Iron-on patches offer a fantastic avenue for apparel customization and branding, adding unique flair to garments. However, achieving a professional, lasting finish requires the right tools. While a household iron might seem convenient, its limitations—uneven heat distribution, inconsistent pressure, slower application time, and increased risk of damaging both patch and garment—make it unsuitable for business purposes where quality and reputation are paramount.
This is where a dedicated heat press machine becomes essential. Utilizing a heat press ensures consistent temperature and pressure across the entire patch surface, leading to superior adhesive bond strength and increased durability. This translates to greater efficiency in production and, critically, higher perceived quality for your customized apparel.
Investing in the proper equipment elevates your apparel customization process, safeguarding your branding efforts and ensuring customer satisfaction. This guide will walk you through selecting the right settings, the precise application process, and troubleshooting common issues to help you master the use of a heat press for iron-on patches.
1. Essential prep work: Setting the stage for flawless adhesion
Thorough preparation is foundational to achieving a professional and durable patch application; neglecting these initial steps often leads to inconsistent results or damage to materials.
1.1 Gathering your tools & materials for garment decoration
Having the right equipment ready streamlines the garment decoration process and prevents errors mid-application. Ensure you have the following:
- Heat press machine: The core tool providing controlled heat and pressure.
- Iron-on patches: Your chosen designs with heat-activated adhesive backing.
- Garment/fabric item: The clothing or accessory receiving the patch.
- Protective sheet (e.g., Teflon sheet, parchment paper): Essential to protect both the patch and the garment from direct heat, prevent sticking to the heat platen (the heated upper surface of the press), and avoid shine on certain fabrics.
- Heat resistant tape: Useful for securing the patch in the exact desired position on the garment, preventing shifting during the pressing process.
- (Optional) Pressure pillow (heat press pillow): A foam-filled, heat-resistant pad placed inside the garment or under the application area. Beneficial for ensuring even pressure when pressing over seams, zippers, buttons, or thick fabric areas that create an uneven surface.
1.2 Understanding your fabric & patch combination is key
Before applying any heat, always consult the garment care labels. These labels provide crucial information about the fabric types used and their max heat tolerance. Different fabrics react differently to heat; for instance, cotton generally withstands higher temperatures compared to heat-sensitive fabrics like polyester or blends, which can scorch, melt, or discolor easily.
Additionally, while many iron-on patches use similar heat-activated adhesive, variations in patch adhesive formulation might necessitate slight adjustments to the recommended temperature settings or press time. Treating this step as non-negotiable is key to preventing costly mistakes and ruined inventory.
1.3 Preparing the garment and workspace for efficiency
For the adhesive to bond correctly, the application area on the garment must be clean and completely wrinkle-free. Smooth out the fabric on the lower platen (the base surface) of the heat press.
Perform a quick pre-pressing step: close the heat press onto the application area for 2-5 seconds using the intended temperature. This serves two critical functions: removing residual moisture trapped in the fabric (which can interfere with adhesion) and creating a perfectly smooth, flat surface for the patch.
Ensure your workspace is safe and conducive to efficient work. The heat press should be placed on a sturdy, stable surface with adequate ventilation, especially when working for extended periods.
2. Dialing it in: Optimal heat press settings for reliable patch bonding
Achieving a durable and professional finish hinges on correctly configuring your heat press; this section delves into the critical settings required for successful patch application.
2.1 The core trio: Temperature, pressure, and time
The successful application of an iron-on patch relies on the precise interplay of three key elements: temperature, pressure, and time. Temperature is required to activate the heat-activated adhesive on the back of the patch, melting the glue so that bonding can occur.
Pressure ensures firm, even contact between the melted adhesive and the fabric fibers, forcing the adhesive into the weave for a stronger hold. Time dictates how long the heat and pressure are applied, allowing the chemical and physical bonding process to complete effectively.
These three factors are interdependent; adjusting one often necessitates tweaking another. Insufficient heat, pressure, or time can lead to poor adhesion and application failure, while excessive amounts can damage the patch or the garment fabric. Finding the right balance is crucial for consistent, high-quality results.
2.2 Recommended starting point settings guide
Disclaimer: The following table provides general starting points based on common materials. These are not definitive settings. Always refer to the specific recommendations provided by your patch manufacturer and garment supplier. Thorough testing on scrap material or an inconspicuous area is absolutely essential before proceeding with production runs.
Patch type | Fabric type | Temp range (°F / °C) | Pressure level | Time duration (sec) | Notes |
---|---|---|---|---|---|
Embroidered | Cotton | 330-350°F / 165-177°C | Medium to firm (4-6 bar) | 15-25 seconds | Use protective sheet (Teflon), cool peel |
Embroidered | Polyester | 270-300°F / 132-149°C | Medium (3-5 bar) | 10-20 seconds | Use protective sheet, test for scorching |
Embroidered | Cotton/poly blend | 300-330°F / 149-165°C | Medium (4-5 bar) | 12-22 seconds | Use protective sheet, start lower temp |
Woven | Cotton | 320-340°F / 160-171°C | Medium (4-5 bar) | 12-20 seconds | Use protective sheet, cool peel |
Woven | Polyester | 270-290°F / 132-143°C | Light to medium (3-4 bar) | 10-18 seconds | Use protective sheet, high risk scorching |
Woven | Cotton/poly blend | 290-320°F / 143-160°C | Medium (3-5 bar) | 10-20 seconds | Use protective sheet, test carefully |
Disclaimer: Remember, these heat press settings are guidelines only. Variations in patch adhesive, fabric density/finish, and heat press calibration necessitate testing. Always prioritize manufacturer instructions and conduct your own tests to determine the optimal temperature range, pressure level, and time duration for your specific patch type and fabric type combination.
2.3 The non-negotiable step: Testing your settings
From a business perspective, testing your heat press settings before committing to a batch of garments is non-negotiable. This crucial step acts as your primary quality control measure, helping you avoid ruined inventory, costly reprints, and potential damage to your brand’s reputation.
Always perform a test application first, ideally on a piece of scrap fabric identical to your final product, or at minimum, on a hidden area of the garment (like an inside seam or hem).
After pressing and allowing the patch to cool completely (following cool peel instructions), meticulously check the adhesion. Try to lift the edges of the patch gently with a fingernail. A successful bond means the edges are firmly secured with no lifting.
Also, inspect the fabric around the patch for any signs of scorching, discoloration, shining, or melting, particularly on heat-sensitive materials. If the patch isn’t sticking securely or if there’s fabric damage, you need to adjust your settings.
Critically, only adjust *one variable at a time* – either temperature, pressure, or time – by a small increment and test again. This iterative process allows you to pinpoint the exact cause of the issue and dial in the perfect settings for your specific combination of patch, fabric, and equipment.
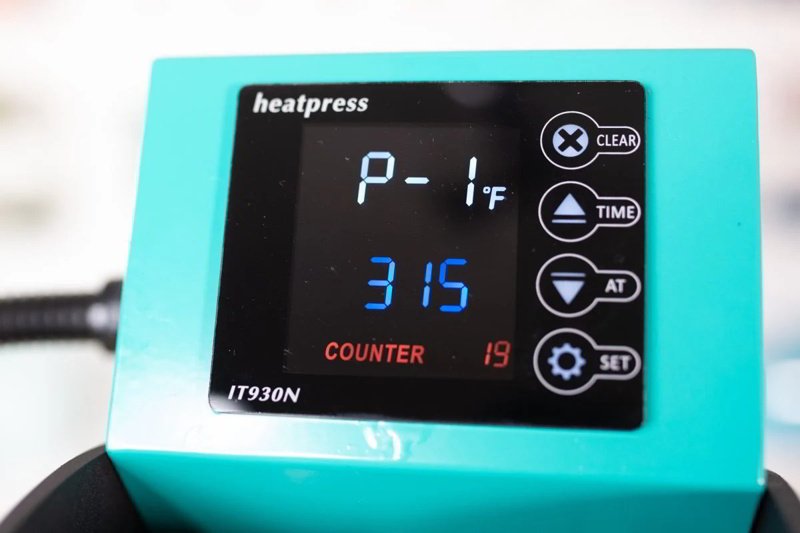
3. The application process: Step-by-step heat pressing for consistent results
Following a consistent, methodical process is key to achieving repeatable, high-quality results when applying iron-on patches with a heat press.
- Power on and set parameters: Turn on your heat press and allow it to reach the predetermined optimal temperature and pressure settings identified during your testing phase. Double-check these settings before proceeding.
- Prepare the garment: Lay the garment flat and smooth on the lower platen of the heat press, ensuring the application area is free of wrinkles or seams directly underneath where the patch will sit (use a pressure pillow if needed). Perform a quick pre-press (2-5 seconds) to remove moisture and create a flat surface.
- Position the patch: Carefully place the iron-on patch onto the garment in the desired location, ensuring the adhesive side is facing down against the fabric.
- Secure the patch (optional but recommended): Use small pieces of heat-resistant tape applied to the *edges* of the patch (avoiding taping over the main body if possible) to hold the patch securely in place and prevent shifting when closing the press.
- Apply protection: Cover the patch and surrounding garment area with a protective Teflon sheet or parchment paper. This prevents direct contact with the heat platen, protects both patch and garment, and avoids adhesive residue transfer.
- Engage the press: Carefully lower the heated upper platen and lock the heat press down, applying the set pressure. Ensure the handle is fully engaged according to the press’s instructions for the desired pressure level.
- Start the timer: Begin the press cycle timer immediately upon locking the press. Adhere strictly to the time determined during your testing.
- Release the press: Once the timer reaches zero, carefully open the heat press, lifting the upper platen away from the garment.
- Remove protective sheet: Gently remove the protective Teflon sheet.
- Crucial cooling phase: This step is critical for bond strength. Allow the garment and patch to cool down *completely* on a flat surface before handling or attempting to check adhesion. Most standard iron-on patch adhesives require a cool peel process, meaning the adhesive fully sets and bonds as it cools. Attempting to peel or check the patch while still warm (hot peel) can disrupt the bond formation, leading to poor adhesion check results or application failure. Unless specifically instructed otherwise by the patch manufacturer for a hot peel product, always let it cool fully (often several minutes). This cooling process solidifies the adhesive’s grip on the fabric fibers, ensuring maximum durability.
- Adhesion check: Once completely cool, gently try to lift the edges of the patch with a fingernail. The patch should be firmly adhered all around with no lifting corners or edges.
- Re-press if necessary: If edges are lifting after cooling, cover again with the protective sheet and re-press for an additional 5-10 seconds. Ensure pressure is adequate and allow to cool fully again before re-checking. Avoid excessive re-pressing, which can damage the fabric or patch.
4. Troubleshooting common heat press patch issues: Expert solutions
Even with careful preparation, occasional issues can arise during heat press application. Understanding the common problems and their solutions can save time, materials, and frustration.
4.1 Patch not sticking or peeling at edges
This is one of the most frequent challenges, indicating incomplete adhesion.
Causes:
- Insufficient heat: The adhesive didn’t reach the required activation temperature.
- Inadequate pressure: Not enough force was applied to push the adhesive into the fabric fibers.
- Press time too short: The bonding process was interrupted before completion.
- Uneven pressure: Obstructions like seams, buttons, or zippers prevented consistent contact across the patch surface.
- Incorrect cooling process: Handling the patch or garment before the adhesive fully set (especially for cool peel types).
- Old or faulty adhesive on the patch itself.
- Incorrect heat press settings for the specific fabric/patch combination.
Solutions:
- Verify and increase heat settings slightly (re-test first).
- Increase pressure setting on the heat press.
- Increase press time by a few seconds (re-test).
- Use a pressure pillow inside the garment to create an even surface over obstructions.
- Ensure the garment lies completely flat on the platen.
- Strictly adhere to the recommended cooling procedure (usually cool peel) before checking adhesion.
- If issues persist across multiple patches from the same batch, consult the patch supplier regarding potential adhesive issues.
- Revisit your testing process to confirm the correct settings.
4.2 Fabric scorching, shining, or discoloration
These signs indicate fabric damage due to excessive heat or improper protection.
Causes:
- Temperature too high for the specific fabric type.
- Press time too long.
- Direct contact between the heat platen and the fabric (not using a protective sheet).
- Incorrect settings for delicate or synthetic fabrics.
Solutions:
- Reduce the temperature setting significantly and perform testing again.
- Reduce the press time.
- Always use a clean protective sheet (e.g., Teflon sheet, parchment paper) between the heat platen and the garment/patch.
- Double-check the heat tolerance of the specific fabric type and adjust settings accordingly.
- Consider using a thicker protective cover for particularly sensitive fabrics after testing.
4.3 Adhesive bleeding through fabric (“ghosting”)
This occurs when excess melted adhesive permeates the fabric, sometimes leaving a faint outline (“ghosting”) of the patch visible on the other side or around the edges.
Causes:
- Excessive pressure, forcing too much adhesive into and through the fabric weave.
- Excessive heat, making the adhesive overly fluid.
- Application onto very thin or porous fabric.
- Incompatibility between the specific adhesive type and the fabric.
Solutions:
- Reduce the pressure setting.
- Reduce the heat (temperature) setting.
- Perform thorough compatibility testing on scrap fabric first, especially with thin materials.
- If using thick patches on thin fabric, consider if a different patch type or application method (like sewing) might be more suitable.
4.4 Patch appears wrinkled or fabric around it is distorted
Wrinkling can affect the patch itself or the surrounding garment area, compromising the professional look.
Causes:
- Garment not laid completely flat or smooth on the platen before pressing.
- Uneven surface beneath the application area (e.g., seams, pockets) causing distortion under pressure.
- Movement or shifting of the garment or patch during the pressing cycle.
- Fabric shrinkage or stretching due to excessive temperature.
- Improper cooling (e.g., stretching the garment while still warm).
Solutions:
- Ensure the garment is meticulously smoothed out before pressing. Pre-press helps.
- Use a pressure pillow to compensate for uneven surface areas and ensure even pressure distribution.
- Use heat-resistant tape to securely hold the patch and garment area in place.
- Verify and adjust temperature settings based on fabric type; reduce if necessary.
- Allow the garment and patch to cool completely on a flat surface without stretching or moving it prematurely after pressing.
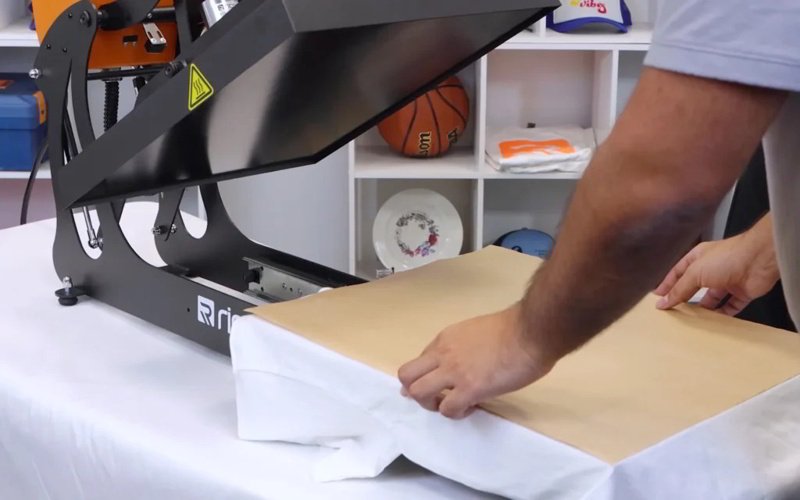
5. Ensuring long-term patch durability and garment care
Proper application is the first step, but subsequent care significantly impacts the lifespan and appearance of both the patch and the garment itself.
5.1 Post-application best practices for lasting bonds
Achieving maximum durability relies on allowing the adhesive bond to fully cure. After heat pressing, refrain from washing the garment for at least 24 to 48 hours. This waiting period gives the adhesive the necessary time to completely set and solidify its grip on the fabric fibers, ensuring better long-term patch integrity.
For items subjected to exceptionally heavy wear, frequent washing, or attachment to challenging fabrics, consider adding a stitching border around the patch *after* heat pressing and curing. This should be viewed not as a failure of the heat press method, but as an optional reinforcement – a quality upgrade that provides an extra layer of security and enhances longevity in demanding conditions.
5.2 Washing and care instructions for patched apparel
Providing clear garment care instructions to end customers helps maintain the quality of the customized apparel and ensures patch durability. Recommend the following washing guidelines:
- Turn garment inside out: Before washing, always turn the apparel inside out. This minimizes friction and abrasion directly on the patch surface during the wash cycle.
- Use cold wash: Wash the garment using a cold wash setting (or lukewarm at most). Hot water can potentially weaken the adhesive over time.
- Select gentle cycle: Use the washing machine’s gentle cycle (or delicate cycle) to reduce stress on both the fabric and the patch.
- Mild detergent: Use a mild laundry detergent. Avoid using bleach or harsh fabric softeners, as these chemicals can degrade the patch materials or affect the adhesive.
- Hang dry recommended: Whenever possible, hang dry the garment or lay it flat to air dry. Avoid using a high-heat tumble dryer, as excessive heat can compromise the patch durability and potentially reactivate or weaken the adhesive. If machine drying is necessary, use the lowest heat setting (tumble dry low or air fluff).
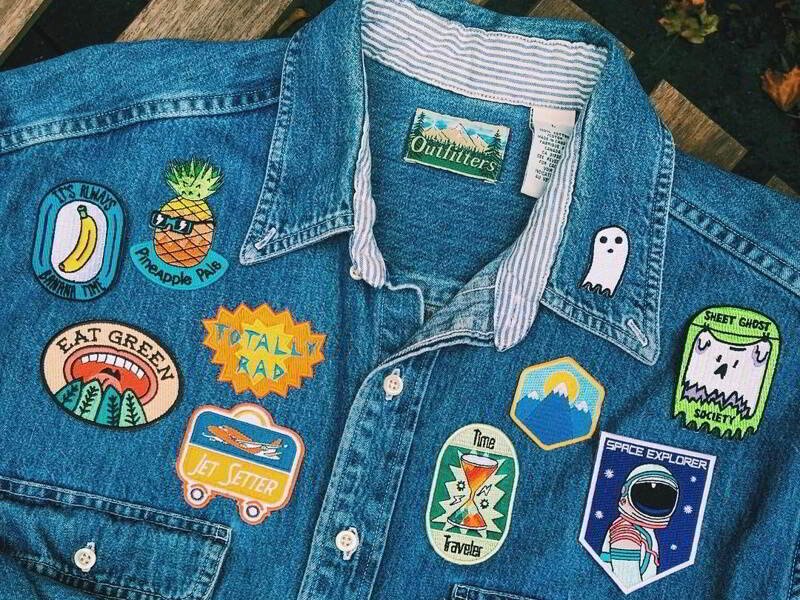
6. Related questions (FAQs from businesses)
Here are answers to some frequently asked questions businesses encounter when working with heat press patch applications.
6.1 Is a household iron ever okay for applying patches to products I sell?
For achieving consistent, professional results suitable for products being sold, a household iron is generally not recommended. While it might suffice for personal, one-off applications, irons suffer from significant drawbacks in a business context: inconsistency in temperature across the soleplate, inability to provide controlled and even pressure, and much lower efficiency compared to a heat press.
These factors increase the risk of failed applications, damaged garments, and ultimately, products that don’t meet professional quality standards. Investing in a proper heat press ensures reliability and quality control.
6.2 What’s the real difference between heat seal, iron-on, and sew-on patches for my business?
The terms “heat seal” and “iron-on patches” are often used interchangeably; both refer to patches equipped with a heat-activated adhesive backing designed for thermal application. The primary difference lies in the application methods when compared to sew-on patches.
Heat application is significantly faster and requires less specialized skill than sewing, making it efficient for larger runs. However, sew-on patches, which require manual or machine stitching, can offer superior durability on certain items subjected to extreme stress or washing conditions, or on fabrics unsuitable for heat application. The choice depends on production volume needs, desired finish, garment type, and end-use demands.
6.3 How do I reliably heat press patches onto hats or other curved items?
Attempting to heat press patches on hats or other distinctly curved surfaces using a standard flatbed heat press is generally ineffective and ill-advised. Achieving the necessary even pressure and consistent heat application across a non-flat surface requires specialized equipment.
A dedicated hat press, featuring curved upper and lower platens designed to match the contour of a cap, is essential for professional and reliable results on headwear. Using the wrong equipment will lead to poor adhesion and potential damage.
6.4 Do embroidered patches need different settings than woven patches?
Yes, it’s likely that embroidered patches and woven patches will require slightly different heat press settings. Embroidered patches are typically thicker and denser due to the raised thread, which can insulate the adhesive underneath.
This often means they might require slightly more heat, a longer dwell time, or increased pressure compared to thinner woven patches to ensure the heat fully penetrates and activates the adhesive for a strong bond. However, as always, the specific patch construction and adhesive used are critical factors, making manufacturer guidance and thorough testing essential to determine the optimal settings for each type.
Read more:
- Iron-on patches: The definitive uniform patch guide
- What do iron-on patches look like? A visual guide
- How to make patches: DIY embroidered & iron-on patch guide
Mastering the use of a heat press with the correct settings is fundamental for any apparel business aiming to incorporate iron-on patches effectively. Moving beyond inconsistent household methods to a controlled heat press process ensures not only greater efficiency but, more importantly, professional quality and enhanced durability for your customized apparel products.
Well-applied patches significantly boost brand visibility and offer compelling avenues for clothing personalization, adding tangible value that customers appreciate. By prioritizing proper preparation, careful testing, and adherence to best practices in application and care, you can confidently elevate your garments and make a lasting impression.
Contact Packlove if you need further expert advice or assistance in finding quality custom patches to suit your specific needs.