Navigating the world of knit fabrics can feel like entering a whole new dimension of sewing. Unlike their woven counterparts, knits possess a unique stretch and drape that can present exciting possibilities, but also a few initial hurdles for beginners.
This article provides the tools to begin a knit sewing adventure, to address common fears, and to provide skills for beautiful, professional-looking results. The looped structure of knit fabrics offers comfort and versatility, but these’re benefits that can only be harnessed by understanding a different approach to techniques.
1. Understanding stretch fabrics
1.1 What makes fabric stretchy?
Knit fabrics, unlike their woven counterparts, possess a unique looped structure that is the very source of their stretch. Imagine a chain, where each link interlocks with the next. This interconnectedness is what gives knits their flexibility.
Woven fabrics, on the other hand, are constructed with threads interlacing at right angles – a much more rigid, grid-like arrangement. This fundamental difference in construction is why a woven cotton shirt feels stiff compared to a knit cotton T-shirt.
To enhance the stretch and recovery (the ability of a fabric to return to its original shape after being stretched) of fabrics, manufacturers often incorporate spandex or elastane fibers. These synthetic fibers are renowned for their exceptional elasticity. Even a small percentage of spandex can significantly increase a fabric’s stretch capabilities.
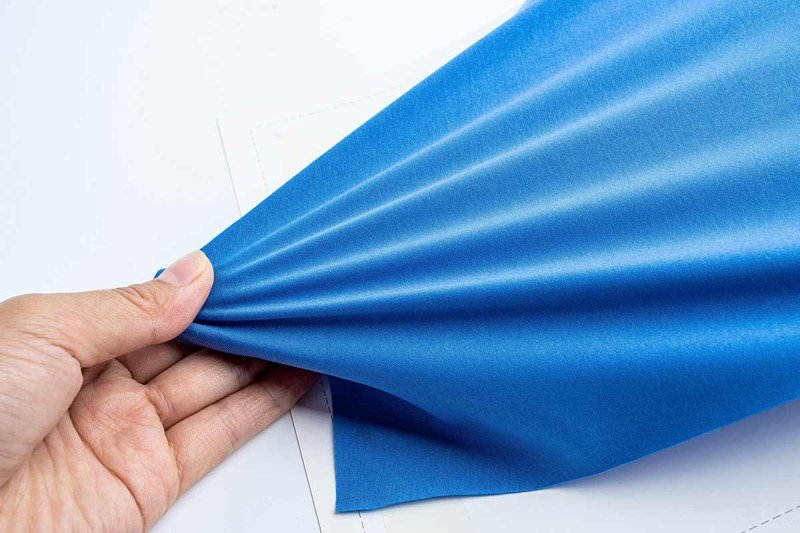
1.2 Types of stretch fabrics
Here’s a quick rundown of some common stretch fabrics:
- Jersey: This is a versatile, single-knit fabric (a fabric created using a single set of needles) often used for T-shirts, dresses, and other everyday garments. Jersey typically has good drape (the way a fabric hangs) and is relatively easy to sew.
- Spandex/Lycra: While technically a fiber, not a fabric, spandex (also known as Lycra) is synonymous with stretch. It’s rarely used on its own but is blended with other fibers to add significant stretch and recovery. Think leggings, activewear, and swimwear.
- Double knit: As the name suggests, double knits are created with two sets of needles, resulting in a thicker, more stable fabric than jersey. They often have less drape and are suitable for more structured garments.
- Ponte knit: A type of double knit, Ponte is known for its stability, durability, and resistance to wrinkling. It’s a great choice for comfortable yet polished-looking pants, skirts, and jackets.
- Scuba knit: This is a thicker, spongy double knit with a smooth surface. It’s often used for structured dresses, skirts, and athletic-inspired apparel.
Fabric Type | Description | Common Uses | Ease of Sewing |
---|---|---|---|
Jersey | Lightweight, drapey | T-shirts, dresses | Easy |
Spandex/Lycra | Very stretchy | Leggings, activewear | Moderate |
Double Knit | Thicker, more stable | Structured garments | Moderate |
Ponte Knit | Stable, wrinkle-resistant | Pants, skirts, jackets | Moderate |
Scuba Knit | Thick, spongy | Structured garments | Moderate to Difficult |
1.3 Identifying stretch direction
Understanding the direction of stretch is crucial for a well-fitting garment. Stretch fabrics typically come in two varieties:
- 2-way stretch: This fabric stretches in one direction, usually from selvage to selvage (the finished edges of the fabric).
- 4-way stretch: This fabric stretches in both directions – crosswise and lengthwise.
To identify the direction of greatest stretch, gently pull the fabric along both the crosswise and lengthwise grains. The direction with the most give is the direction of greatest stretch. For most patterns, the direction of greatest stretch should go around the body. This ensures comfort and allows the garment to move with you. Ignoring this can lead to a garment that feels restrictive or doesn’t fit properly.
1.4 Stretch percentage and recovery
Stretch percentage:
Stretch percentage refers to how much a fabric can extend beyond its original length. To determine this, take a 4-inch section of fabric along the direction of greatest stretch. Hold one end firmly and gently pull the other end until it resists. Measure the extended length. Subtract the original length (4 inches) from the stretched length, then divide that number by the original length and multiply by 100.
For example:
If the 4-inch section stretches to 6 inches:
(6-4)/4 * 100 = 50% stretch
The stretch percentage required will depend on the project. Fitted garments like leggings require a higher stretch percentage than looser-fitting garments. Choosing a fabric with appropriate stretch is essential.
Recovery:
Recovery refers to how well a fabric returns to its original shape after being stretched. A fabric with good recovery will snap back quickly, while one with poor recovery may remain stretched out. Good recovery is key to preventing garments from becoming baggy or misshapen over time. Gently stretch the fabric, and let go, and watch the recovery.
2. Essential tools and supplies
2.1 Sewing machine needles
Using the correct sewing machine needle is paramount when working with stretch fabrics. Ballpoint needles are specifically designed for this purpose. Unlike sharp needles, which can pierce and damage knit fibers, ballpoint needles have a rounded tip that gently pushes the fibers aside. This prevents snags, skipped stitches, and holes in your fabric.
Here’s a guide to needle sizes and their recommended uses:
Needle Size | Fabric Type | Fabric Weight |
---|---|---|
70/10 | Lightweight knits, Lycra | Very Light |
80/12 | Medium-weight knits, Jersey | Light to Medium |
90/14 | Heavier knits, Ponte | Medium to Heavy |
2.2 Choosing the right thread
For most stretch fabric projects, polyester thread is the preferred choice. Polyester thread has inherent stretch and strength, allowing it to move with the fabric without breaking. Cotton thread, while suitable for woven fabrics, lacks the necessary give and is prone to snapping when used with stretch materials.
Thread weight isn’t usually a major concern with stretch fabrics, but an all-purpose polyester thread will work well for most applications.
2.3 Recommended stitches
Because stretch fabrics stretch, the seams need to stretch, too. Traditional straight stitches lack this flexibility and can easily break when the fabric is pulled. Therefore, specialized stretch stitches are essential. Here are some common options:
- Zigzag stitch: This is the most readily available stretch stitch on most sewing machines. It creates a series of angled stitches that allow the seam to stretch. A narrow zigzag (where the width and length are relatively small) is often sufficient.
- Stretch stitch (lightning bolt stitch): Many machines have a dedicated stretch stitch, often resembling a lightning bolt. This stitch is specifically designed for stretch fabrics and provides excellent seam elasticity.
- Triple stretch stitch: This stitch creates three rows of stitching for extra strength and stretch. It’s particularly useful for areas that experience high stress, such as armholes or crotch seams.
- Serger/Overlocker: While not essential, a serger (also known as an overlocker) creates a professional-looking, highly stretchable seam that also finishes the raw edges. It’s ideal for knitwear but requires a separate machine.
The choice of stitch depends on the fabric and the project. For example, a simple T-shirt might only require a zigzag stitch, while leggings might benefit from a triple stretch stitch or a serged seam.
2.4 Optional but helpful tools
- Walking foot: A walking foot is a valuable tool for sewing stretch fabrics. It has an extra set of feed dogs on top that work in conjunction with the machine’s feed dogs below. This ensures that both layers of fabric are fed evenly through the machine, preventing stretching, puckering, and wavy seams. It’s particularly helpful for thicker or slippery stretch fabrics.
- Twin needle: A twin needle creates two parallel rows of stitching on the top of the fabric and a zigzag stitch on the back. This provides both stretch and a neat, professional-looking finish, especially for hems. It’s a great alternative to a coverstitch machine.
- Rotary cutter and cutting mat: Stretch fabrics can be easily distorted when cut with scissors. A rotary cutter and cutting mat allow for smooth, precise cuts without stretching the fabric out of shape. This ensures accurate pattern pieces and a better final result.
- Fabric stabilizer: Fabric stabilizer, either tear-away or wash-away, can be a lifesaver when sewing tricky areas like buttonholes or when working with very delicate or sheer stretch fabrics. It provides temporary support to prevent stretching and distortion during sewing.
3. Preparing stretch fabric
3.1 Pre-washing and drying
Pre-washing stretch fabrics is a crucial step that should never be skipped. Stretch fabrics, especially those containing cotton, are prone to shrinkage. Pre-washing before cutting and sewing ensures that any shrinkage happens before the garment is constructed, preventing unpleasant surprises after the first wash.
Follow these guidelines:
- Machine wash the fabric using the same settings you would use for the finished garment (usually cold or warm water).
- Tumble dry on a low heat setting or air dry, depending on the fabric’s care instructions. Some delicate stretch fabrics may be better suited to air drying.
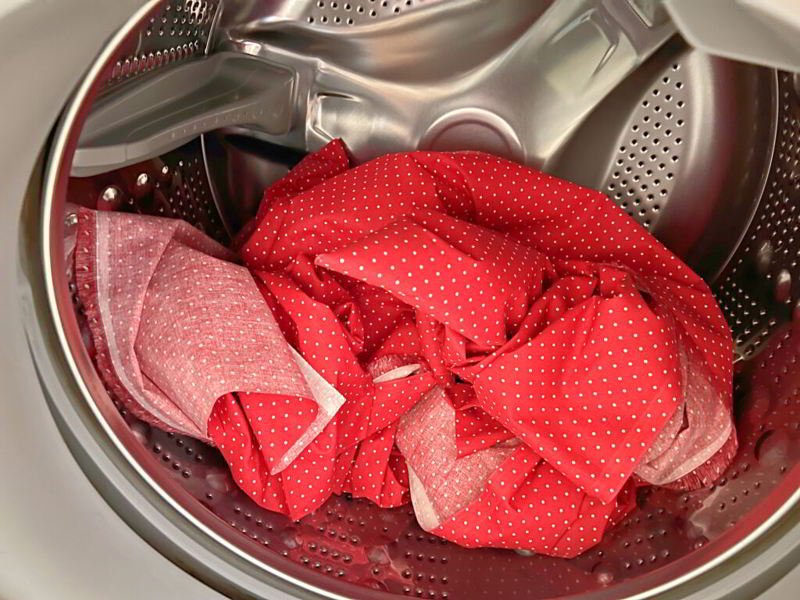
3.2 Cutting stretch fabric
Accuracy is key when cutting stretch fabric. Because these materials are so pliable, they can easily be stretched or distorted during the cutting process. Here are some tips for best results:
- Use a rotary cutter and mat: As mentioned earlier, a rotary cutter and self-healing cutting mat provide the most accurate and smooth cuts, minimizing the risk of stretching.
- Lay fabric flat: Ensure the fabric is laid completely flat on the cutting surface. Do not allow any part of the fabric to hang off the edge, as this can cause it to stretch under its own weight.
- Use pattern weights or pins: Secure the pattern pieces to the fabric using pattern weights or plenty of pins. If using pins, place them within the seam allowance to avoid creating visible holes.
- Don’t over-stretch: When cutting, avoid pulling or stretching the fabric.
If you must use scissors, make sure they are sharp and make long, smooth cuts instead of short, choppy ones.
3.3 Marking stretch fabric
Marking stretch fabric requires a delicate touch. Traditional marking methods, like hard chalk, can drag or distort the fabric. Here are some better alternatives:
- Tailor’s chalk: Use a light-colored tailor’s chalk that will show up on the fabric without requiring excessive pressure.
- Tracing wheel and paper: A tracing wheel and tracing paper can transfer markings without stretching the fabric. Place the tracing paper between the fabric and the pattern, and use the tracing wheel to trace the lines.
- Fabric markers: Choose fabric markers that are specifically designed for use on stretch fabrics. These markers typically have a fine tip and won’t bleed or damage the fabric. Always test the marker on a scrap of fabric first to ensure it doesn’t leave a permanent mark.
Avoid using pens or permanent markers, as they can bleed or be difficult to remove.
4. Sewing techniques
4.1 Setting up your sewing machine
Before you begin sewing, make a few adjustments to your sewing machine settings:
- Tension: Stretch fabrics often require a slightly lower tension setting than woven fabrics. Start with the recommended setting for your machine and fabric type, then test on a scrap and adjust as needed. Too much tension can cause puckering or wavy seams.
- Stitch length: When using a stretch stitch (like a zigzag), a slightly longer stitch length is often recommended. This allows for greater stretch in the seam.
- Presser foot pressure: If your machine has adjustable presser foot pressure, you may need to reduce it slightly for stretch fabrics. This prevents the fabric from being stretched or compressed as it feeds through the machine.
4.2 Pinning and handling techniques
Gentle handling is essential when sewing stretch fabrics. Avoid pulling, tugging, or stretching the fabric as you sew. Here are some specific tips:
- Use plenty of pins or clips: Secure the fabric layers together with plenty of pins or sewing clips. This prevents shifting and ensures that the edges stay aligned. Place pins perpendicular to the seam.
- Handle gently: Guide the fabric through the machine without pulling or forcing it. Let the feed dogs do their job.
4.3 Sewing with a consistent seam allowance
Maintaining a consistent seam allowance is crucial for any sewing project, but it’s particularly important with stretch fabrics. An inconsistent seam allowance can affect the fit and overall appearance of the garment. Use the seam allowance guide on your sewing machine’s needle plate or use a seam guide attachment to help you maintain accuracy.
4.4 Hemming stretch fabrics
Hemming stretch fabrics requires a method that allows the hem to stretch along with the rest of the garment. Here are a few effective techniques:
- Twin needle: As mentioned before, a twin needle creates a stretchy and professional-looking hem. Thread your machine with two spools of thread (one for each needle) and select a straight stitch. The twin needle will create two parallel rows of stitching on the top and a zigzag on the back.
- Zigzag stitch: A narrow zigzag stitch can also be used to hem stretch fabrics. It provides sufficient stretch and is a readily available option on most machines.
- Coverstitch machine: A coverstitch machine creates a professional-looking hem with multiple rows of stitching on the top and a looped stitch on the back. This is the type of hem often seen on commercially made knit garments. However, it requires a specialized machine.
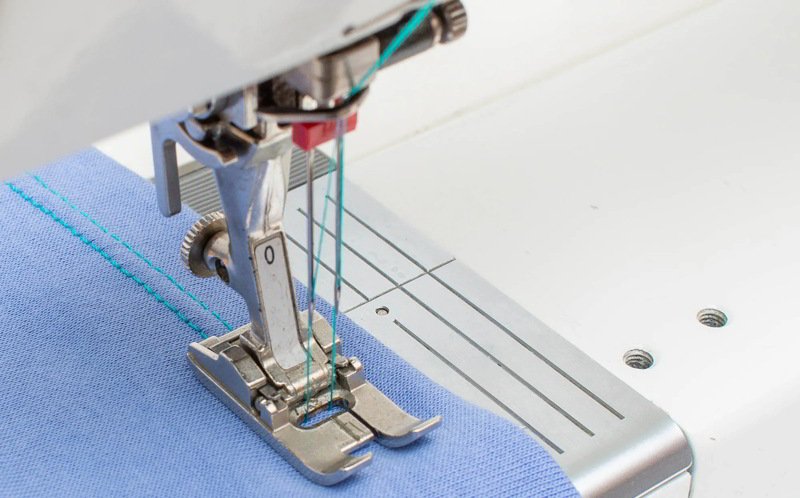
4.5 Sewing curves
Sewing curves on stretch fabric needs a little bit different approach comparing with woven.
- Use short stitch length.
- Use lots of pins.
- Sew slowly.
5. Troubleshooting common problems
5.1 Wavy seams
Wavy seams are a common problem when sewing stretch fabrics. They occur when the fabric is stretched or distorted during sewing, resulting in a rippled or uneven seam.
Causes:
- Incorrect tension: Too much tension on either the top or bobbin thread can cause the fabric to stretch.
- Over-stretching: Pulling or tugging the fabric while sewing.
- Uneven feeding: The fabric layers may not be feeding evenly through the machine.
Solutions:
- Adjust tension: Test your stitch on a scrap of fabric and adjust the tension until the seam lies flat.
- Use a walking foot: A walking foot helps feed the fabric evenly, preventing stretching.
- Handle gently: Avoid pulling or stretching the fabric as you sew.
- Use a stabilizer: A temporary fabric stabilizer can help prevent stretching, especially on delicate fabrics.
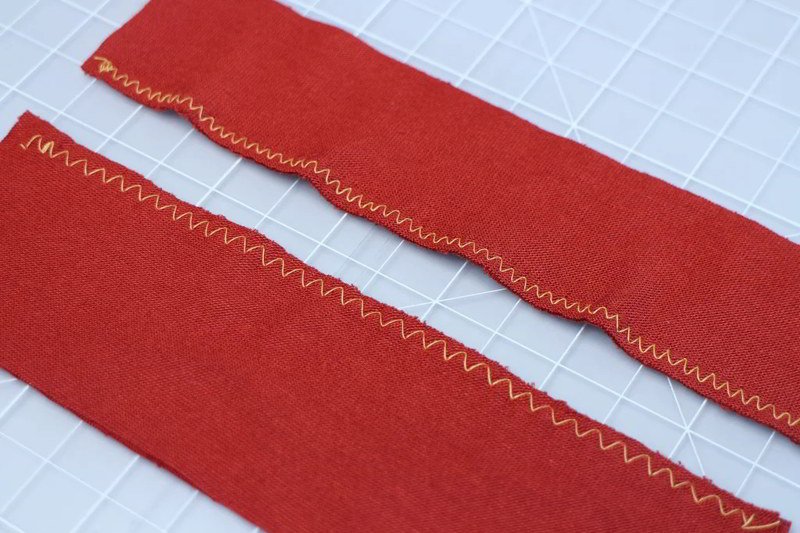
5.2 Puckering:
Puckering refers to small wrinkles or gathers that form along the seam line.
Causes:
- Incorrect needle: Using a needle that is too large or the wrong type (e.g., a sharp needle instead of a ballpoint).
- Wrong thread: Using a thread that is too heavy or incompatible with the fabric (e.g., cotton thread).
- Too high tension: Excessive tension can cause the fabric to gather.
- Incorrect stitch type: Using a straight stitch instead of a stretch stitch.
Solutions:
- Use a ballpoint needle: Ensure you are using the correct size ballpoint needle for your fabric.
- Use polyester thread: Switch to polyester thread, which has more give.
- Lower tension: Reduce the top and/or bobbin tension.
- Choose a stretch stitch: Use a zigzag stitch, stretch stitch, or other appropriate stitch type.
5.3 Skipped stitches
Skipped stitches occur when the needle fails to catch the bobbin thread, resulting in gaps in the seam.
Causes:
- Incorrect needle: Using the wrong type of needle (e.g., a sharp needle instead of a ballpoint) or a damaged needle.
- Dull needle: A dull needle may not penetrate the fabric properly.
- Thread issues: Incorrectly threaded machine, thread catching, or poor-quality thread.
- Machine settings: Incorrect tension or stitch length.
Solutions:
- Use a new ballpoint needle: Replace the needle with a new ballpoint needle of the correct size.
- Check thread path: Ensure the machine is threaded correctly and the thread isn’t snagging.
- Adjust machine settings: Check the tension and stitch length, and adjust as needed.
5.4 Thread breakage
Thread breakage can be frustrating and disrupt the sewing process.
Causes:
- Thread quality: Using old, weak, or poor-quality thread.
- Too high tension: Excessive tension can put stress on the thread, causing it to break.
- Incorrect needle: Using the wrong needle size or type can damage the thread.
Solutions:
- Use high-quality polyester thread: Invest in good-quality polyester thread.
- Lower tension: Reduce the tension on the top and/or bobbin thread.
- Use the correct needle size: Make sure you are using the appropriate needle size for your fabric.
5.5 Fabric stretching/distortion
Fabric stretching or distortion can occur during cutting, handling, or sewing.
Causes:
- Over-handling: Excessive pulling or stretching of the fabric before or during sewing.
- Incorrect cutting: Using dull scissors or stretching the fabric while cutting.
- Uneven feeding: The fabric layers not feeding evenly through the machine.
Solutions:
- Handle gently: Minimize handling and avoid pulling or stretching the fabric.
- Use a rotary cutter: A rotary cutter and mat provide clean, accurate cuts without stretching.
- Use a walking foot: A walking foot helps feed the fabric evenly, preventing distortion.
6. Advanced techniques
6.1 Sewing with sheer or delicate stretch fabrics
Sewing with sheer or delicate stretch fabrics, such as mesh or lightweight Lycra, requires extra care.
Tips:
- Use a stabilizer: Tear-away or wash-away stabilizer is essential to prevent stretching and distortion. Place it underneath the fabric before sewing.
- Use a fine ballpoint needle: Choose a smaller size ballpoint needle (e.g., 70/10).
- Lower tension: Reduce the tension even further than usual.
- Short stitch length: Use a shorter stitch length for better control and to prevent the fabric from being pulled into the machine.
- Test on scraps.
6.2 Working with high-stretch fabrics (like swimwear Lycra)
High-stretch fabrics, like those used for swimwear and activewear, present unique challenges.
Tips:
- Use a special stretch needle: Consider using a stretch needle specifically designed for high-stretch fabrics. These needles have a special scarf (the indentation above the eye) that helps prevent skipped stitches.
- Specific stitch settings: Experiment with different stretch stitches and settings to find what works best. A zigzag or triple stretch stitch is often recommended.
- Consider using a serger: A serger is ideal for sewing high-stretch fabrics, as it creates strong, flexible seams that can withstand significant stretching.
- Test on scraps.
6.3 Pattern adjustments for stretch fabrics
When working with stretch fabrics, you may need to make pattern adjustments, especially for fitted garments. This is because stretch fabrics can stretch, meaning a garment made in the same size as a woven pattern might be too large.
Negative ease:
Negative ease refers to making a garment smaller than the body measurements. The amount of negative ease depends on the stretch percentage of the fabric and the desired fit. For example, a pattern designed for a fabric with 50% stretch might require 2-4 inches of negative ease in the bust and hips.
Adjusting patterns:
- Consult the pattern: Some patterns designed for stretch fabrics will already include negative ease.
- Calculate: If the pattern doesn’t specify, you may need to calculate the negative ease based on the fabric’s stretch percentage.
- Make a muslin: Always make a muslin (a test garment) out of a similar stretch fabric to check the fit before cutting into your final fabric.
7. Related questions
7.1 Can I sew stretch fabric without a serger?
Yes, absolutely. While a serger creates a professional finish and is faster, a regular sewing machine can successfully sew stretch fabrics using the techniques outlined in this guide (ballpoint needle, stretch stitch, proper handling).
7.2 What’s the best way to finish seams on stretch fabric?
The best way to finish seams is with a serger, as it overcasts the raw edges and provides stretch. If you don’t have a serger, a zigzag stitch along the raw edge can help prevent fraying (though knit fabrics don’t typically fray much).
7.3 How do I prevent the edges of my stretch fabric from curling?
A starch spray can help.
7.4 How can I sew a T-shirt neckline without it stretching out?
Using a stabilizer, such as a lightweight fusible interfacing or tear-away stabilizer, on the neckline before sewing can help prevent stretching.
7.5 Can I use a regular sewing machine for all stretch fabrics?
Yes, a regular sewing machine can handle most stretch fabrics, provided you use the correct needle, thread, and stitch settings.
Read more:
Sewing with stretch fabrics might seem daunting at first, but with the right knowledge and techniques, it can be a rewarding experience. Practice and experimentation are key. Don’t be afraid to try different techniques and settings to find what works best for you and your project. With a little patience, you’ll be confidently sewing all kinds of stretch garments and projects.