For small apparel businesses, ensuring consistent production quality presents a significant challenge. Understanding garment construction – essentially the process of clothing assembly – is crucial. High-quality construction directly impacts garment durability, fit, and overall appeal. This, in turn, influences customer satisfaction, shapes brand reputation, and ultimately contributes to business success.
This guide delves into the essential steps, techniques, and strategic considerations involved in garment construction, providing valuable insights to help businesses navigate the manufacturing process and produce apparel that meets customer expectations.
Readers will gain a foundational knowledge of how clothes are made, why meticulous construction matters, and how to make informed decisions for their production needs. Let’s start!
1. Why Solid Garment Construction is Non-Negotiable for Your Clothing Brand
Investing in solid garment construction isn’t just about aesthetics; it involves profound business benefits. High-quality construction translates directly to enhanced product quality and durability. Well-made seams resist splitting, fabrics maintain their shape after washing, and details like buttons or zippers remain securely attached. This durability reduces returns and complaints, fostering customer satisfaction and trust.
Furthermore, consistent garment fit relies heavily on precise construction. Accurate pattern cutting and assembly ensure that sizing remains consistent across production runs, leading to fewer sizing issues and greater comfort for the wearer. Happy customers who receive garments that fit well are more likely to become repeat buyers and recommend the brand.
From a business perspective, focusing on proper construction techniques from the outset can positively impact production costs. While using better techniques or materials might seem initially more expensive, doing so minimizes errors, rework, and wasted materials during the manufacturing process.
Efficient assembly workflows, built on sound construction principles, save time and labor. Ultimately, a commitment to quality construction strengthens brand reputation, positioning the apparel brand as reliable and worthy of customer loyalty.
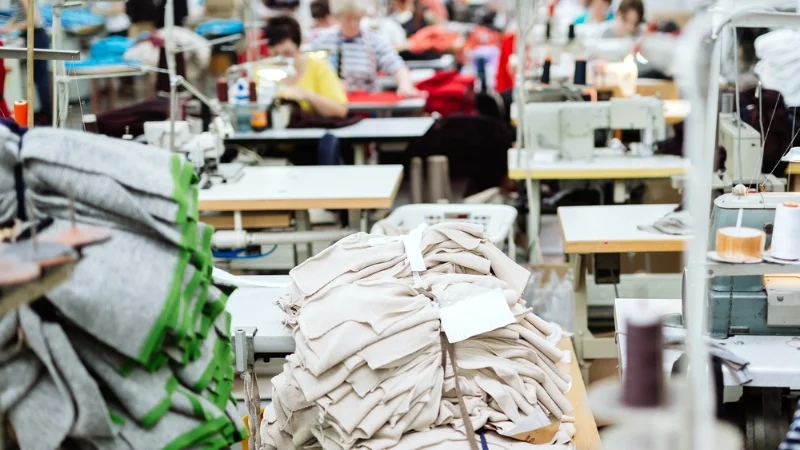
2. The Core Process: How Garments are Assembled Step-by-Step
2.1 Stage 1: Pattern Making and Design Interpretation
The journey from an apparel design sketch to a finished garment begins with pattern making. This stage involves translating the two-dimensional design concept into a set of templates, known as pattern pieces. These pieces represent the different sections of the garment (like sleeves, bodice front, bodice back, collar).
Achieving accuracy during pattern making is fundamental, as these templates dictate the shape and dimensions of the fabric pieces to be cut, directly influencing the final garment fit. The goal is to create precise guides for cutting the fabric sections that will later be assembled into a three-dimensional form.
2.2 Stage 2: Fabric Selection, Preparation, and Layout
Choosing the appropriate textile goes beyond color and print. Fabric selection involves considering fabric properties such as weight, drape (how the fabric hangs), and stretch, as these characteristics significantly affect how the garment will look, feel, and behave during construction and wear.
Some fabrics may require preparation, like pre-washing, to prevent shrinkage after the garment is made. Once the fabric is ready, the pattern pieces are carefully arranged during layout. Proper placement, respecting the fabric’s grainline (the direction of the threads), is vital to ensure the garment hangs correctly and maintains its shape.
2.3 Stage 3: Precision Cutting – The Foundation of Fit
Cutting the fabric is a critical stage where precision is paramount. Errors made here, such as deviating from the pattern lines or misaligning the fabric, directly compromise the sewing process and the final fit of the garment. Using sharp cutting tools, like dedicated fabric scissors or rotary cutters, and meticulously following the pattern piece outlines are essential.
Attention must be paid to the fabric grainline marked on the pattern pieces to ensure consistency and proper drape in the finished product. Accurate cutting lays the foundation for smooth assembly and a well-fitting garment.
2.4 Stage 4: Sewing and Assembly
2.4.1 Introduction to Basic Seams and Stitches
Seams are formed when two or more pieces of fabric are joined together using stitches. Sewing machines offer various stitch types, but two fundamental ones are the straight stitch and the zigzag stitch. The straight stitch is the workhorse for creating most structural seams, joining main garment sections.
The zigzag stitch is often used for finishing raw fabric edges to prevent fraying or for sewing knit fabrics that require some stretch in the seam. Understanding the basic function of these stitches is the first step in assembling garment pieces.
2.4.2 Order of Operations: Joining Major Sections Logically
Garment assembly follows a specific order of operations rather than random stitching. There’s a logical sequence that makes the sewing process more efficient and ensures components fit together correctly. For instance, with a simple t-shirt, shoulder seams are typically sewn first, allowing the neckline to be finished more easily.
Then, sleeves might be attached to the bodice before the side seams are sewn from the underarm down to the hem. Following a standard assembly order prevents awkward construction steps and leads to a cleaner finish.
2.4.3 Attaching Complex Components
Beyond the main body sections, many garments incorporate components like collars, cuffs, waistbands, zippers, or button plackets. Attaching these elements often requires specific sewing techniques and greater attention to detail.
These components add functionality (like closures or fitted edges) and contribute significantly to the garment’s overall structure and style. Their correct placement and neat attachment are hallmarks of quality construction.

2.5 Stage 5: Finishing Techniques for a Polished, Professional Product
The final stage involves finishing techniques that transform a collection of sewn pieces into a complete, professional product. Key steps include: hemming, which creates clean, finished edges on sleeves, trousers, and garment bottoms; seam finishing, which tidies internal raw edges to prevent fraying and enhance durability (discussed further below); thorough pressing with an iron to flatten seams, sharpen creases, and give the garment its final shape; and rigorous quality control checks, involving snipping loose threads, inspecting seam integrity, and verifying measurements.
3. Key Construction Elements That Define Garment Quality
3.1 Understanding Fabric Behavior: Beyond the Surface
The chosen textile significantly influences construction methods and the final garment’s quality. Understanding fabric behavior means recognizing how different fabric properties affect the sewing process and wearability.
For example, a fabric’s drape determines how elegantly it hangs; its weight impacts structure and warmth; and its degree of stretch necessitates specific stitches (like zigzag or stretch stitches) and handling techniques to avoid puckering or distortion. Selecting construction techniques compatible with the fabric’s nature is essential for achieving the desired outcome.
3.2 Seam Finishes: More Than Just Joining Fabric
Seam finishes are techniques applied to the raw edges of fabric inside a garment after a seam has been sewn. Their primary purpose is to prevent fraying, which enhances durability and gives the garment interior a neater appearance. Several methods exist, varying in complexity, look, and suitability for different fabrics:
- Serged/Overlocked: A very common finish created by a serger (or overlocker) machine. This method trims the raw edge and encases the edge in thread loops simultaneously. Offers a fast, clean, and durable finish suitable for many fabric types.
- French Seam: An enclosed seam technique where the raw edges are completely hidden within a seam. Creates a very neat, high-end finish, ideal for lightweight or sheer fabrics where raw edges might show through. Requires more time and precision.
- Flat-Felled Seam: An extremely durable seam where one raw edge is folded over the other, and both are stitched flat. Often seen on denim jeans and workwear due to superior strength. Creates a visible row of parallel stitching on the outside.
The choice of seam finish impacts production time, cost, and the garment’s final quality perception.
3.3 The Critical Role of Pressing Throughout Construction
Pressing (using an iron) seams and garment sections as they are sewn is a non-negotiable step for achieving professional-level quality. This is different from final laundry ironing. Pressing during construction flattens seam allowances, sets stitches into the fabric, helps shape curves and collars, and makes subsequent sewing steps easier and more accurate.
Properly pressed seams lie flat and look crisp, significantly enhancing the garment’s overall appearance and fit. Skipping this step often results in a homemade or less polished look.
3.4 Essential Tools That Ensure Consistency
Achieving consistent results in garment construction relies on using the right tools. Indispensable items include:
- A reliable sewing machine appropriate for the fabrics being used.
- Sharp fabric scissors, kept separate from those used for paper, for clean, precise cuts.
- An iron and ironing board dedicated to pressing during construction.
- Accurate measuring tools, such as a flexible measuring tape and clear rulers.
- Pins and marking tools (chalk, fabric pens).
For businesses aiming for highly professional finishes, especially on knitwear or to speed up edge finishing, a serger (or overlocker) is a valuable addition, providing fast and neat seam finishing. Investing in quality tools contributes significantly to construction consistency.
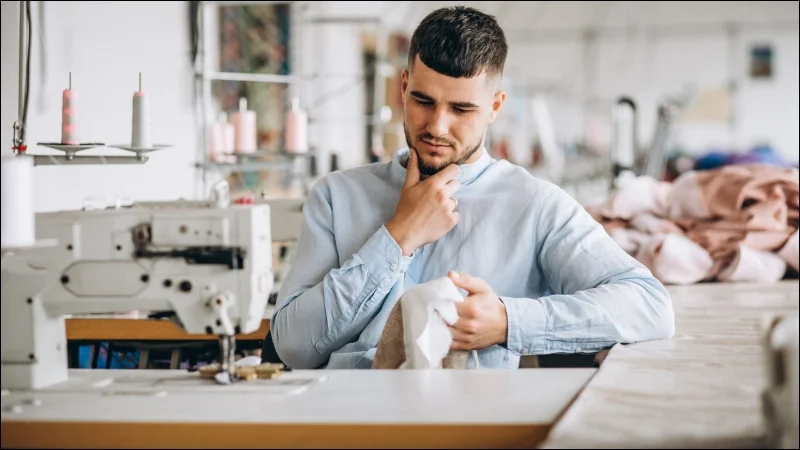
4. Smart Garment Construction Strategies for Small Apparel Businesses
Small businesses need to adopt smart strategies that balance quality standards with budget constraints and production timelines. This often involves choosing cost-effective construction techniques that still deliver durability and a professional appearance. For example, serging seam allowances is generally faster and less expensive than creating French seams, making serging a practical choice for many everyday garments.
Understanding common construction flaws helps in preventing them. Puckered seams, often caused by incorrect machine tension or handling stretchy fabrics improperly, can be avoided with practice and the right settings. Mismatched patterns or plaids at seam lines signal a lack of attention during the cutting and layout stage.
Clear communication is vital, especially when outsourcing production to manufacturing partners or sewing contractors. Utilizing technical packs (tech packs)—detailed documents outlining construction methods, measurements, materials, seam types, and finishing requirements—ensures everyone involved understands the expectations.
Simple diagrams within the tech pack can clarify complex assembly steps. Investing time in developing clear specifications minimizes errors and ensures the final product aligns with the brand’s quality standards.
Seam Finish | Look | Durability | Relative Speed/Cost | Best For |
---|---|---|---|---|
Serged/Overlocked | Neat, enclosed edge loops | Good | Fast / Low | Most fabrics, internal seams, knits |
French Seam | Very neat, no raw edges seen | Good | Slow / High | Lightweight, sheer fabrics, high-end items |
Flat-Felled Seam | Visible parallel stitching | Excellent | Moderate / Moderate | Denim, workwear, sturdy fabrics |
5. Related Questions
5.1 What is the main difference between garment construction and tailoring?
Garment construction refers to the general process of assembling any type of clothing from fabric pieces. Tailoring, while a form of garment construction, specifically involves highly skilled techniques to create custom-fitted garments, particularly structured items like suits and coats. Tailoring often incorporates more complex internal structuring (like canvassing and padding) and intricate hand-finishing details to achieve a precise fit and shape.
5.2 How does the choice of seam finish affect the cost per garment?
The cost per garment is directly influenced by the time and skill required for a particular seam finish. Simpler finishes like serging are very fast to execute with the right machinery, keeping labor costs lower. More complex finishes, such as French seams or flat-felled seams, require multiple steps, greater precision, and more time, thus increasing the labor cost associated with producing each garment.
Material cost differences are usually negligible, but the time factor is significant.
Essential quality control checks during and after construction include inspecting for: even and consistent stitch length; secure seams without skipped stitches or breaks; absence of puckering or pulling along seam lines; correct placement and secure attachment of components like zippers, buttons, and collars; neatness of finishing techniques like hems and seam finishes; and verification that final garment measurements match the specified dimensions (specs).
5.4 Can sustainable practices be incorporated into garment construction?
Yes, sustainable practices can be integrated into construction. Choosing durable construction techniques and high-quality materials extends the garment’s lifespan, reducing the need for frequent replacement. Optimizing fabric layout during cutting minimizes fabric waste.
Selecting eco-friendly materials, such as organic cotton, recycled polyester, or biodegradable threads, where feasible and appropriate for the product, also contributes to sustainability. Proper machine maintenance ensures energy efficiency.
Read more:
Mastering the fundamentals of quality construction is not merely a technical exercise; forms the bedrock of a successful and enduring apparel brand. Prioritizing how garments are assembled – from precise cutting and appropriate seam finishes to meticulous pressing and finishing – translates directly into tangible business value.
Well-constructed clothing leads to higher customer loyalty, reduced returns, positive reviews, and a stronger brand reputation. By applying the principles discussed, small apparel businesses can create products that stand out for their quality and durability, building a foundation for long-term success.
Considering details extends to presentation as well; ensuring high-quality labels and tags are properly attached further enhances the professional image of the finished product.