This guide targets individuals and businesses seeking high-quality, textured prints for custom apparel, promotional products, and unique branding solutions. The challenge often lies in choosing the right printing method to achieve desired aesthetics and durability, creating a strong brand impact. Selecting the wrong technique can lead to a compromised brand image and wasted resources. High-density screen printing emerges as a powerful solution for those seeking a premium, texturized print that truly stands out. This guide demystifies the process, offering detailed insights into the technique, its benefits, practical applications, design considerations, and how to find reliable printing services. Armed with this knowledge, users can create visually compelling products that enhance their brand image and leave a lasting impression.
1. What is high-density screen printing?
1.1 Definition and overview
For businesses seeking to add a distinctive and tactile dimension to their clothing designs, high-density screen printing emerges as a powerful technique. This method utilizes specialized inks that are significantly thicker than those used in traditional screen printing.
The result is a design that noticeably rises above the fabric surface, creating a pronounced three-dimensional effect that is both visually striking and appealing to the touch.
Compared to standard screen printing, high-density printing offers a richer texture and a more substantial feel. The increased ink volume allows for intricate layering techniques, enabling designers to build depth and complexity into their creations.
This opens up exciting possibilities for brands looking to create memorable and impactful visual elements on their garments. The adaptability of high-density inks extends across a wide range of fabric types and design complexities, making it a valuable tool for businesses aiming to elevate their brand identity through unique and high-quality printed details.
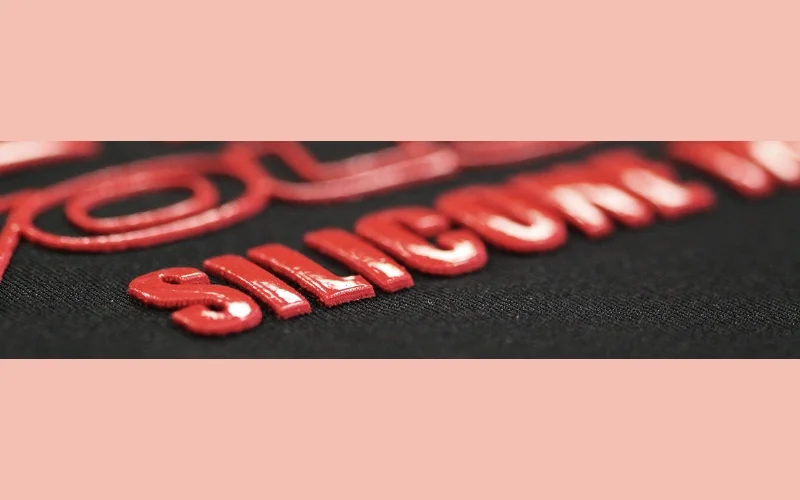
1.2 The science behind high-density: Inks and mesh
The magic of high-density screen printing lies in a carefully orchestrated interplay between specialized inks and precisely chosen mesh screens. To achieve the signature three-dimensional effect, this technique primarily relies on plastisol inks.
The inherent properties of plastisol are perfectly suited for this purpose. Its notably thick consistency is not just a characteristic, but a critical requirement. This viscosity allows the ink to hold sharp details and, more importantly, to be built up in layers, creating the desired raised texture that defines high-density prints. Think of it like sculpting with ink – plastisol’s body allows for controlled and precise shaping.
The selection of mesh count in the screen printing process is equally vital and directly linked to the thick nature of plastisol inks. A lower mesh count is deliberately chosen to create larger openings in the screen. These larger openings are necessary to accommodate the significantly thicker deposits of plastisol ink.
Imagine trying to squeeze toothpaste through a fine sieve – it simply wouldn’t work. Similarly, a high mesh count screen, with its fine weave, would restrict the flow of thick plastisol ink, hindering the ability to build up the desired height. Therefore, a lower mesh count acts as a wider channel, allowing ample ink to pass through and accumulate on the fabric, forming the raised print.
Furthermore, proper tension of the screen printing mesh is paramount. This is a delicate balance. If the mesh is too loose, the print is likely to suffer from uneven ink distribution or unwanted distortions, compromising the clarity and sharpness of the design.
Conversely, if the mesh is stretched too tightly, it can restrict the ink flow, preventing sufficient ink deposition and ultimately diminishing the intended high-density effect. Achieving the correct tension ensures consistent ink transfer and precise control over the printed design.
While other types of inks exist in the screen printing world, such as water-based and discharge inks, they generally fall short when aiming for high-density effects. Their thinner viscosity, a characteristic often prized for other printing styles, becomes a limitation in this context.
These alternative inks simply lack the necessary body and structure to be effectively built up into the raised, textured designs that define high-density printing. They are designed to penetrate the fabric more than sit on top, which is the opposite of what’s needed for a 3D effect.
In essence, the success of high-density screen printing hinges on understanding and manipulating the specific characteristics of the chosen ink, particularly its viscosity, and carefully matching it with the appropriate mesh count and tension.
Each element plays a crucial role in determining the final print quality and the degree of the desired three-dimensional effect. For businesses venturing into high-density printing, mastering these technical aspects is key to achieving impactful and visually stunning results.
1.3 Advantages of high-density printing: Durability, visual appeal, tactile feel
High-density printing boasts exceptional durability thanks to its thick ink layer, ensuring lasting impressions on various materials. The raised texture, coupled with the interplay of shadows and dimensional effects, creates a captivating visual appeal that truly stands out. This unique aesthetic transcends a simple flat print, offering a tactile experience – a pronounced difference in feel that adds depth and visual interest. The bold, textured designs are ideal for adding a premium touch to apparel, promotional items, and more, making a strong visual impact and creating a tangible link with the brand.
2. High-density vs. other printing methods
2.1 High-density vs. standard screen printing
High-density screen printing stands apart from standard screen printing primarily in the ink thickness and resulting print height. Standard screen printing, with its thinner ink films, excels at simpler designs. Conversely, high-density printing, utilizing thicker ink, is ideal for bolder, more textured graphics with a raised, three-dimensional effect.
The greater ink volume in high-density printing allows for deeper, more defined designs, making it the preferred method for complex imagery and impactful visual statements. Standard screen printing is better suited for basic designs with a more uniform, flat print, while high-density printing prioritizes a visual impact that distinguishes itself with its unique texture and depth.
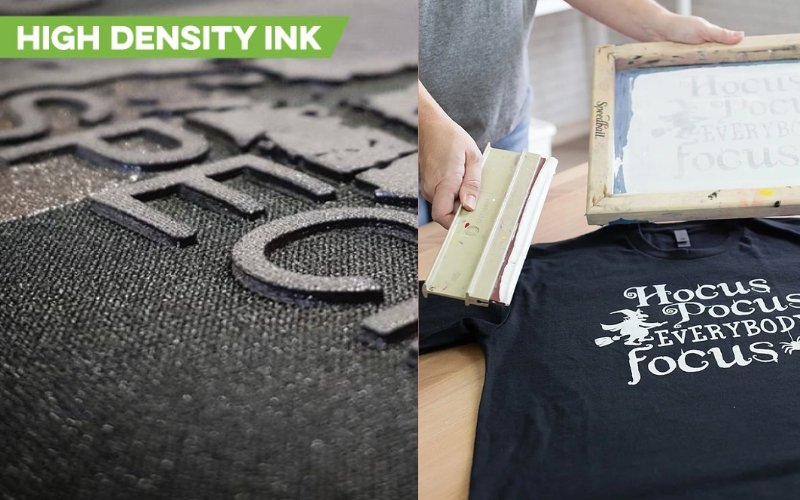
2.2 High-density vs. puff printing, embossing, debossing
High-density and puff printing both create raised designs, but their results differ significantly. High-density screen printing builds up layers of thick ink for a crisp, textured, and often more durable finish, ideal for intricate details and sharp edges. Puff printing, on the other hand, utilizes ink that expands upon heating, creating a softer, more three-dimensional, almost spongy texture, less suitable for precise lines or complex shapes.
High-density’s control over the raised effect makes it preferable for designs requiring greater durability and precision, while puff printing excels at achieving a more tactile and playful aesthetic. The final choice depends on the specific design goals and desired outcome.
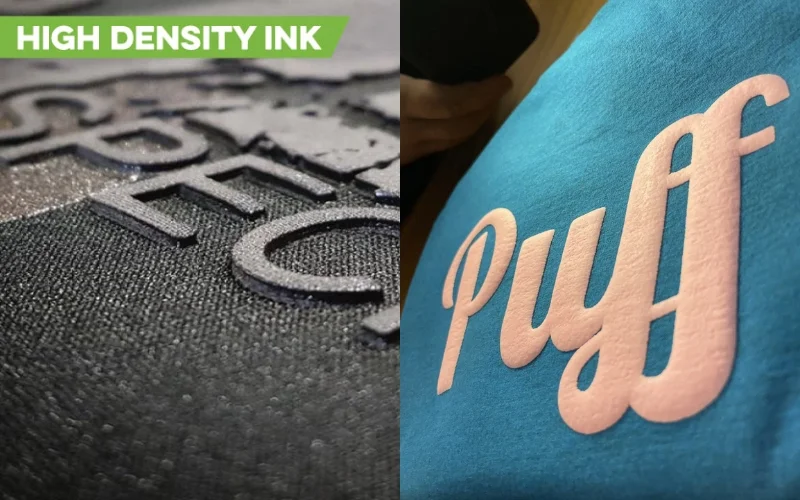
2.3 High-density vs. digital printing (DTG), heat transfer
In the world of apparel decoration, businesses have a variety of printing techniques at their disposal, each with its own set of advantages and limitations. Among these, high-density screen printing, digital printing (DTG), and heat transfer stand out as popular choices, but they cater to different needs and design goals. Understanding their distinct characteristics is crucial for making informed decisions about which method best suits a particular project.
High-density screen printing truly shines when the objective is to create designs that are not only visually striking but also physically tangible. This technique excels at producing incredibly durable prints with a pronounced raised, three-dimensional texture that is both seen and felt.
The use of thicker inks allows for rich, vibrant colors and the reproduction of intricate details, making it ideal for designs that demand attention and a premium feel. Furthermore, high-density screen printing is versatile and can be applied to a wide array of fabrics.
However, it’s worth noting that setting up for screen printing, especially high-density, can involve more upfront costs, making it generally more economical for larger production runs rather than small, custom orders.
Digital printing, or DTG (Direct-to-Garment) printing, offers a different set of strengths. Its primary advantage lies in its speed and design flexibility. DTG is particularly well-suited for complex designs with many colors, gradients, or even photographic images, which can be challenging and costly to reproduce with traditional screen printing.
It also excels in customization and short runs, as there are minimal setup costs involved. If a business needs to quickly produce a small batch of shirts with unique, intricate designs, DTG is often the go-to solution. However, when considering durability, especially for garments that will undergo heavy use or frequent washing, DTG prints may not hold up as robustly as screen-printed designs, particularly on heavier or water-resistant fabrics.
Additionally, while DTG can achieve a slight texture, it typically doesn’t replicate the substantial raised effect characteristic of high-density screen printing. The print feel can sometimes be less pronounced and more integrated into the fabric.
Heat transfer printing presents yet another option, often favored for its moderate cost and relatively quick turnaround times. It can be a practical choice for simpler designs and works well on certain types of fabrics. Heat transfer is often used for promotional items or designs where extreme durability isn’t the primary concern.
However, this method typically falls short when aiming for the rich, layered textures and depth achievable with high-density screen printing. The print quality and feel can sometimes be less premium compared to screen printing or even DTG, and durability, especially under intensive use and washing, can be a limitation.
Ultimately, the “best” printing method isn’t universal; it’s highly dependent on the specific requirements of each project. Factors such as the complexity of the design, the desired level of durability, the volume of items to be printed, and the budget all play crucial roles in determining whether high-density screen printing, DTG, heat transfer, or another technique is the most appropriate choice.
For businesses, carefully weighing these factors against the strengths and weaknesses of each printing method is key to achieving optimal results and customer satisfaction.
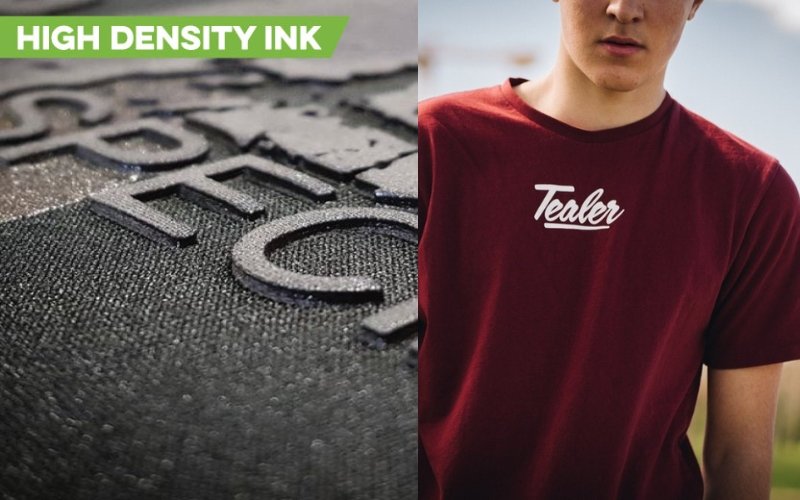
3. Applications of high-density screen Printing
3.1 Apparel and fashion (t-shirts, hoodies, etc.)
High-density screen printing elevates apparel with a distinctive visual and tactile impact. The technique’s ability to create raised, textured designs makes it a popular choice for t-shirts, hoodies, jackets, and other garments.
The unique texture adds depth and dimension to streetwear designs, offering a bold aesthetic that’s highly sought after. Similarly, in sports apparel, high-density printing allows for impactful team logos and graphics that are not only visually striking but also durable enough to withstand the rigors of athletic activity.
The three-dimensional quality of high-density prints translates seamlessly into workwear, providing a sophisticated branding element for durable and stylish apparel. The raised texture of high-density prints stands out prominently on various garments, making it a standout option for fashion-forward designs, athletic wear, and professional attire.
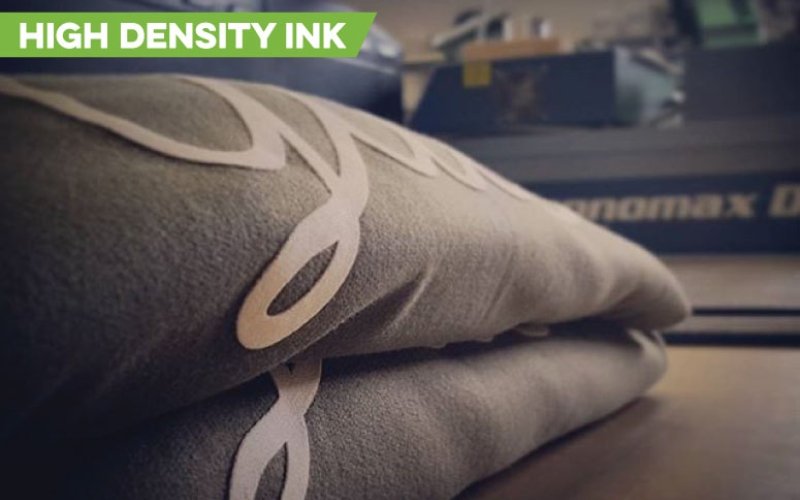
3.2 Promotional products (bags, pens, etc.)
High-density screen printing transforms everyday promotional products into memorable brand ambassadors. The technique’s ability to create raised, textured designs elevates items like tote bags, water bottles, pens, and keychains to a premium aesthetic.
The tactile element of high-density printing makes these items more engaging, adding a unique “feel” that enhances the overall brand experience. A custom logo printed in high-density on a tote bag, for example, stands out and leaves a lasting impression.
The raised texture on a branded water bottle, or the distinctive feel of a high-density logo on a pen or keychain, can elevate a simple promotional item into a more premium and engaging corporate gift. High-density printing’s durability also ensures that these promotional tools maintain their visual appeal and the brand’s message, even with repeated use, making them effective and enduring marketing tools.
3.3 Art and design (limited edition prints, posters)
High-density screen printing provides artists and designers with a powerful tool for creating unique and textured artwork. The technique’s ability to produce raised, three-dimensional designs allows for the creation of limited-edition prints and posters with a compelling tactile and visual impact.
This unique texture elevates the visual experience, offering depth and a distinctive feel reminiscent of impasto painting techniques, where layers of paint build up on the canvas. The high-density approach allows for a rich interplay of colors and textures, creating a tactile and visual experience that transcends traditional flat prints.
The durability of high-density screen printing further enhances its appeal as a medium for limited-edition artwork, ensuring that these prints maintain their visual impact and tactile quality for years to come.
4. Designing for high-density screen printing
4.1 Artwork preparation (vector art, halftones)
The foundation of any exceptional high-density screen print lies in meticulous artwork preparation. Think of it as laying the groundwork for a building – a solid foundation is crucial for a lasting and impressive structure. In this context, proper artwork preparation is not just a step, but a prerequisite for achieving the desired three-dimensional effect and crisp details that define high-density printing.
Vector artwork is absolutely essential for high-density screen printing. Unlike raster images which are made of pixels, vector graphics are built using mathematical formulas that define points, lines, and curves. This fundamental difference is key.
Vector art offers unparalleled scalability. Designs can be enlarged or reduced without any loss of detail or sharpness, ensuring that intricate elements remain crisp and clean regardless of the final print size on the garment.
For businesses, this means artwork created once can be used across various garment sizes and styles without compromising quality. Using vector art guarantees that the edges of your design will be smooth and well-defined, which is particularly important when working with the thick inks of high-density printing.
While halftone images are commonly used in standard printing to create gradients and simulate shades using dots, they often present challenges in high-density screen printing. The very nature of high-density printing, with its thick ink and raised texture, can work against the subtle nuances of halftone patterns.
The fine lines and delicate gradations that halftones rely on can become blurred or lost when reproduced with thick inks. The raised texture can also distort the intended visual effect of the halftone dots, leading to a less refined and less predictable outcome.
Therefore, when designing for high-density, it’s generally advisable to move away from traditional halftones for achieving color transitions and gradients. Instead, explore alternative techniques that are better suited to the medium.
One effective approach is to utilize a solid color palette. By carefully selecting and combining distinct solid colors, designers can create visually striking designs with clear definition and impact, perfectly complementing the bold nature of high-density printing. Another powerful technique is layering. Overlapping solid shapes of different colors can create the illusion of depth and color variation without relying on the problematic fine dots of halftones.
For smoother transitions, consider incorporating a gradient mesh in vector design software. This allows for controlled and visually impactful gradients that are rendered as solid areas rather than halftone dots, resulting in a cleaner and more predictable outcome in high-density printing.
For designs that incorporate multiple colors, precise color separation is absolutely critical. Each color in the design needs to be separated into its own layer in the artwork file. This separation is essential for creating individual screens for each color during the screen printing process.
Accurate color separation ensures that each color is printed in its designated area without unwanted overlap or gaps. Furthermore, including clear registration marks in the artwork is equally vital, especially for multi-color designs.
Registration marks are small, precisely placed symbols that act as guides for aligning the different color screens during the printing process. These marks ensure that each color layer is printed in perfect alignment with the others, preventing any misalignment or blurring in the final multi-colored print.
In conclusion, successful high-density screen printing hinges on starting with a high-quality vector file, steering clear of traditional halftones, and ensuring meticulous color separation and registration. Investing time and attention in these artwork preparation steps is not just good practice; it’s the key to achieving professional-looking, impactful, and visually stunning high-density prints that will truly elevate your apparel designs.
4.2 Color considerations (pantone colors, color matching)
Color selection plays a significant role in the final outcome of high-density screen printed designs. Accurate color matching is crucial, especially for high-quality results. Using Pantone colors ensures consistent color reproduction across different prints, preventing variations in hue and saturation.
High-density printing, while capable of vibrant colors, may present limitations in achieving smooth gradients and subtle color transitions. The raised texture of the high-density print can sometimes make it challenging to reproduce nuanced gradients.
In these cases, a simplified color palette or bolder, more distinct color blocks might be more effective. Accurate color matching starts with careful selection of Pantone-matched inks and precise color separation during the design process. This meticulous attention to color accuracy and preparation is vital for achieving the desired visual impact.
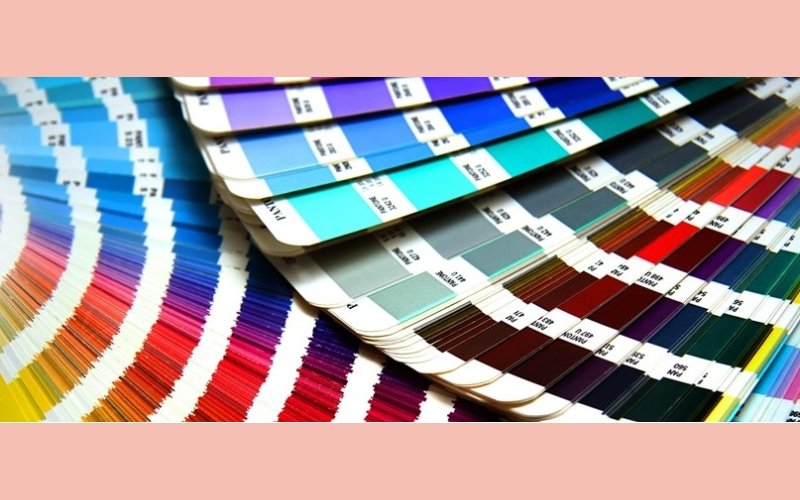
4.3 Choosing the right ink (plastisol, water-based, discharge)
Selecting the appropriate ink is crucial for achieving the desired look and feel in high-density screen printing. Plastisol ink, renowned for its opacity and durability, is a popular choice for high-density printing, particularly for applications requiring long-lasting color and a substantial raised texture.
Its thick consistency allows for excellent ink build-up, but its curing process often requires higher temperatures and specialized equipment. Water-based inks, conversely, offer a softer hand feel and are suitable for garments where a less substantial texture is desired, but their durability and opacity are generally lower than plastisol.
Discharge inks, specifically designed to create vibrant colors on dark fabrics, are a strong alternative, but may not offer the same high-density texture as plastisol. The curing process for each ink type differs. Plastisol requires heat-curing at higher temperatures to achieve maximum adhesion and durability.
Water-based inks cure through evaporation. Discharge inks often have a specific curing process requiring particular temperatures. Careful consideration of the fabric type, the desired print effect, and the overall durability requirements of the project should guide your ink choice, ensuring both a visually appealing and long-lasting result.
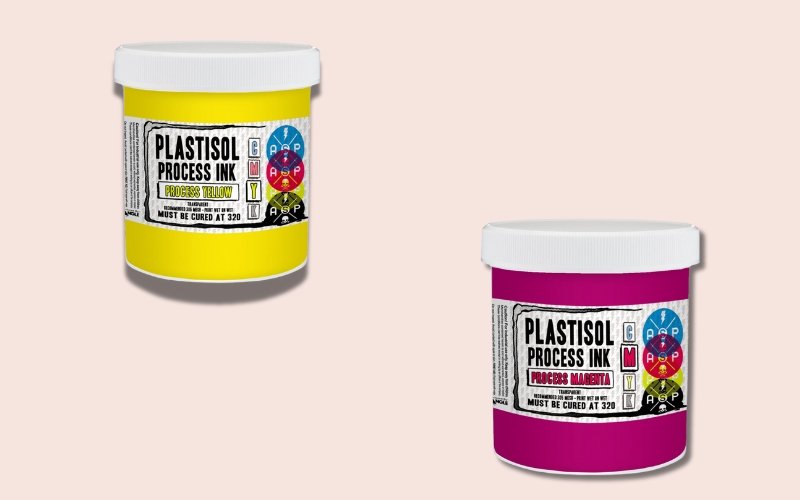
5. The high-density screen printing process: A step-by-step guide
5.1 From design to finished product
High-density screen printing is a fascinating process that transforms flat fabric into a textured canvas, adding a unique three-dimensional dimension to apparel designs. This technique achieves its raised effect through a meticulous process of layering specialized inks. Let’s break down the journey from initial design to the final, touchable product:
Step 1: Stencil Creation – Defining the Design’s Blueprint
The first crucial step is stencil creation. In screen printing, the stencil, often referred to as a screen, acts as a template that precisely defines the outlines of your design on the garment. This stencil is typically created on a fine mesh screen, stretched tautly over a frame.
A light-sensitive emulsion is applied to the screen, and a positive image of your design is then placed onto the emulsion. Exposing this setup to UV light hardens the emulsion in the areas not covered by the design, while the areas under the design remain soft.
These soft, unexposed areas are then washed away, leaving behind open mesh areas that perfectly correspond to your design. This creates the stencil – areas where ink will pass through and areas where it will be blocked. The precision of this stencil creation process is paramount as it directly dictates the sharpness and accuracy of the final printed design.
Step 2: Ink Application – Building the Raised Dimension Layer by Layer
With the stencil prepared, the next stage is ink application. This is where the magic of high-density printing truly begins. Specialized high-density ink, typically plastisol-based due to its thickness and buildable nature, is carefully applied to the screen.
Using a squeegee, the ink is forced across the screen, passing through the open areas of the stencil and onto the fabric beneath. What sets high-density printing apart is the technique of meticulous layering. Instead of a single pass of ink, multiple layers are applied, one on top of the other.
Each layer builds upon the previous one, gradually increasing the ink deposit and creating the desired raised effect. The number of layers applied directly influences the height and prominence of the three-dimensional element.
Skilled printers carefully control the pressure and angle of the squeegee, as well as the number of passes, to ensure even and consistent ink deposition, crucial for achieving a uniform and professional raised print.
Step 3: Curing Process – Setting the Ink for Durability and Longevity
Once the desired number of ink layers has been applied, the garment moves to the curing process. This step is essential for permanently setting the ink and ensuring both the durability and shape retention of the raised design.
Curing involves exposing the printed garment to controlled heat, typically using a conveyor dryer. The heat activates the plastisol ink, causing it to gel and solidify. Proper curing is critical; under-curing can lead to the ink cracking or washing out, while over-curing can scorch the fabric or alter the ink’s texture.
The curing process effectively transforms the wet ink layers into a robust, raised print that is bonded to the fabric, capable of withstanding wear and washing.
Step 4: Layering and Enhancement Options – Expanding Design Possibilities
High-density printing offers significant creative flexibility through layering and enhancement options. Designs can be further enhanced by adding even more layers of high-density ink to achieve an even more pronounced texture and dramatic three-dimensional effect.
This allows for the creation of truly tactile prints that stand out both visually and to the touch. Furthermore, high-density printing can be seamlessly combined with traditional screen printing inks. For example, a design might incorporate a flat, traditionally printed background with raised high-density elements on top, creating a dynamic contrast in texture and dimension.
This combination approach opens up a wide range of design possibilities, allowing businesses to create visually complex and multi-layered apparel graphics.
Step 5: Precision Control – Achieving Consistent and Refined Results
A key advantage of high-density screen printing is its precision control over the height and placement of the raised elements. Unlike less controlled methods like puff paints, which can sometimes spread or distort unpredictably, high-density printing allows for meticulous control throughout the process.
From the precise stencil creation to the controlled layering of ink, every step is designed to ensure consistent and predictable results. This level of control is crucial for achieving professional-quality prints where the raised elements are exactly where intended, with clean edges and uniform height across the entire print run.
This consistency is particularly important for brands seeking to maintain a high standard of quality and visual appeal in their apparel.
In summary, high-density screen printing is a sophisticated process that combines stencil creation, layered ink application, precise curing, and creative layering options to produce durable and visually striking three-dimensional prints.
The precision and control inherent in this technique make it a valuable tool for businesses looking to elevate their apparel designs and create products that are both visually appealing and uniquely tactile.
5.2 Key questions to ask a printer
When seeking a printer for your projects, a thorough inquiry is crucial. Ask about minimum order quantities (MOQ) to understand the printer’s production capacity and if it aligns with your needs. Inquire about their pricing structures, clarifying whether they offer discounts for larger orders or volume printing.
Turnaround time is essential; understand how long the printing process takes, including design proofing and delivery. Be specific about the ink and garment options available, and ask about their experience with various fabric types. Delve into their artwork requirements, do they need vector files, specific formats, or specific color profiles?
Finally, inquire about their experience with similar projects. Ask for examples of past work, especially if the project involves a specific design or style. Understanding their experience with your type of project, whether for apparel, promotional items, or artwork is crucial for a smooth and successful collaboration. These detailed questions provide critical information to assess a printer’s capabilities and ensure a suitable fit for your project.
6. FAQs about high-density screen printing
6.1 What is the difference between high-density and puff printing?
High-density and puff printing both create raised effects, but their methods and results differ significantly. High-density screen printing uses thick, specialized ink that builds up from the fabric’s surface, creating a substantial, often textured, and durable raised design.
The process involves layering ink to achieve depth and visual impact. Puff printing, on the other hand, employs a different ink that expands and puffs up when heated, resulting in a lighter, more “bubbled” three-dimensional effect.
This expansion is a key characteristic that gives puff printing its distinctive, less substantial texture. The final appearance of puff prints might be softer, more irregular, and less precise than the crisp, controlled textures achievable with high-density printing.
6.2 What types of garments are best suited for high-density printing?
Heavier fabrics with a substantial weave are best suited for high-density printing. The thick, layered ink characteristic of this technique requires a robust substrate to hold the raised texture without distortion. Cotton fabrics, including blends with cotton, generally excel at accommodating the ink’s build-up.
The denser weave and weight of these fabrics provide a stable base for the raised elements, leading to a more impactful and long-lasting result. Conversely, delicate fabrics like silks, chiffons, or sheer materials might not support the substantial ink layer and could be damaged by the printing process or subsequent handling.
The printing process’s inherent pressure and the ink’s thickness can also stretch or warp such fine materials. Therefore, when high-density printing is chosen, it’s critical to consider the fabric weight and structure to ensure optimal results and prevent potential damage.
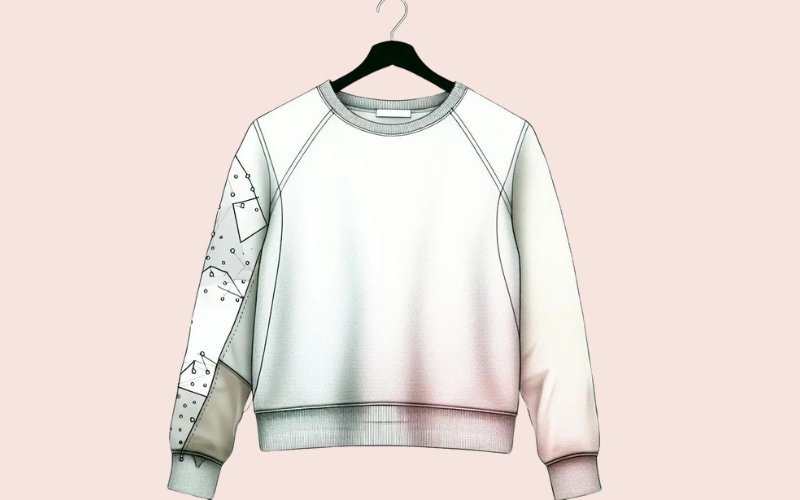
6.3 How much does high-density screen printing cost?
The cost of high-density screen printing varies significantly and depends on several factors. Quantity plays a major role; larger orders often command lower per-unit costs. The complexity of the design, including the number of colors and intricate details, also affects the price. Similarly, the choice of garment material impacts pricing; more specialized or heavier fabrics may increase the cost of the printing process. Seeking quotes from multiple printers is essential for comparison. Shop around, carefully evaluating not just the price but also the turnaround time and the quality of the printing samples provided, to ensure you’re getting the best value for your investment. These factors should be considered when evaluating the overall cost of a high-density screen printing project.
6.4 How long does high-density screen printing last?
High-density screen prints, when properly applied, can last for years with appropriate care. The thick ink layers contribute to exceptional durability, making these prints resilient to everyday wear and tear. Factors like the quality of the ink, the type of fabric, and the care the garment receives all impact longevity. To maximize the lifespan of high-density prints, it’s recommended to follow proper garment care instructions—avoid harsh chemicals, choose gentle washing cycles, and allow garments to air dry whenever possible. These precautions will help prevent the print from fading, peeling, or losing its three-dimensional texture over time, preserving the visual appeal of the design for years to come.
6.5 Can I print high-density on dark-colored garments?
High-density printing on dark-colored garments is achievable with the right inks and sometimes a preparatory base layer. Plastisol inks, especially those with high opacity, are well-suited for dark fabrics, as they provide excellent color vibrancy and coverage. In some cases, a base white layer beneath the design can enhance color and reduce the need for extremely opaque inks, allowing a more nuanced look. However, the choice of inks and the method of applying base layers should be discussed with the printer to ensure optimal results for the specific fabric and design.
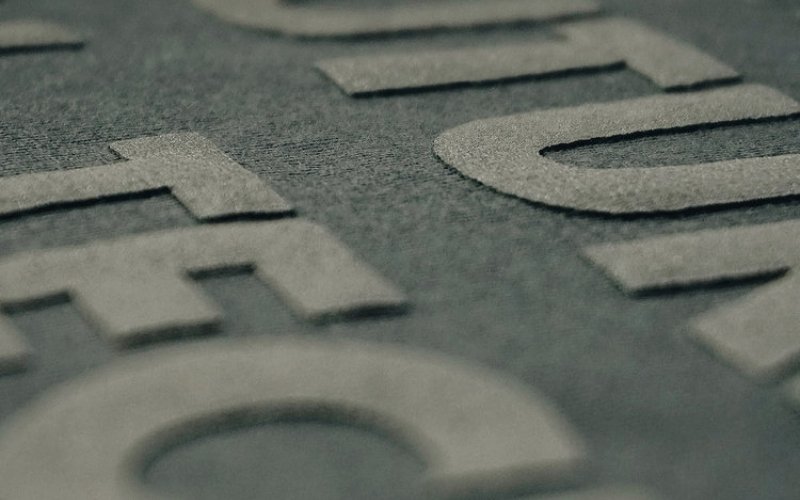
6.6 What file format do I need for my artwork?
Vector file formats (.ai, .eps, .svg) are essential for high-density screen printing. Raster formats (.jpg, .png) are not suitable for this technique because they are made up of pixels, losing detail and clarity when enlarged. Vector files, on the other hand, are based on mathematical formulas, allowing for scalable enlargement without loss of quality. If you have raster artwork, it can be converted to a vector format using specialized software. This conversion step ensures the high resolution and clean lines necessary for the raised, textured effect of high-density printing.
7. My Pack Love – Providing services for high-density printing and more
My Pack Love provides high-quality custom printing solutions, specializing in the vibrant and durable world of high-density screen printing. We’re dedicated to helping customers achieve unique and impactful branding for their apparel, promotional products, and more. Our expertise extends beyond the print itself, offering a comprehensive suite of complementary branding solutions to maximize your project’s impact. From the Value Booster Kit—bundling essential products for significant savings—to our range of high-quality woven labels, heat transfer labels, and durable rubber labels, we offer everything you need to create a polished and professional look.
Our zipper bags offer secure packaging, while poly mailers ensure safe shipping. Transform your ideas into tangible, high-quality products that leave a lasting impression. Contact us today for a custom quote, browse our complete product catalog for additional branding options, or request a free sample kit. Connect with us at +84 363615867 or [email protected], or visit us online at https://mypacklove.com/
Read more:
- Cub Scout Uniform Patch Placement Guide 2025
- OCP Patch Placement: Army Uniform Regulations and Guide
- Remove Iron-On Patches: Easy and Safe Methods for All Fabrics
High-density screen printing offers a unique blend of durability, texture, and visual appeal, making it a powerful tool for elevating brands and creating lasting impressions. The raised, three-dimensional quality of this technique sets it apart, adding a distinct tactile experience and a premium look to a wide array of applications, from apparel to promotional products. Whether you’re a business seeking a unique branding solution or an artist looking for a distinctive printing method for your artwork, high-density screen printing provides a solution that stands out. For expert advice and custom printing solutions, contact My Pack Love. Get a free quote today and explore the potential of high-density screen printing to elevate your projects to the next level.