches, ensuring other elements like labels, tags, and packaging align with your brand quality is also key. For expert guidance on these complementary solutions tailored to your apparel business needs, consider exploring resources from Packlove.