Ensuring consistent product quality can feel overwhelming for a growing apparel business. You worry about inconsistent sizing on labels, packaging that doesn’t hold up, or small flaws that might damage your hard-earned brand reputation and prevent building customer loyalty. Ignoring these details can lead to unexpected costs and customer complaints. This article cuts through the confusion surrounding quality control (QC).
You’ll learn what QC truly involves beyond simple checks, why implementing basic inspection routines against set standards is crucial for your success, and how these practices differ from quality assurance (QA) (the broader system of preventing issues). Most importantly, you’ll gain practical, actionable steps to start implementing essential QC checks throughout your production process today, protecting your brand and saving money in the long run.
1. Defining Quality Control: More Than Just Checking Boxes
1.1 What QC Really Means for Product Quality & Consistency
At its heart, quality control (QC) is the hands-on process of verifying that your products – including labels, tags, and packaging – actually match the standards and specifications you’ve set. Think of it like proofreading an important document before sending it; QC is the systematic inspection and testing designed to catch defects and ensure compliance before an item ships to your customer.
This definition highlights its role in achieving consistent product quality. While QC involves specific actions like checking measurements or print clarity, it’s a crucial component within the broader framework of quality management, focusing directly on the output.
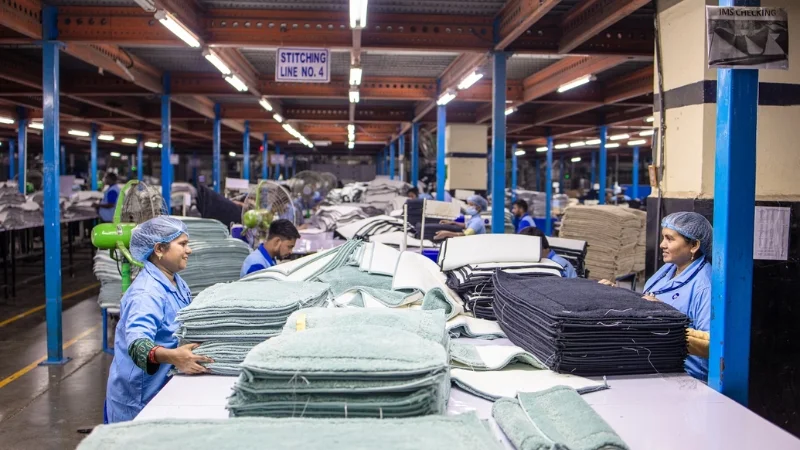
1.2 The Core Purpose: Ensuring Your Standards Are Met Every Time
The fundamental purpose of implementing QC is not just about random spot-checks. It’s about systematically fulfilling quality requirements that your business establishes. These quality requirements, which form your manufacturing standards, dictate what makes a product acceptable. Effective QC aims to ensure every production run meets these standards, thereby reducing unwanted variation between individual items and maintaining consistency. This reliability is what customers come to expect.
2. The Real Cost of Skipping QC: Why Your Small Apparel Business Needs It
2.1 Protecting Your Hard-Earned Brand Reputation from Inconsistency
Imagine a customer receiving a t-shirt they love, only to find the care label instructions misspelled or the size tag completely inaccurate. Even small flaws like these reflect poorly on the entire brand. This inconsistency signals a lack of attention to detail, eroding customer satisfaction and the trust you’ve worked hard to build. Consistent quality, down to the smallest trim, is essential. When customers encounter defects, even minor ones, their perception shifts, making defect acceptance low and negatively impacting your overall brand reputation. QC acts as a crucial guard against these damaging inconsistencies.
2.2 Reducing Financial Losses from Defects, Returns, and Waste
Skipping QC might seem like saving time, but it often leads to significant financial losses. Consider the tangible costs:
- The expense of the defective labels, tags, or bags themselves.
- The cost of producing or ordering replacements.
- Labor costs associated with removing faulty items and attaching new ones.
- Shipping costs for sending replacements or processing returns.
- Potential loss of entire garments if poorly made trims (like a sharp-edged label) damage the fabric.
- The waste generated from discarded materials and products. Implementing basic QC is a direct form of defect prevention, saving you money by catching problems before they escalate into costly defects and returns.
2.3 Building Customer Loyalty Through Reliable, Quality Products
Conversely, consistently delivering reliable products that meet customer expectations is a powerful driver of customer loyalty. When customers receive apparel with accurate labels, durable tags, and secure packaging every time, it reinforces their trust in your brand’s quality.
They are far more likely to purchase again and recommend your business to others. Effective QC isn’t just about preventing negatives; it’s a positive investment in building a loyal customer base that values the reliability and care you put into every detail.
3. Practical QC Checks for Essential Apparel Trims: A Hands-On Approach
3.1 Inspecting Labels (Woven & Printed): Accuracy, Legibility, Feel, Placement
Performing a thorough inspection of your labels is fundamental. Whether dealing with woven labels or printed labels, consistent checks against your quality standards help in early defect identification. Use these testing methods as a guide:
Content Accuracy:
- Is the brand logo rendered correctly?
- Verify all text for spelling accuracy (brand name, size, care instructions, materials).
- Ensure fiber content information is correct and meets legal requirements.
- Check if the Country of Origin (CoO) is present and accurate, if required for your market.
Appearance & Legibility:
- Do the colors precisely match your specifications?
- Is all text sharp, clear, and easily readable (legibility)? Look for blurry or incomplete printing.
- For woven labels: Check for fraying edges or loose threads.
- For printed labels: Examine for cracking, peeling, or ink bleeding, especially after a gentle flex test.
Feel & Texture:
- For labels placed near skin (like neck labels), is the material acceptably soft?
- Does the overall texture match the sample you approved?
Placement (if pre-attached): Confirm the label is attached securely in the correct, specified location on the garment.
3.2 Verifying Hang Tags: Print Quality, Material Stock, Hole Punch, String/Attachment
Hang tags contribute significantly to the perceived value and branding at the point of sale. Referencing your product specification document, follow these inspection procedures:
Print Quality & Content:
- Are colors accurate and consistent with your brand guidelines?
- Is the logo sharp and well-defined?
- Ensure all text is legible, correctly spelled, and free from smudges or misprints.
Material Stock: Does the paper or cardstock material match the specified weight, texture (e.g., smooth, textured), and finish (e.g., matte, gloss)?
Construction & Finishing:
- Is the hole punch clean, correctly sized, and accurately positioned?
- If a string, ribbon, or plastic fastener is used, is it attached securely, neatly, and using the correct type?
- Check for any tears, creases, bends, or surface damage on the tag itself.
3.3 Examining Zipper Bags & Inner Packaging: Seal Strength, Clarity, Correct Sizing
Inner packaging like zipper bags protects garments and presents them professionally. Key inspection points include finished product testing for functionality:
Functionality & Seal Strength:
- Does the zipper or adhesive seal close securely along its entire length? Test the seal strength.
- Can the bag be reopened easily without tearing the plastic (unless designed as tamper-evident)?
Appearance & Clarity:
- Is the plastic material clear (or opaque/colored, if specified) and free from excessive scratches, dirt, or marks that impair clarity?
- If printed, is the branding/information accurate and clear?
Fit & Sizing: Is the bag the correct sizing for the garment it’s intended to hold? The garment should fit comfortably without being crammed or swimming in excess space.
3.4 Testing Poly Mailers & Shipping Supplies: Adhesive Seal, Tear Resistance, Opacity
Your outer shipping supplies, especially poly mailers, are the first line of defense during transit. Robust testing is crucial for effective supply chain management:
Seal & Adhesive:
- Does the protective strip over the adhesive peel off cleanly without tearing?
- Once sealed, does the adhesive create a strong bond? Try to gently pull it open – it should require significant effort or visibly damage the mailer (indicating tamper evidence).
Durability & Tear Resistance:
- Does the mailer material feel appropriately thick and strong for shipping apparel?
- Perform a simple tear resistance test: apply reasonable pulling force at an edge or seam to check for easy tearing.
Opacity: Is the mailer sufficiently opaque to conceal the contents? Hold it up to a bright light with an item inside to check visibility. Proper opacity protects privacy and deters theft.
4. Clearing the Confusion: Quality Control (QC) vs. Quality Assurance (QA)
While often used interchangeably, Quality Control (QC) and Quality Assurance (QA) represent distinct but related approaches to managing quality. Understanding the difference helps in implementing a more effective overall strategy.
4.1 Focused on Finding and Fixing Issues (Product Inspection & Testing)
Quality control (QC) is primarily product-oriented and reactive. Its main function involves inspection and testing activities performed during or after production to identify problems against set specifications. The goal is finding defects in the actual output. If issues are found, corrective actions (like rejecting a batch of labels or reworking faulty stitching) are taken. Think of QC as the final spellcheck performed after a document is written – its purpose is defect identification in the finished product.
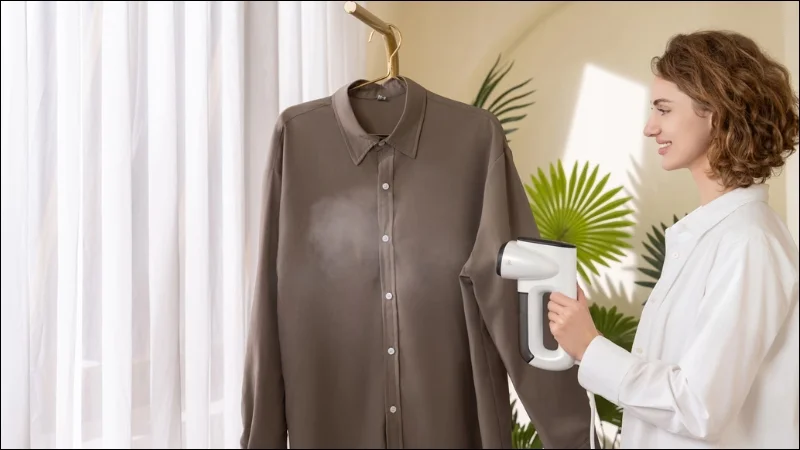
4.2 Focused on Preventing Issues (Process & System Design)
Quality assurance (QA), conversely, is process-oriented and proactive. QA focuses on prevention by designing, implementing, and monitoring the systems and processes used to create the product. This includes activities like establishing standard operating procedures, training staff, vetting suppliers, and implementing process control measures.
The aim is preventing defects from occurring in the first place through robust system design. QA works upstream to build quality into the entire quality management system (QMS). Using the writing analogy, QA is like creating the style guide, templates, and author training before writing begins, aiming to minimize errors from the start.
4.3 How They Work Together: Achieving Overall Quality Management
QC and QA are not opposing forces; they are complementary components of comprehensive quality management. Effective systems use the data gathered during quality control (QC) activities as feedback for quality assurance (QA). For example, if QC repeatedly identifies the same type of printing defect on hang tags (defect identification), this information signals a potential weakness in the QA system.
QA would then investigate the root cause (e.g., supplier issue, faulty equipment, inadequate specification) and implement changes for process improvement, ultimately reducing future defects. They work in a continuous loop to maintain and enhance overall product quality.
5. Implementing Basic QC: Actionable First Steps for Small Businesses
Getting started with Quality Control doesn’t require complex systems or significant investment. Focusing on clear communication and simple checks can make a substantial difference.
5.1 Setting Clear, Achievable Quality Standards for Your Products & Trims
Begin by defining what “acceptable quality” means for your most critical trims. Don’t try to create exhaustive rules for everything at once; focus on what matters most to your brand and customers. Establish clear, measurable, and achievable quality standards.
For example, your initial specifications might include:
- Woven labels: “Maximum 1 loose thread per 50 labels. Color must match approved Pantone swatch within +/- 1 shade variance (tolerance).”
- Hang Tags: “No visible print smudges or spelling errors. Paper stock must match the approved sample weight. Hole punch must be centered +/- 1mm.”
- Poly mailers: “Adhesive must create a seal that requires tearing the mailer to open. Opacity must prevent text visibility under normal light.”
Document these simple quality benchmarks, ideally including reference photos showing examples of ‘acceptable’ versus ‘unacceptable’ for visual clarity. These documented specifications become your baseline.
5.2 Using Simple Checklists & Visual Guides for Consistent Inspections
Once standards are set, create straightforward checklists based on them for each type of trim. These tools guide the inspection procedures and ensure consistency, regardless of who performs the check.
- Use a simple format, like tick boxes (Pass/Fail/Not Applicable).
- Incorporate visual guides (like the standard sheet photos mentioned above) directly into or alongside the checklists for quick reference.
- Keep language clear and direct.
This structured approach helps standardize the inspection process and provides a basis for basic employee training on QC tasks.
Check Point | Specification / Standard | Pass | Fail | Notes |
---|---|---|---|---|
Print Clarity | All text readable, no smudging or blurring | ☐ | ☐ | |
Color Match | Matches approved brand color swatch (within tolerance) | ☐ | ☐ | |
Content Accuracy | Spelling, logo, info matches specification sheet | ☐ | ☐ | |
Material Stock | Correct paper weight and finish (e.g., matte) | ☐ | ☐ | |
Hole Punch | Cleanly punched, centered +/- 1mm, correct size | ☐ | ☐ | |
String/Attachment | Securely attached, correct type, neat | ☐ | ☐ | |
Overall Condition | No tears, creases, or significant marks | ☐ | ☐ |
5.3 Communicating Expectations & Findings Clearly with Suppliers
Effective quality control relies heavily on clear communication with your suppliers. Good supplier management is a partnership built on shared understanding.
Share expectations upfront: Provide your documented quality standards and specifications (including visual guides if possible) before placing an order. Ensure the supplier acknowledges and agrees to them.
Establish a feedback loop: Define a clear process for reporting any defects found during your QC checks. This should include:
- Who to contact at the supplier company.
- How to report (e.g., email is usually best for documentation).
- What information to include (order number, item description, quantity affected, clear description of the defect, photographic evidence).
- A reasonable timeframe for reporting issues after receiving the goods (e.g., within 7-10 business days).
Maintain records: Keep track of all quality-related communication with suppliers, including shared standards, reports of defects, and agreed-upon resolutions. Maintaining records is crucial for tracking supplier performance and resolving disputes.
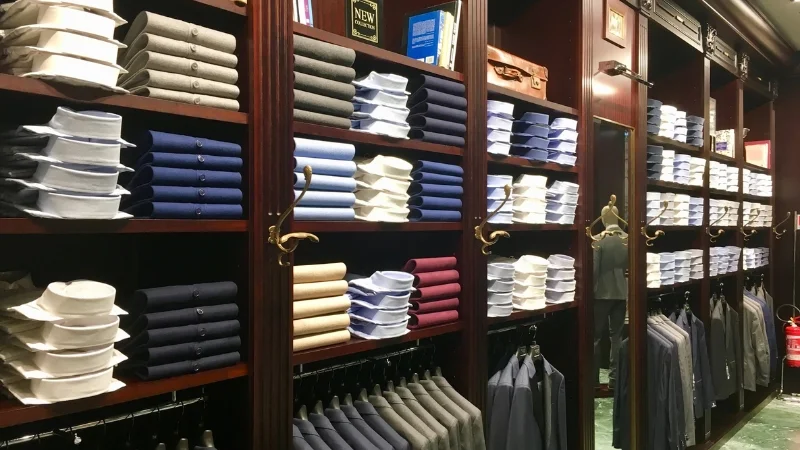
6. Related Questions
6.1 How much does implementing basic QC cost a small apparel business?
For a small business, the primary initial cost of implementing basic quality control is often measured in time rather than direct financial outlay. Setting up simple checklists and performing visual inspections on incoming trims requires dedicating staff time, but usually involves minimal expenditure on tools or equipment. This time commitment should be viewed as an investment.
When compared to the potential costs of not doing QC – dealing with customer returns, remaking faulty products, wasted materials, and damage to your brand reputation – the time spent on basic checks offers a significant return on investment (ROI). Preventing even a small percentage of defects can save substantial money and resources down the line.
6.2 What’s the difference between checking every item (100% inspection) and checking a few (sampling)?
The main difference lies in the scope of the inspection. 100% inspection method means examining every single unit in a batch. This is the most thorough approach, offering the highest chance of catching all defects, but it is also the most time-consuming and costly, especially for large quantities.
Sampling, on the other hand, involves inspecting only a predetermined portion or random selection of items from a batch. This method is faster and less expensive but carries a higher risk that some defects might be missed if they happen to fall only in the uninspected portion. The choice often depends on the criticality of the item and the acceptable risk level; 100% inspection might be used for high-value components or critical compliance details, while sampling may suffice for large batches of less critical items where minor defect rates are tolerable.
Discovering defects in a delivery from a supplier requires a methodical approach. First, meticulously document the issues found during your QC checks – take clear photos, note the specific problems, and quantify the number of affected items. Next, review your purchase order or agreement with the supplier regarding quality standards and procedures for handling non-conforming goods.
Armed with this evidence and understanding, contact your supplier promptly and professionally. Clearly explain the defects using your documentation (including photos). Discuss potential solutions based on your agreement and the severity of the issue; options might include returning the entire batch for a refund or replacement, accepting the batch at a discount, or having the supplier rework the defective items. Whatever the resolution, ensure it’s documented as a corrective action for future reference. Clear communication and thorough records are key.
6.4 Can I use the same QC checks for different types of clothing trims?
While the fundamental principles of quality control – verifying accuracy, checking against specifications, looking for defects – apply broadly across all clothing trims, the specific QC checks and criteria must be adapted for each item type. You wouldn’t test the adhesive strength on a woven label, nor would you primarily check the softness of a poly mailer.
Therefore, while a general framework for inspection might be similar (e.g., checking quantity, visual appearance, content accuracy), the detailed checklist points require specificity. You need distinct checks tailored to the unique function and material of labels, tags, bags, mailers, etc. Effective QC requires this level of adaptation to ensure all relevant quality aspects for each specific trim are evaluated appropriately.
Read more:
Integrating quality control into your operations is not merely an optional add-on; it’s a fundamental practice crucial for the health and growth of your apparel business. As we’ve explored, consistent QC safeguards your hard-earned brand trust, minimizes financial losses from defects and returns, and fosters customer satisfaction and loyalty through reliable product quality.
For small business owners, implementing QC doesn’t need to be overly complex or expensive. Starting with clear standards, simple checklists, and focused inspections for essential trims like labels, tags, and packaging provides a solid foundation. These actions represent a vital investment in consistency and long-term success. By prioritizing quality checks, you ensure every piece you send out reflects the care and standard your customers expect, strengthening your brand one stitch at a time.