Small clothing businesses often grapple with achieving consistent sizing and fit across their garments, a challenge that can directly impact customer satisfaction and brand reputation. The critical link between a creative design vision and a garment that can be accurately and repeatedly produced lies in Pattern Making. Consider pattern making the essential blueprint for your apparel business, translating abstract ideas into tangible instructions for production.
This article serves as a comprehensive guide, explaining precisely what pattern making entails, why mastering this process is vital for your business, the different methods and tools involved, and its crucial role in ensuring success from initial concept to finished product. Understanding pattern making empowers you to build a foundation for quality, consistency, and growth. Let’s delve into the specifics!
1. Decoding Pattern Making: More Than Just a Template
1.1 Defining Pattern Making
Pattern Making is the process of creating a precise template, typically on paper or digitally using CAD (Computer-Aided Design) software, from which individual pieces of a garment are cut from fabric. Fundamentally, pattern making translates a flat, 2D design sketch into a functional guide for constructing a 3D product. This blueprint acts as the technical interpretation of the designer’s vision, detailing the exact shape and size of each component needed for garment construction.
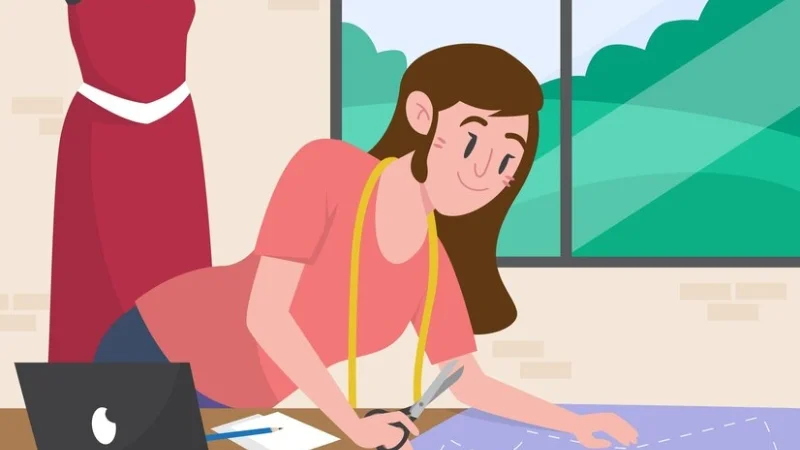
1.2 The Purpose: Why Patterns are Foundational
Patterns serve several critical functions in apparel production, making them truly foundational:
- Accuracy: They ensure every piece is cut precisely according to the intended design specifications.
- Replicability: Patterns allow for consistent reproduction of garments across multiple production runs, crucial for maintaining sizing standards.
- Communication: They act as a vital technical communication tool, conveying exact requirements from the designer to the manufacturer or sewing team.
- Fit: The pattern forms the very basis of garment fit, dictating how the final product will drape and conform to the body.
1.3 Pattern Making vs. Fabric Pattern Design
A common point of confusion involves distinguishing between a sewing pattern and a fabric pattern. The sewing pattern, which is the focus here, refers to the template or blueprint that defines the structure and shape of the garment pieces (like the shape of a sleeve piece cut from paper). In contrast, a fabric pattern refers to the visual surface design printed or woven onto the fabric itself. Think of the sewing pattern as the construction plan, while the fabric pattern is the decorative finish.
2. Why Accurate Patterns are Crucial for Your Clothing Brand’s Success
2.1 Ensuring Consistent Fit and Quality Across Batches
Accurate patterns are the bedrock of reliable sizing and consistent fit. When patterns are precise, every garment produced adheres to the same measurements, building customer loyalty and drastically reducing return rates due to poor fit. This consistency directly translates into a perception of higher quality and professionalism for your brand.
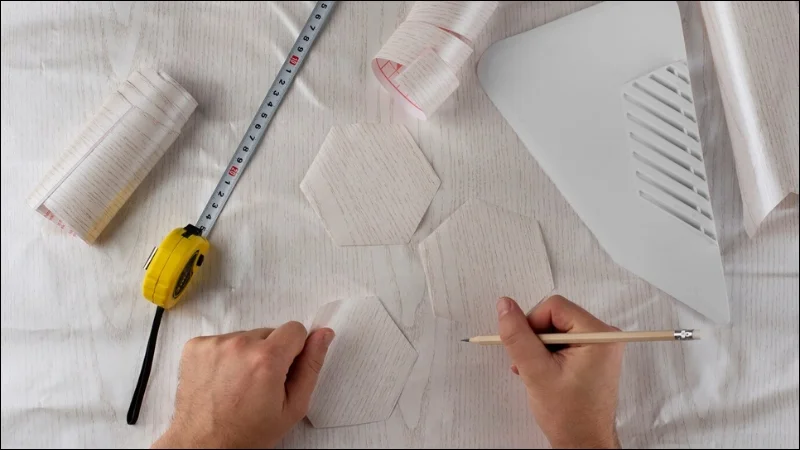
2.2 Minimizing Errors and Material Waste During Fabric Cutting & Sewing Construction
Well-drafted patterns significantly reduce errors during the fabric cutting stage. They allow for optimal layout on the fabric, minimizing material waste – a crucial factor for controlling costs. Furthermore, accurate patterns with clear markings streamline the sewing construction process, reducing assembly time and potential mistakes, leading to greater efficiency and cost savings in both materials and labor.
2.3 Building Brand Trust and Customer Loyalty Through Reliable Garments
When customers purchase clothing from your brand and consistently find that the garments fit as expected, they develop confidence and brand trust. This reliability, born from consistent fit enabled by accurate patterns, encourages repeat purchases and positive word-of-mouth recommendations, forming the foundation of lasting customer loyalty. Reliable garments become a hallmark of your brand’s promise.
2.4 Facilitating Clear Communication with Manufacturers
Patterns serve as a universal language in garment production. When included as part of a comprehensive Tech Pack (a detailed document outlining all specifications for producing a garment), patterns provide precise instructions to manufacturers. This clarity minimizes misunderstandings, reduces the risk of errors, and ensures the final product accurately reflects the original design intent, regardless of where production takes place.
2.5 Solving Common Fitting Issues
Pattern making techniques directly address how a garment fits the human body. Methods like dart manipulation (creating folds to shape the fabric around curves) and the strategic addition of ‘ease’ (extra room built into the pattern for comfort and movement) solve common fitting issues such as tightness across the bust or shoulders, pulling lines, or poor drape (how the fabric hangs). Effective pattern making anticipates and resolves these problems before they reach the customer.
3. Key Methods of Pattern Creation: Drafting vs. Draping
3.1 Flat Pattern Drafting: The Technical Approach
Flat Pattern Drafting is a method that uses precise body measurements or standardized size charts to create basic foundational patterns, known as blocks or slopers (e.g., a basic bodice block or sleeve block), directly onto pattern paper or using CAD software.
These blocks represent a close fit to the body without style details. From these base blocks, pattern makers use technical drawings and manipulation techniques—such as pivoting darts or adding fullness—to develop patterns for various styles. This approach relies heavily on geometric principles and accurate calculations, often utilizing specialized drafting tools. Foundational work in this area, like that of Helen Joseph Armstrong, established many standard techniques still used today.
3.2 Draping: Sculpting Directly with Fabric
Draping offers a more sculptural approach to pattern creation. This method involves manipulating fabric, often inexpensive muslin fabric, directly onto a dress form (a mannequin representing body dimensions). The pattern maker pins, folds, and cuts the fabric on the form to achieve the desired silhouette and 3D shape.
Markings made on the draped fabric are then carefully transferred onto paper to create the flat pattern pieces. Draping is particularly valuable for understanding fabric behavior, working with complex or asymmetrical designs, and visualizing the garment in three dimensions early in the process.
4. Essential Tools & Terminology for Your Production Toolkit
4.1 Basic Pattern Making Tools Overview
Having the right pattern making tools is essential for accuracy and efficiency. Here are some basics:
- Pattern Paper: Used for drafting and tracing patterns. Common types include Dot paper (with grid markings), Kraft paper (sturdy brown paper), or Oak Tag (heavy-duty cardstock often used for durable master patterns or slopers).
- Measuring Tools: A flexible Tape Measure for body measurements, clear plastic rulers (like L-squares and grading rulers) for straight lines, and French Curves for drawing smooth curves (armholes, necklines).
- Marking Tools: Pencils for drawing, tracing wheels and carbon paper for transferring markings between paper layers or onto muslin, and colored pencils for differentiating lines.
- Cutting Tools: Sharp shears dedicated only for paper (to avoid dulling), separate fabric shears, and potentially a rotary cutter and mat for straight cuts.
- Notchers & Awls: Notchers create small nicks in the pattern edge to mark seam allowances or matching points. An awl creates small holes for marking dart points or pocket placements.
- Dress Form: A mannequin padded to specific body measurements, essential for draping and checking the fit of pattern prototypes.
- CAD Software (Digital Option): Programs like Lectra, Gerber Accumark, or Optitex allow for digital pattern creation, modification, grading, and marker making (efficient pattern layout for cutting).
4.2 Key Vocabulary Demystified
Understanding pattern making terminology is crucial for clear communication and learning.
Term | Definition |
---|---|
Sloper / Block | A basic, fitted template pattern (without seam allowances or design details) created from specific measurements. Serves as the foundation for developing other patterns. |
Muslin / Toile | A test garment, typically made from inexpensive muslin fabric, sewn from the first pattern draft. Used to check the fit, proportions, and design lines before cutting into final fabric. Essentially, a prototype. |
Dart | A V-shaped fold sewn into fabric to help shape a flat piece of cloth to fit body curves (e.g., bust, waist, hips). |
Dart Manipulation | Techniques used to move or change darts on a pattern (pivoting) or to incorporate dart shaping into seam lines or gathers (slash-and-spread) to create different design styles while maintaining fit. |
Seam Allowance | The area between the stitching line and the raw edge of the fabric on a pattern piece. Must be included on patterns for sewing and varies depending on the seam type and location. |
Pattern Grading | The process of systematically increasing or decreasing the size of a base pattern to create a range of sizes (e.g., Small, Medium, Large) while maintaining the original proportions and fit intent. Essential for sizing. |
Tech Pack | A comprehensive specification document created for manufacturers. Includes technical sketches, measurements, construction details, material specifications, and crucially, the pattern pieces (often digitized) needed for production. |
5. Integrating Pattern Making into Your Apparel Production Workflow
5.1 From Design Sketch to Finished Sample: Where Patterns Fit In
Pattern making is a pivotal step bridging the creative and production phases of your apparel production workflow. The typical sequence looks like this:
- Idea/Concept: The initial inspiration for a garment.
- Design Sketch: Visualizing the garment, often including key details and silhouette.
- Pattern Creation: Drafting or draping the blueprint based on the sketch and required measurements.
- Muslin/Sample Sewing: Creating a test garment (Muslin) from the initial pattern.
- Fitting/Revisions: Assessing the muslin on a form or fit model, identifying necessary adjustments, and making pattern revisions.
- Final Pattern: The corrected, approved pattern ready for production or grading.
- Production: Using the final pattern to cut and sew the finished sample and subsequent production run.
Pattern making transforms the design sketch into a producible reality.
5.2 The Role of Patterns in Manufacturer Communication
Effective manufacturer communication is vital for successful garment manufacturing, especially when outsourcing. Pattern pieces, often digitized and included electronically, are a core component of the Tech Pack. Alongside detailed measurement charts, construction instructions, bill of materials, and other specifications, the patterns provide the manufacturer with the exact shapes and sizes needed to cut the fabric accurately. A comprehensive Tech Pack, featuring precise patterns, minimizes errors and ensures the final product aligns with the design vision.
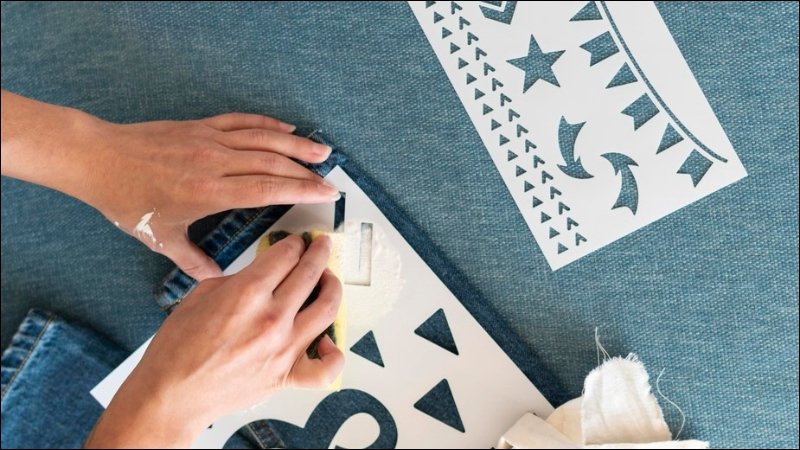
5.3 Testing and Refining: The Importance of Muslins and Pattern Revisions
Pattern making is rarely perfect on the first try; it’s an iterative process. Sewing a muslin (also known as a toile) is a crucial quality control step. This test garment allows you to assess the garment fit, drape, and design lines on a 3D form before committing expensive final fabric.
Fitting the muslin will inevitably reveal areas needing improvement. Making pattern revisions based on these fittings is a normal and necessary part of developing a high-quality, well-fitting garment. Consider muslins an investment in saving time and materials later.
5.4 Considerations for Small Businesses: Learning In-house vs. Outsourcing to a Pattern Maker
For small businesses, deciding whether to develop pattern making skills in-house or outsourcing to a professional pattern maker (either freelance or through a service) involves weighing several factors:
Factor | Learning In-House | Outsourcing to a Professional |
---|---|---|
Time Investment | Significant time required to learn and practice effectively | Frees up founder’s time for other business tasks |
Cost | Lower initial cash outlay, but time is also a cost | Professional fees can be significant, especially initially |
Skill Level | Requires developing technical proficiency, patience | Access to expert skills and experience immediately |
Design Complexity | May be challenging for intricate or non-standard designs | Better suited for complex or tailored garments |
Production Volume | More manageable for very small, hands-on production | Necessary for scaling up production efficiently |
Control | Full creative and technical control | Requires clear communication and trust |
6. Related Questions
6.1 What is the difference between a block/sloper and a final pattern?
A pattern block or sloper is the most basic template derived directly from body measurements. It fits the body closely with minimal ease and has no style lines, design details, or seam allowance. Think of it as the foundational blueprint. A final sewing pattern, derived from the block, incorporates design elements (like collars, pockets, pleats), adds necessary wearing ease (room for movement), includes seam allowances, notches for matching pieces, and all other markings needed for cutting and sewing the specific garment style.
6.2 Is CAD software practical for a small business?
Whether CAD software is practical depends heavily on the small business’s specific needs. For businesses with higher production volumes, complex designs requiring frequent modifications, or those needing precise pattern grading, CAD can significantly increase efficiency and accuracy.
However, there’s a cost associated with the software and hardware, plus a learning curve. For businesses starting out with simpler designs and lower volumes, traditional manual pattern making methods are perfectly viable and more budget-friendly initially.
6.3 How can I find and collaborate effectively with a freelance pattern maker?
Finding a freelance pattern maker can be done through industry-specific platforms (like Sewport), professional networks, fashion incubators, or referrals. Effective collaboration hinges on clear communication. Providing a detailed tech pack or design brief is essential.
This should include accurate sketches or photos, target customer measurements or desired fit, fabric information, and construction details. Regular communication, reviewing muslin samples together (physically or virtually), and understanding their workflow will lead to better results.
6.4 What key information should I provide when briefing a pattern maker?
To ensure your pattern maker understands your vision, provide: detailed technical sketches (front and back, minimum) or clear photographs of a similar garment; the target customer profile and desired fit; key finished garment measurements; the specific type and weight of fabric to be used (as this affects drape and fit); any specific construction preferences or finishing details; and if possible, a reference sample garment that demonstrates the desired fit or details. The more information, the better.
6.5 How does pattern grading ensure consistent fit across sizes?
Pattern grading is the process of creating patterns for a range of sizes from the base size pattern (usually the sample size). It doesn’t simply enlarge or shrink the entire pattern. Instead, grading uses specific mathematical rules and pre-determined increments applied to key points on the pattern pieces (like bust, waist, hip, shoulder points, armhole depth).
These rules are designed to systematically increase or decrease the pattern dimensions while maintaining the original style lines, proportions, and intended consistent fit characteristics across the entire size range.
Read more:
Pattern making is far more than just drawing shapes on paper; it is the essential technical foundation upon which quality apparel is built. Understanding its principles and investing time or resources into creating accurate patterns is non-negotiable for any serious apparel business. Doing so directly impacts consistent fit, reduces errors and waste during production, fosters clear communication with manufacturers, and ultimately builds brand success through reliable, well-fitting garments that earn customer trust.
Prioritizing pattern making from the outset lays the groundwork for a sustainable and reputable clothing brand. Whether you choose to learn the skill yourself or collaborate with an expert, giving pattern making the attention it deserves is crucial. If you require professional assistance developing tech packs and patterns, services like My Pack Love can provide expert support tailored to your needs.