In the world of fashion design, creating the perfect fit and silhouette hinges on the pattern. Two fundamental methods dominate this process: draping, a three-dimensional technique working directly with fabric on a form, and flat pattern making, a two-dimensional approach using drafting and measurements on paper.
While both aim to produce functional patterns, their approaches, creative possibilities, and technical demands differ significantly. This comparison explores the core differences between 3D draping and 2D flat pattern making, highlighting when and why designers utilize each distinct method.
1. Understanding the Fundamentals: Draping vs. Flat Pattern Making
1.1 Defining Draping: The Art of Three-Dimensional Design on a Dress Form
Draping is one of the fundamental fashion design techniques involving the direct manipulation and positioning of fabric onto a dress form or mannequin. This process allows a designer to sculpt material directly in three-dimensional space, establishing the garment’s structure, fit, and aesthetic lines through hands-on textile manipulation.
Unlike methods that begin on paper, draping is often more intuitive, relying on the feel and behavior of the fabric as it is pinned, folded, and shaped around the form to bring a design idea to life organically.
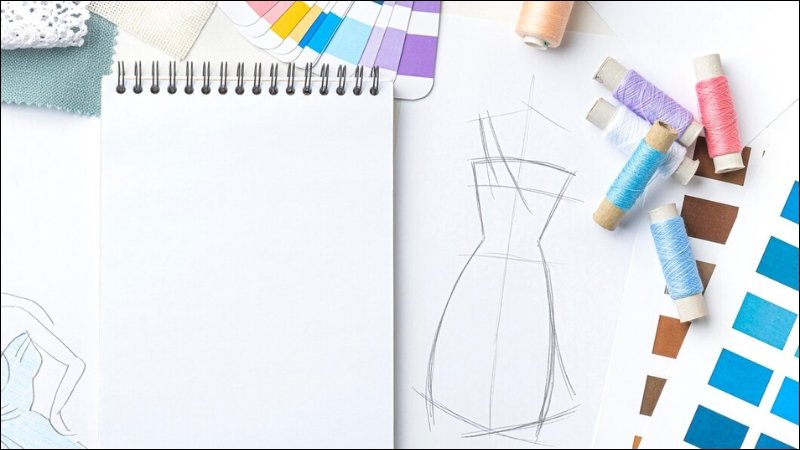
1.2 Key Differences from Flat Pattern Making
While draping starts in 3D, flat pattern making (also known as pattern drafting or increasingly, digital pattern creation) begins in two dimensions. Here’s a breakdown of the core distinctions:
- Starting Point: Draping commences with fabric on a three-dimensional form, allowing immediate visualization of shape and flow. Flat pattern making starts with precise measurements translated into lines and curves on flat paper or using computer-aided design (CAD) software.
- Methodology: Draping often involves an intuitive, sculptural approach, responding directly to how the fabric behaves. Flat pattern making relies on calculated geometry, formulas, and established tailoring principles to construct the pattern pieces.
- Visualization: With draping, the designer sees the potential garment take shape in real-time on the form. Flat pattern making requires creating a sample garment (a toile or muslin) from the 2D pattern to assess the fit and design in 3D.
- Typical Applications: Draping excels in creating complex, unique, or fluid shapes, flowing gowns, or designs with intricate details that are difficult to conceptualize flat. Flat pattern making is highly efficient for creating foundational blocks, standardized fits, tailored garments, and designs based on precise specifications.
1.3 Why Both Methods Have Value in Modern Garment Construction
In contemporary apparel design process, draping and flat pattern making are not rivals but complementary garment construction methods. Many successful designers and brands utilize both techniques, often within the development of a single garment. For instance, a designer might use flat pattern making for the basic structure of a jacket but employ draping to develop a complex collar or sleeve detail.
Alternatively, an initial design concept might be explored through draping, and once finalized, the draped muslin is then used to create a precise flat sewing pattern for production. Understanding the principles behind both methods provides designers and clothing business owners with greater versatility, problem-solving ability, and a deeper comprehension of how fabric transforms into form.
2. Why Understanding Draping is Valuable for Your Clothing Business
2.1 Improving Garment Fit and Quality Control
Gaining a foundational knowledge of draping principles significantly enhances fit understanding for clothing businesses. When evaluating samples, instead of simply noting that a garment doesn’t fit correctly, you can begin to understand why. Recognizing how darts create shape, how seams curve around body measurements, or how ease is distributed helps pinpoint the root cause of fit issues.
For example, seeing fabric pull awkwardly across the bust might suggest an incorrectly placed or sized dart, while tightness across the hips could indicate insufficient ease was draped into the side seams. This deeper insight into achieving fit accuracy allows for more effective quality control, potentially reducing costly returns and improving overall customer satisfaction with the final fit.
2.2 Enhancing Communication with Manufacturers and Pattern Makers
A grasp of three-dimensional form and how fabric behaves on the body transforms communication within the fashion industry. When providing feedback to apparel manufacturing partners or technical designers, vague comments like “make this looser” become less effective.
Understanding draping allows for more precise instructions, such as “the pattern needs more ease draped over the high hip curve” or “the shoulder seam angle needs adjustment to sit correctly on the form.” This clarity reduces ambiguity, minimizes misunderstandings, and often shortens the sample development timeline, fostering better collaboration and efficiency.
2.3 Unlocking Creative Potential for Unique Silhouettes and Designs
Draping is inherently a creative process that encourages design experimentation directly with fabric. This hands-on, intuitive design process can lead to the discovery of unique shapes, volumes, and silhouette creation possibilities that might not readily emerge from two-dimensional sketching or flat pattern drafting alone.
Observing how different fabric behavior manifests—the way a stiff textile holds a fold versus how a soft one cascades—can inspire organic form development and innovative design details. For businesses looking to differentiate their brand, incorporating elements derived from draping can lead to signature pieces and explore unconventional aesthetics.
2.4 Accurately Assessing Fabric Behavior Before Committing to Bulk
One of the most practical benefits of understanding draping, even at a basic level, is the ability to better predict fabric properties in a three-dimensional context. A flat fabric swatch only tells part of the story. By performing simple drapes, even with small pieces of potential materials, you gain invaluable insight into the actual drape characteristics – how the fabric hangs, folds, stretches, and reacts to gravity.
This practical application of textile science helps assess if a chosen material truly suits the intended design for a garment before investing in large quantities, preventing costly mistakes where a fabric doesn’t perform as expected once constructed.
3. The Essential Draping Tools and Materials
Having the right tools is fundamental to successful draping. Here’s a rundown of the essentials:
3.1 The Dress Form: Your 3D Canvas
- Purpose: The dress form or mannequin serves as the foundation for draping, mimicking the human body shape.
- Selection: Choose a form that closely matches your brand’s core sample size or target customer measurements. Options include adjustable forms (offering flexibility across a small range of sizes) and professional fixed-size forms (often preferred for industry accuracy). Ensure the form has key anatomical landmarks indicated or allows for easy marking of these points.
3.2 Fabric: Starting with Muslin
- Purpose: Muslin fabric (often called calico) is the standard textile for draping due to its plain weave (which clearly shows markings), affordability, and availability in various weights.
- Usage: Use a muslin weight that approximates the drape and feel of your final garment fabric. For initial exploration or very fluid designs where specific drape is key, sometimes a different inexpensive fabric with similar characteristics might be substituted if it better mimics the final material’s behavior.
3.3 Pinning Essentials: Securing the Fabric
- Purpose: High-quality pins are crucial for holding the fabric securely to the dress form and shaping details like darts and pleats.
- Selection: Sharp, fine straight pins designed for dressmaking are essential to avoid snagging the muslin. Some designers prefer pins with small heads for easier handling during the manipulation process.
3.4 Measuring & Marking Tools: Precision in 3D
Purpose: Accurate measurements and clear markings are vital for transferring the draped design into a flat pattern.
Tools:
- Flexible measuring tape: For measuring curves and lengths on the form and fabric.
- Rulers: Straight rulers, L-squares (for right angles), and French curves (for shaping armholes, necklines, etc.).
- Marking tools: Tailor’s chalk or disappearing fabric markers are used to draw seam lines, dart points, and other design details directly onto the muslin while it’s on the form.
3.5 Cutting Tools: Clean Edges
- Purpose: Needed for cutting the muslin pieces initially and trimming excess fabric during the draping process.
- Tools: Sharp fabric scissors are essential for precise cuts. Shears can be helpful for cutting larger fabric sections efficiently.
3.6 Optional but Helpful Tools for Efficiency
Purpose: These tools can streamline the draping and pattern creation process.
Examples:
- Style Tape: Narrow tape (often red or black) used to define style lines directly on the dress form before draping begins.
- Notcher: A tool that creates small notches in the pattern edge, used for aligning seams accurately during sewing.
- Tracing Wheel and paper: Used to transfer markings from the muslin to pattern paper.
- French Curve Ruler: Essential for refining curved lines like armholes and necklines during the ‘truing’ stage.
4. The Draping Process Demystified: A Step-by-Step Overview
Draping is a skill refined through practice, but understanding the fundamental steps provides a clear roadmap. This overview outlines the typical workflow, from preparing your materials to testing the initial pattern.
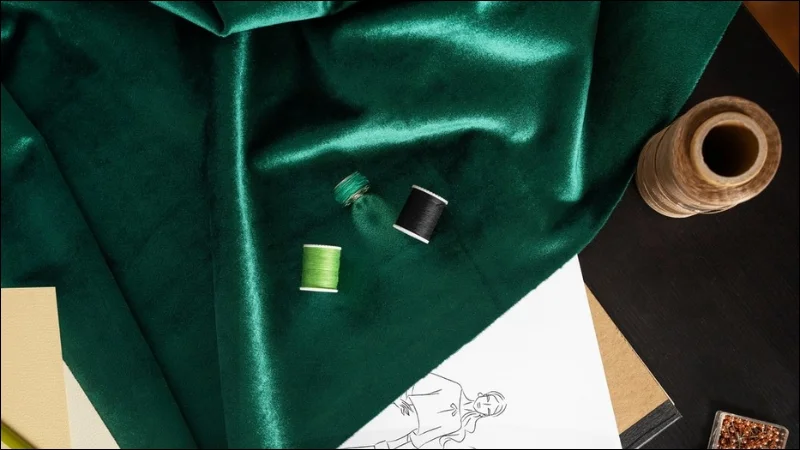
4.1 Step 1: Preparing the Dress Form and Fabric
Accurate preparation is the bedrock of successful draping. Begin by ensuring your dress form is set to the correct measurements if adjustable, or clearly mark essential horizontal and vertical reference lines (like center front, center back, bust, waist, hip) if using a fixed form. Next, prepare your muslin fabric. Cut or tear pieces slightly larger than the section you intend to drape (e.g., front bodice, back skirt).
Proper pressing is crucial to remove wrinkles. Most importantly, accurately mark the lengthwise grain line (parallel to the fabric’s selvage edge) and the cross-grain (perpendicular to the grain line) on each muslin piece. Maintaining these grain lines during draping is essential for the garment’s final hang and fit.
4.2 Step 2: Pinning and Shaping the Fabric
This is the core fabric manipulation stage. Anchor your prepared muslin piece onto the dress form, typically starting at a key point like the center front neckline or shoulder, ensuring the marked grain line aligns correctly with the form’s vertical axis. Smooth the fabric over the form’s contours, pinning it strategically to create the desired shape.
Use pins to form darts, tucks, or gathers where needed to absorb excess fabric and contour the bodice or skirt section to the form’s curves. Work methodically, section by section, gently guiding and easing the fabric without forcing or stretching it unnaturally.
4.3 Step 3: Marking the Key Lines
Once a section is draped satisfactorily and securely pinned, the next critical step is marking. While the muslin is still perfectly positioned on the dress form, carefully mark all necessary lines using your chosen tool (chalk or fabric marker).
This includes the intended seam line locations (where pieces will join), the precise points and legs of darts, any style lines or design elements (like yokes or princess seams), and reference points like the waistline or apex. Consistent and clear marking at this stage is vital for accuracy when transferring the drape to a flat pattern.
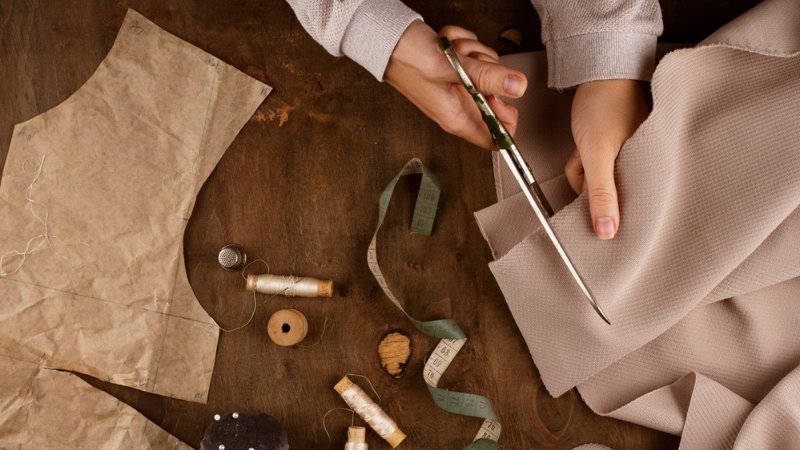
4.4 Step 4: Removing and Truing the Muslin
Carefully unpin the marked muslin section from the dress form and lay it flat on your work surface. The lines marked on the form will likely appear somewhat uneven or sketchy. The “truing” process involves using rulers and design curves (like French curves) to refine these markings into smooth, precise lines.
Straighten seam lines that should be straight, perfect the curves of necklines and armholes, ensure dart legs meet at the correct points, and check that connecting points align properly. This step ensures technical accuracy and smooth transitions between pattern pieces. Smoothing lines correctly is essential for a professional finish.
4.5 Step 5: Adding Seam Allowances and Creating the Paper Pattern
After truing, the marked lines represent the stitching lines (where the seams will be sewn). Before the piece can become a usable sewing pattern, seam allowances must be added. Decide on the appropriate seam allowance width (common standards exist, but can vary) and carefully draw this allowance parallel to all the trued seam lines.
Also, transfer all internal markings, grain lines, dart details, and add notches (small marks on the seam allowance used to align pieces during sewing). Finally, perform the pattern transfer of this completed muslin piece, including all markings and seam allowances, onto sturdy pattern paper to create the final sewing pattern component.
4.6 Step 6: Testing the Fit
Before cutting into your final, often expensive, fabric, it’s essential to test the pattern. Pin or sew your drafted muslin pattern pieces together to create a test garment assembly, often called a toile or muslin sample. Place this sample onto the dress form or, ideally, have a fit model wear it.
Carefully assess the overall fit accuracy, balance, proportion, and how the design lines fall on the three-dimensional form. Check for any pulling, tightness, excess fabric, or awkwardness. Make any necessary adjustments directly on the muslin sample, then transfer these corrections back to your paper pattern before proceeding to the final garment.
5. Key Considerations for Successful Draping Outcomes
Achieving professional results in draping involves more than just following the steps; several key considerations significantly impact the final outcome. Paying attention to these details enhances accuracy and ensures the draped form translates effectively into a well-fitting garment.
5.1 Choosing the Right Muslin Weight or Substitute Fabric
The choice of muslin or draping fabric is paramount because its behavior directly influences the draped result. Using a fabric weight and drape characteristic similar to your final intended fabric is crucial. For instance, draping a pattern intended for a lightweight, fluid chiffon using a heavy, stiff muslin will yield an inaccurate representation of how the final garment will hang and move.
Conversely, using very lightweight muslin for a structured wool coat pattern won’t capture the necessary body and form. Assess the intended fabric characteristics and select a muslin or inexpensive substitute that mimics its weight, stiffness, or fluidity as closely as possible.
5.2 Working Symmetrically vs. Asymmetrically
Efficiency is key in pattern development. For garments designed to be symmetrical (the same on the left and right sides), the standard practice is to drape only one half of the garment, typically the right side as worn, on the dress form. Once this half is draped, marked, trued, and transferred to paper, the pattern piece is simply flipped or mirrored to create the pattern for the opposite side.
However, for asymmetrical designs where the left and right sides differ intentionally, it becomes necessary to drape both sides of the garment fully on the form to capture the unique details and fit of each side accurately.
5.3 The Critical Importance of Grain Lines
Understanding and respecting fabric structure, specifically the grain line, is non-negotiable in draping for quality results. The lengthwise grain (warp) runs parallel to the selvage and typically has the least stretch, providing stability. The crosswise grain (weft) runs perpendicular to the selvage and usually has slightly more give.
The bias cut (fabric manipulated at a 45-degree angle to the lengthwise and crosswise grains) offers the most stretch and fluidity, allowing fabric to cling and drape softly around curves. Maintaining the correct grain alignment (e.g., center front usually on the straight lengthwise grain) during draping is essential for ensuring the finished garment hangs correctly, fits properly, and avoids twisting or distortion.
5.4 Patience and Practice: Embracing the Hands-on Nature
Draping is fundamentally a hands-on approach to design; it’s a tactile skill that develops with experience. It requires patience and a willingness to engage in trial-and-error. Initial attempts may not be perfect, and manipulating fabric smoothly onto the form takes practice.
Don’t be discouraged if early drapes require adjustments or even starting over. View each attempt as part of a valuable learning process. Developing a feel for how different fabrics behave and how to translate a 2D idea into a 3D form requires time and persistent effort.
6. Related Questions
6.1 Is draping harder than flat pattern making?
Whether draping is “harder” than flat pattern making is largely subjective and depends on an individual’s strengths and learning style. Draping heavily relies on spatial reasoning, a tactile understanding of fabric behavior, and the ability to visualize form in three dimensions directly on a dress form.
Flat pattern making, conversely, demands more precision, mathematical calculation, and adherence to specific drafting rules and measurements on a two-dimensional plane. Some individuals find the intuitive, hands-on nature of draping more accessible, while others prefer the structured, logical approach of flat pattern making. Both techniques require significant practice, patience, and attention to detail to achieve mastery.
6.2 Do I need draping if I only make simple garments like t-shirts?
While you likely wouldn’t need to perform active draping for every simple t-shirt design (as basic blocks for such garments are often efficiently created using flat pattern methods), understanding the principles learned from draping remains beneficial.
Knowledge of how fabric behaves in three dimensions helps immensely when evaluating the fit even in simple items. Understanding concepts like shoulder slope, armhole curves, ease distribution, and how grainlines affect hang provides a more critical eye for assessing samples and ensuring comfort and a good silhouette, even for basic t-shirts or tanks.
6.3 Can I learn draping online or do I need a class?
It is possible to learn draping through various methods, each with pros and cons. Online tutorials, videos, and courses offer great accessibility, allowing you to learn at your own pace and benefit from visual demonstrations. However, draping is a very hands-on skill where subtle fabric manipulations make a big difference.
An in-person fashion class provides the invaluable benefit of immediate, personalized feedback from an instructor who can correct technique, guide fabric handling, and answer questions in real-time. Many find a combination approach effective: using online resources for foundational knowledge and visual examples, supplemented by in-person workshops or classes for refining technique and receiving expert critique.
6.4 What’s the minimum investment needed to start experimenting with draping?
Starting with draping doesn’t necessarily require a huge upfront investment. The absolute essentials include a dress form reasonably close to your desired size (second-hand or basic adjustable models can work initially), inexpensive muslin fabric to practice with, a good supply of sharp dressmaker pins, a flexible measuring tape, and basic marking tools like tailor’s chalk or a washable fabric marker.
While specialized rulers and other draping tools are helpful for refinement, you can begin experimenting and learning the fundamentals with just these core items, making it accessible to start small.
Read more:
Incorporating an understanding of draping into your clothing business workflow offers significant advantages. Grasping how fabric interacts with the three-dimensional form translates directly into practical benefits: a more discerning eye for evaluating sample fit, clearer communication with manufacturing partners regarding quality adjustments, enhanced capacity for innovative design exploration, and more informed decisions about fabric behavior before committing to production.
Even foundational knowledge about manipulating fabric in 3D empowers small businesses to elevate their product development process. While mastering draping takes practice, continuously applying these principles fosters a deeper understanding of garment construction. For particularly complex design challenges or taking your pattern development to the next level, collaborating with experienced pattern makers or fit consultants who specialize in draping can be a strategic investment in your brand’s success and quality.