Have you ever produced a batch of shirts, only to have customers complain about inconsistent fit? Or perhaps a well-sewn garment starts twisting strangely after its first wash? Often, the unseen culprit is the fabric grain. Understanding this fundamental aspect of textile structure is crucial for any business involved in clothing production. This article serves as a guide for small clothing businesses, explaining what fabric grain is, why mastering its principles is vital for garment quality and fit, and how to leverage this knowledge for better, more consistent results, ultimately reducing waste and enhancing customer satisfaction. By the end, you’ll have a clearer understanding of how to work with your fabric, not against it.
1. What is fabric grain?
1.1 The weave fundamentals
Warp threads
Imagine fabric on a loom or bolt. The threads running the entire length, parallel to the finished edges (the selvage), are the warp threads. During the weaving process, these threads are held under tension, making them typically stronger and resulting in less stretch. This direction defines the lengthwise grain of the fabric, providing inherent strength and stability.
Weft threads
Running across the width of the fabric, from one selvage to the other, are the weft threads. These threads are woven over and under the warp threads. Generally, weft threads have more give or stretch compared to the tighter warp threads. This direction constitutes the crosswise grain.
The selvage
The selvage refers to the tightly woven, often differently finished edge running along both lengths of a woven fabric. Produced during weaving to prevent unraveling, the selvage serves as the primary visual indicator for identifying the straight grain or fabric direction. Unlike cut edges, the selvage does not fray easily.
1.2 Decoding the three grainlines: Straight, cross, and bias
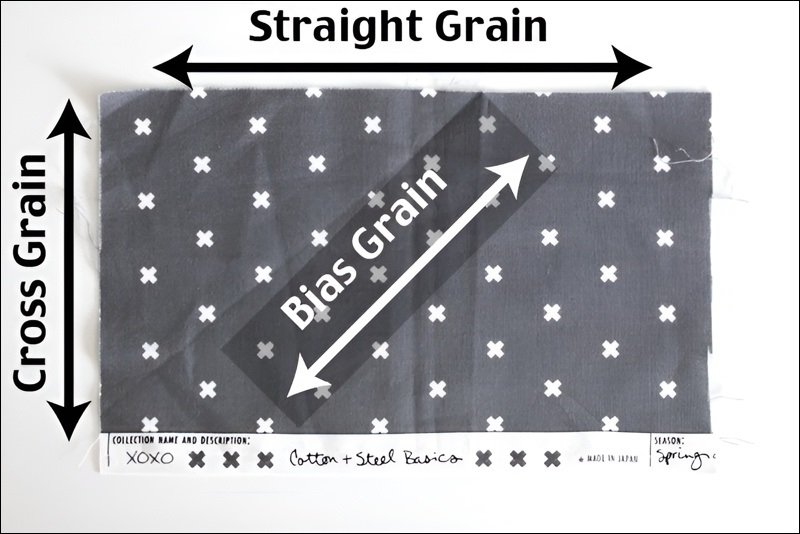
Straight grain
Also known as the lengthwise grain, the straight grain runs parallel to the selvage and the warp threads. This direction offers the greatest stability and strength with the least amount of stretch. Consequently, most main garment pieces are cut along the straight grain to maintain shape and structure.
Cross grain
The cross grain runs perpendicular to the selvage and parallel to the weft threads. This direction exhibits more flexibility and a moderate degree of stretch compared to the straight grain. Utilizing the cross grain can be beneficial where some horizontal give is desirable for comfort or fit.
Bias grain
The bias grain refers to any diagonal direction across the fabric weave. The ‘true bias’ specifically denotes the 45-degree angle relative to the straight and cross grains. Fabric cut on the true bias exhibits maximum stretch, drape (how the fabric hangs), and fluidity. This unique property arises because the 45-degree angle allows the woven threads the greatest freedom of movement relative to each other. Understanding the bias is key for specific design effects.
2. Why mastering fabric grain is critical for your clothing business
2.1 Ensuring proper garment fit and comfort
Correct grain alignment is fundamental to achieving the intended garment fit. When pattern pieces are cut respecting the grain, clothes hang naturally on the body. The stability of the straight grain provides vertical structure, while the slight give of the cross grain allows for comfort across areas like shoulders or the bust. Cutting off-grain leads to garments pulling, twisting, or feeling restrictive, resulting in poor fit and customer dissatisfaction. Mastery of garment construction and tailoring principles starts with understanding grain.
2.2 Achieving the desired drape quality and silhouette
The way a fabric falls and shapes itself – its drape – is intrinsically linked to the grainline chosen during cutting. A skirt cut on the straight grain will have a more structured hang compared to the same skirt cut on the bias, which will offer a fluid, body-hugging silhouette. Understanding this allows designers and manufacturers to accurately translate a clothing design concept into a finished garment that looks and moves as envisioned. Drape quality is a key aesthetic factor controlled by grain.
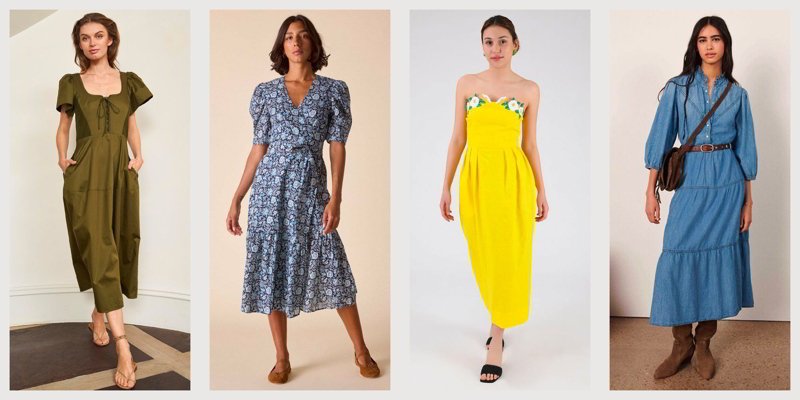
2.3 Enhancing durability & preventing distortion
Garments cut accurately on grain maintain their shape far better through repeated wear and laundering. Fabric stability is compromised when pieces are cut off-grain; these garments are prone to permanent stretching, twisting seams, sagging hems, or uneven wear. This distortion significantly reduces the product’s lifespan and perceived quality. Respecting the grain is an investment in the durability of your products.
2.4 Maintaining consistency across production
For businesses operating in wholesale or retail, consistency is paramount. Ensuring every garment of a specific style and size is cut on the correct grain guarantees uniformity in fit and appearance. This consistency builds brand reputation and trust with customers, minimizing returns related to quality variations or unexpected fit issues.
2.5 Material cost implications
While quality and fit are the primary drivers for correct grain alignment, understanding grain also aids in planning an efficient cutting layout. Knowing how pieces must align allows for better nesting of pattern pieces on the fabric, potentially minimizing waste. While accuracy should never be sacrificed for minor savings, knowledge of grain contributes to optimizing material usage.
3. How to reliably identify fabric grain
3.1 The selvage method
The simplest and most reliable method involves the selvage. The straight grain always runs parallel to these finished edges. Use the selvage as your primary guide whenever available.
3.2 Techniques for fabric pieces without selvages
The stretch test
This tactile method helps determine grain direction based on stretch properties. Gently pull the fabric along one cut edge. Then, pull along the perpendicular edge. Finally, pull the fabric diagonally.
- The direction with the least stretch is the straight grain.
- The direction with moderate stretch is the cross grain.
- The direction with the most stretch is the bias grain.
Visual inspection
Examine the weave structure closely, possibly under good light or magnification. In many fabrics, you can visually distinguish the thread direction – the straight lines of warp threads versus the weft threads woven across them. This method becomes easier with practice and on fabrics with more visible weaves.
The tear test (with caution)
Woven fabrics often tear cleanly along the straight or cross grain. Make a small snip (cut) near an edge and try tearing the fabric. A straight, clean tear indicates you are likely tearing along either the straight or cross grain. Exercise extreme caution: This method is destructive and unsuitable for valuable fabric, delicate materials, or finished pieces. Consider this a last resort or for verifying grain on scraps.
Pulling a thread
Near a cut edge, carefully isolate and pull out a single warp or weft thread. The narrow channel or line left behind by the removed thread represents a perfectly straight grainline (either lengthwise or crosswise). This technique can be meticulous but offers high accuracy.
3.3 Quick note on knit fabric vs. woven fabric
Woven fabric is constructed by interlacing threads at right angles (warp and weft), creating the grainlines discussed. Knit fabric, conversely, is made from interlocking loops of yarn. Knits do not have grain in the same sense. However, they possess directional properties: ‘wales’ (vertical columns of loops, similar to straight grain stability) and ‘courses’ (horizontal rows of loops, similar to cross grain stretch). Knits also have a direction of greatest stretch, which must be considered for pattern placement, much like grain in wovens.
4. Pattern layout and cutting precision
4.1 Reading sewing pattern markings
Most commercial sewing pattern pieces feature a long line with arrows at one or both ends. This is the grainline arrow. Standard practice dictates that this arrow must be aligned with the fabric’s straight grain (parallel to the selvage) unless specifically instructed otherwise (e.g., for a bias cut).
4.2 Accurate pattern alignment
Accurate pattern alignment is crucial. Place the pattern piece onto the fabric. Use a measuring tape or ruler:
- Measure the distance from one end of the grainline arrow to the selvage.
- Pin that end of the pattern piece in place.
- Measure the distance from the other end of the grainline arrow to the same selvage/grain line.
- Adjust the pattern piece until this second measurement is exactly the same as the first.
- Pin the entire pattern piece securely before proceeding with the cutting layout.
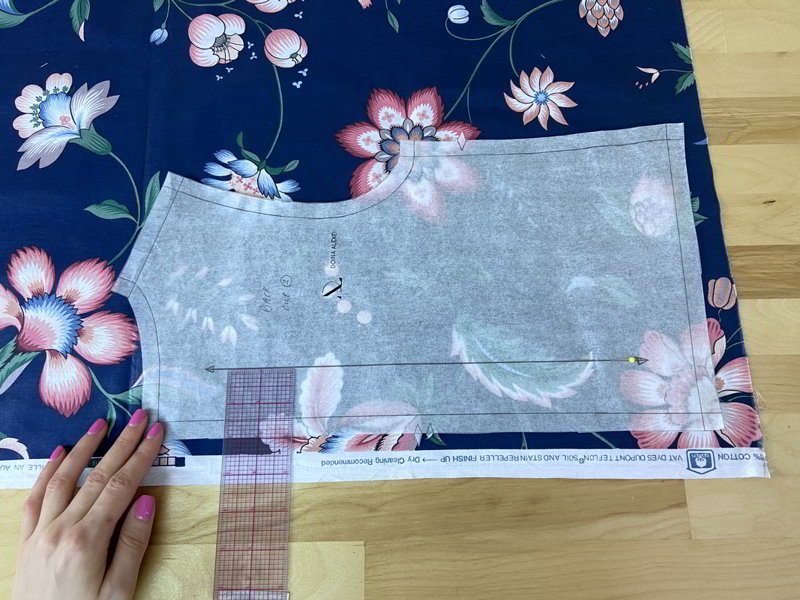
4.3 Handling directional prints & napped fabrics
Fabrics with directional prints (designs that run one way) or napped fabrics (textures with a direction, like velvet or corduroy) require extra attention. Not only must the grainline be correctly aligned, but all pattern pieces must also be laid out facing the same direction (“up”). Failure to do so results in mismatched prints or textures on the final garment. Often, a single-headed grainline arrow indicates the intended top direction of the pattern piece.
4.4 Cutting on the cross grain
While less common for main body pieces, cutting on the cross grain might be necessary for very wide pattern pieces that don’t fit on the straight grain, for maximizing fabric usage, or for specific design effects requiring horizontal stretch. Be aware of the potential drawbacks: slightly reduced stability and potentially more stretch across the piece than desired. Use caution, especially for structured or closely fitted garments.
4.5 Best practices for cutting
Achieving cutting precision ensures pieces fit together correctly, contributing to overall sewing accuracy. Follow these tips:
- Use sharp fabric scissors or a rotary cutter and mat.
- Ensure the fabric lies completely flat and smooth, without any wrinkles or tension.
- Use pattern weights or sufficient pins to hold the pattern securely in place.
- Cut carefully and precisely along the pattern lines.
5. Utilizing the bias cut: Drape, stretch, and design
5.1 The purpose of a bias cut
Why intentionally cut fabric on its stretchiest grain? The bias cut is chosen specifically because the 45-degree angle allows the weave structure maximum movement. This translates into exceptional fluidity and a soft, graceful drape that cannot be achieved on the straight or cross grain. Bias-cut fabric conforms beautifully to body curves and offers significantly increased elasticity, making certain designs possible.
5.2 Common uses
The unique properties of the bias cut lend themselves well to:
- Elegant skirts and dresses, particularly evening wear, known for their flowing silhouettes.
- Neckties, which require flexibility to knot smoothly.
- Creating bias tape for neatly finishing curved edges (like necklines and armholes).
- Decorative fabric trims and details.
- Collars designed to roll softly rather than stand stiffly.
5.3 Working with bias
Fabric cut on the bias requires careful handling during sewing due to its inherent stretchiness:
- Minimize handling of cut pieces before sewing to prevent stretching them out of shape.
- Consider stay-stitching (a line of straight stitches sewn just inside the seam allowance) on curved edges to stabilize them.
- Use plenty of pins or clips to hold seams together without stretching.
- Ensure the fabric feeds evenly through the sewing machine; a walking foot attachment can be helpful.
- Press seams gently using an up-and-down motion, avoiding pushing the iron along the seam, which can cause stretching.
6. Common problems from incorrect grain alignment
Here are common issues that arise from improper grain alignment:
- Twisting seams & uneven garments: One of the most obvious signs of off-grain cutting is seams that twist around the body, particularly noticeable on pant legs or side seams of shirts. Hems may also hang unevenly.
- Puckering along seams: If adjacent pattern pieces are cut on slightly different grains, or if one piece is stretched more than the other during sewing (often due to incorrect grain alignment), the resulting seam may appear puckered or slightly gathered instead of lying flat.
- Garment distortion after washing/wearing: Often, the most significant problems manifest after the garment is washed or worn. The fabric relaxes and settles according to its true grain, revealing cutting inaccuracies through permanent distortion such as twisting, sagging in certain areas, or uneven dimensions.
- Difficulty matching stripes/plaids: For fabrics with patterns like stripes or plaids, precise grain alignment is non-negotiable. Even a slight deviation from the correct grain will make matching the pattern across seams extremely difficult or impossible, resulting in an unprofessional finish.
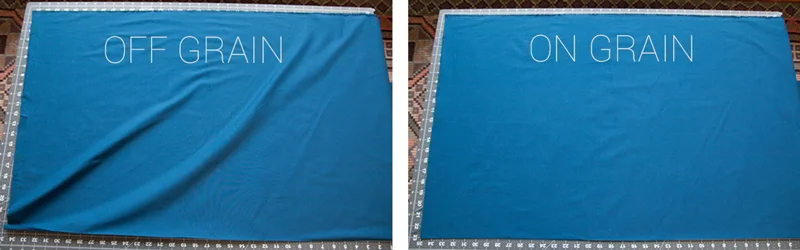
7. Related questions
7.1 How does pre-washing affect fabric grain?
Pre-washing (or pre-treating fabric according to care instructions) is highly recommended before cutting. This process allows the fabric to undergo any initial shrinkage or relaxation, settling into its stable dimensions. Pre-washing doesn’t alter the inherent grain direction (warp and weft remain the same), but it ensures that the grain you align your pattern pieces with is the fabric’s final, stable state. Neglecting this step, especially with natural fibers prone to shrinking, can lead to garments distorting after the first wash, even if cut correctly on the initial grain.
7.2 Does fabric grain matter for linings and interfacings?
Yes, grain alignment is crucial for linings and interfacings. Linings should generally be cut on the same grain as the outer fabric piece they will support. This ensures both layers hang and move compatibly, preventing the lining from pulling, bubbling, or restricting the outer fabric.
Fusible interfacings also often have a specific grain or direction of slight stretch; typically, this should align with the main fabric’s grain to provide support without hindering intended movement. Always refer to the interfacing manufacturer’s instructions for specific guidance.
7.3 How do I match patterns like plaids or stripes accurately with the grainline?
Matching patterns accurately requires careful attention to both the grainline and the pattern repeat. First, ensure the pattern piece’s grainline arrow is perfectly parallel to the fabric selvage (straight grain). Then, identify a dominant horizontal or vertical line within the plaid or stripe.
When laying out adjacent pattern pieces that will be seamed together, ensure corresponding points (often marked by notches on the pattern) align precisely along the same dominant pattern line on both pieces. This often necessitates cutting pieces individually (not on the fold) and may require extra fabric yardage.
7.4 Can I check the grain consistency of fabric before buying a whole bolt?
You can perform some basic checks, although a complete assessment isn’t always feasible before purchase. If possible, ask to unroll a yard or two of the fabric. Lay the fabric flat and look for obvious distortions: ‘bowing’ (where the cross grain threads curve instead of running straight across) or ‘skewing’ (where warp and weft threads are not perfectly perpendicular).
Perform a quick stretch test near the cut edge as described earlier. While these checks won’t guarantee perfection, they can help identify significant grain issues. Discussing quality control standards regarding grain alignment with your supplier is also advisable.
Read more:
Fabric grain is far more than a technical detail; understanding straight, cross, and bias directions is fundamental to professional garment construction. How fabric hangs, stretches, and wears is dictated by this inherent structure. Consistently identifying and utilizing the correct grain is a direct investment, translating into superior garment quality, accurate fit, enhanced durability, and reduced material waste.
Make grain alignment a standard, conscious step throughout your workflow, from pattern layout to sewing. This commitment elevates your final product’s professionalism, builds brand reputation through reliable quality, and ensures customer satisfaction. Mastering fabric properties is ongoing; seek expert resources for complex textile challenges.