Have you ever looked closely at your t-shirt or a blanket and wondered how it’s made? Most fabric is created from two sets of threads that intertwine in a process called weaving. This article simply explains “weft”, one of these key threads in textile production. We’ll make it easy to understand! You’ll learn about a basic component that makes up your everyday fabrics and how it contributes to the things we make at Packlove.
1. What is weft?
1.1 Defining weft
The weft is one of the two main kinds of threads used in weaving to make fabric. Think of weft threads as the ones that go *across* the fabric, from left to right or right to left. You might also hear weft threads called filling yarn, crosswise thread, horizontal yarn in weaving, or an older term, woof.
Understanding the weft thread in fabric is key to understanding textile components and basic fabric structure elements. This is fundamental weaving terminology.
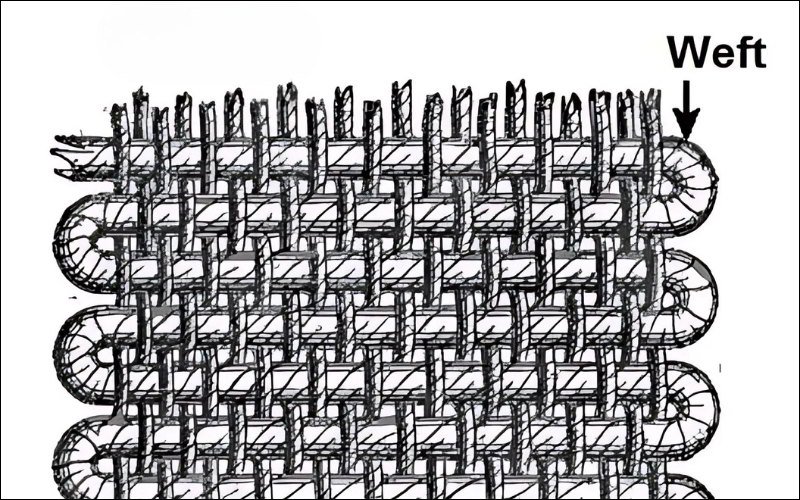
1.2 Weft and its partner: the warp
Weft threads don’t create fabric on their own. They work together with another set of threads called the warp. Warp threads are the threads that run up and down, along the length of the fabric. These threads are stretched tight from top to bottom on a weaving machine called a loom.
So, the warp threads go lengthwise, and the weft threads go crosswise, weaving over and under the warp threads to create the fabric. This helps in understanding weft and warp in textiles. Imagine the warp threads are like the strings of a guitar, held straight and tight.
The weft thread is then passed over and under these strings, going from one side to the other. This shows the difference between warp and weft: one runs lengthwise, the other crosswise.
1.3 The direction of weft
A simple way to remember: weft threads are the horizontal threads in your fabric. They go from one side to the other, defining the fabric’s horizontal direction. These crosswise threads fill the width of the fabric as it’s made. The weft runs across fabric width.
2. How weft helps make fabric
2.1 The weaving process in simple steps
The weaving process combines warp and weft to create woven fabric. Here’s how it works in simple terms:
- First, the warp threads are stretched tightly on a machine called a loom.
- Next, the weft yarn is passed through these tight warp threads. It goes over one warp thread, then under the next one, then over another, and so on, all the way across. A tool called a shuttle often carries the weft yarn through the warp.
- This action of passing the weft through the warp is sometimes called ‘picking’ or ‘weft insertion’. Each weaver inserts weft through warp meticulously.
- Each time the weft yarn makes a pass and is pushed firmly into place, it locks together with the warp threads. This continuous over-and-under action is what builds up the woven fabric, piece by piece. This conceptually illustrates how weaving looms work.
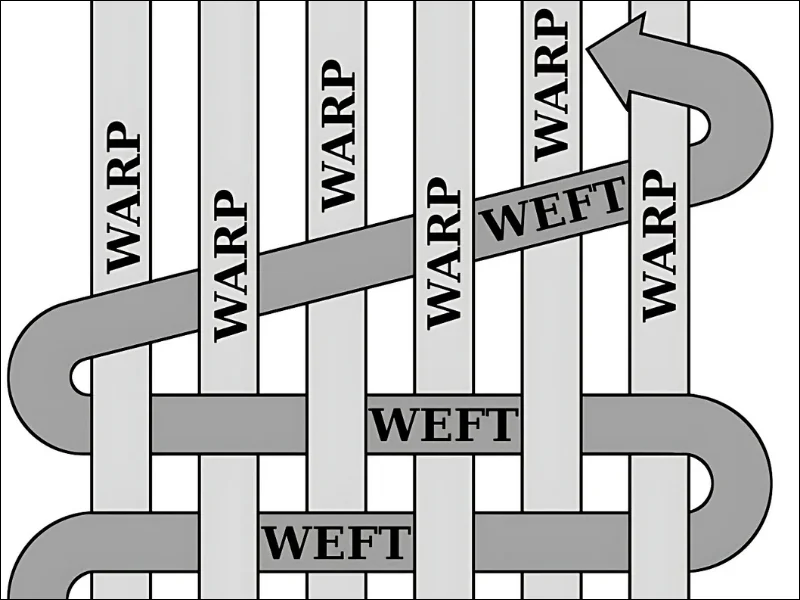
2.2 What the weft does
Weft threads have several important jobs in creating fabric structure elements:
- Builds fabric: The weft threads fill the space between the warp threads. This builds up the main body and width of the fabric. Its function forms fabric width and pattern.
- Provides structure: By weaving in and out of the warp, the weft helps give the fabric its strength and prevents it from unraveling. It creates a stable structure.
- Creates edges (selvage): As the weft thread goes across and then turns around to go back the other way, it creates the finished edges of the fabric. These edges are called the selvage.
3. How weft changes how fabric looks and feels
The characteristics of the weft thread significantly influence the final fabric.
3.1 Weft and fabric patterns
One of the coolest things about weft is how weft creates patterns in fabric. By changing the color of the weft yarns, weavers can make stripes, checks, and even highly detailed images in the fabric.
For instance, to make a fabric with blue and white stripes, the weaver would use blue weft yarn for a few rows, then switch to white weft yarn for the next few rows, and keep repeating this. The color characteristic of the weft yarn plays a big role.
The specific way the weft thread goes over and under the warp threads is called the weave structure. There are many different types of fabric weaves, and the weft’s effect on them is crucial.
Each one makes the fabric surface look and feel different. Some are smooth and flat, others might be bumpy, ribbed, or have diagonal lines. The weft’s role creates fabric pattern and texture.
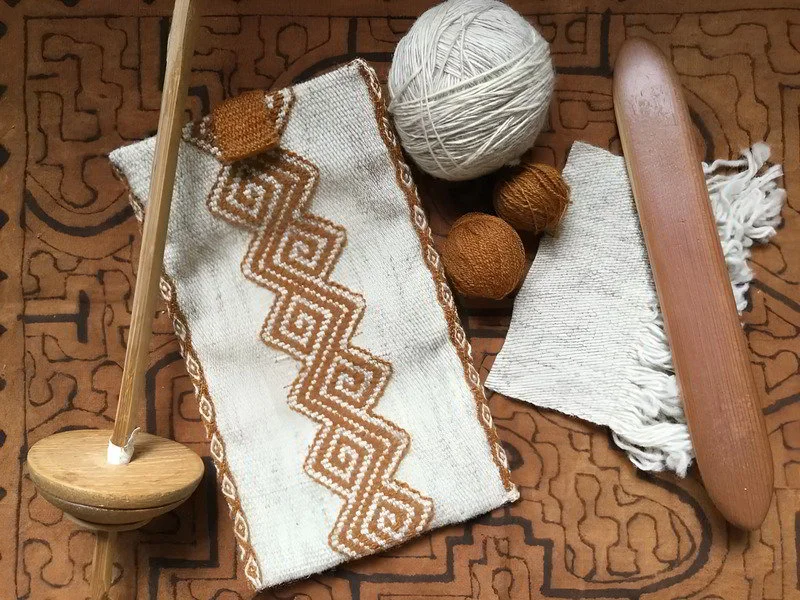
3.2 Weft and fabric feel
The kind of yarn used for the weft significantly changes how the fabric feels. For example, if the weft is made from soft cotton yarn, the fabric will feel soft.
If it’s made from shiny silk thread, the fabric might feel smooth and look luxurious. Polyester yarn is often used for wefts when you need the fabric to be strong and last a long time. At Packlove, we often use high-quality polyester yarns for our woven labels because they are durable and can create very fine details.
How close together the weft threads are packed also changes the fabric. This is related to something called thread count.
If many weft threads are packed tightly, the fabric will be dense and often feel a bit stiffer. If fewer weft threads are used and they are packed loosely, the fabric will be lighter and might hang or drape more softly.
4. Weft in everyday items
Now that you understand weft, you’ll probably start noticing its work in lots of textile things you use every day – like your clothes, towels, bed sheets, and even the fabric on your furniture. A fantastic example where weft plays a starring role is in woven labels – like the beautiful, custom labels we make right here at Packlove for clothing brands and makers. These labels are key for custom apparel branding and often involve intricate textile manufacturing knowledge, influencing fashion design.
In a woven label, very fine weft yarns are carefully woven back and forth to create your brand name, logo, or any design you want, often in amazing detail. By using different colored weft threads, even complicated images and tiny text can be woven directly into the label. This explains the role of weft in woven labels and how weft affects woven label detail.
The quality and fineness of these weft yarns are extremely important for a good-looking label. Packlove specializes in using very fine, high-quality weft yarns, often made from durable polyester yarn.
This ability to use fine weft threads for high-definition (HD) woven labels at Packlove means even small letters and complex parts of a logo look incredibly sharp and clear. At Packlove, we help you select woven labels where the weft quality ensures detailed logo reproduction. This is something we guide our customers on to make their brand look its best.
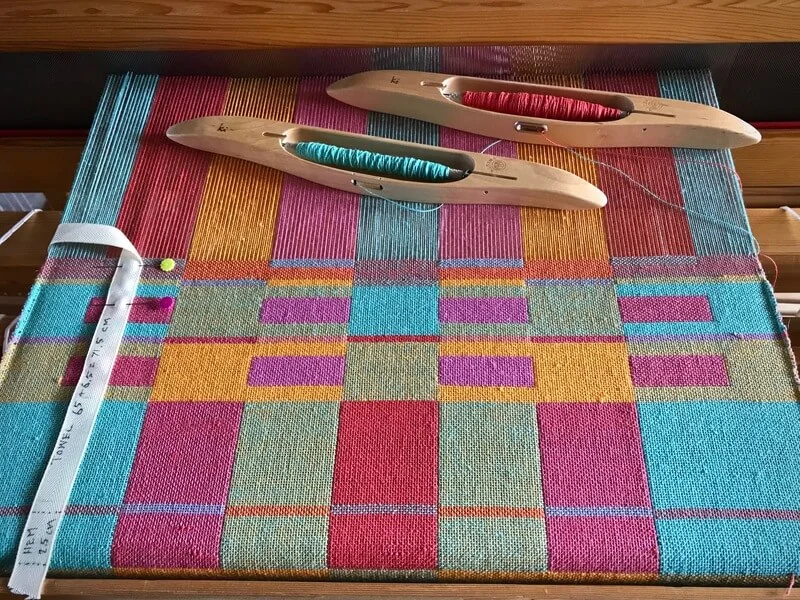
Different weft materials can also give your labels a special look and feel. For example, using a satin weft can give your label a lovely sheen, making it look more luxurious and eye-catching. We provide guidance on how different weft materials impact the sheen and feel of custom labels.
So, when you see a detailed and professional-looking woven label, remember it’s the precise weaving and quality of the weft threads that make it possible! Understanding a bit about weft helps you appreciate the craftsmanship that goes into these small but important branding details.
5. Frequently asked questions (FAQs) about weft
5.1 Is weft the same as woof?
Yes, they mean exactly the same thing! “Woof” is just an older English word for weft. You might also hear people call weft threads “filling yarn” or sometimes a “pick”.
5.2 Which is stronger, warp or weft?
Generally, the warp threads are typically made stronger. This is because they have to withstand significant stretching and tension during the weaving process. However, both warp and weft threads are crucial for the overall strength, durability, and quality of the final fabric.
5.3 Why is it called “weft”?
The word “weft” comes from a very old English word “wefan”, which simply means “to weave.” So, “weft” basically describes “that which is woven” across the warp threads to create fabric.
5.4 How does understanding weft help me if I order custom labels from Packlove?
Knowing a bit about weft helps you understand the skill and quality that goes into making great woven labels. For instance, when you want a label with very fine, clear details or rich, vibrant colors, that’s achieved through the careful selection and use of weft yarns.
Our understanding of how different weft yarns, thicknesses, and colors work allows us to advise you on the best options to make your woven labels look incredibly professional and ensure your logo and brand design are reproduced beautifully and accurately. Packlove explains weft’s role in labels to show how we use quality materials and expert techniques to create the best possible labels for your brand.
Read more:
In essence, understanding weft unlocks insight into a crucial element of textile creation. These horizontal threads, interlacing with the warp, are fundamental not only to fabric structure but also to its visual appeal, texture, and pattern.
From everyday garments to the intricate details in high-quality woven labels, like those crafted at Packlove, the weft’s role is indispensable. Appreciating the function and impact of the weft enhances your understanding of fabric quality and the artistry behind textile products, ensuring you recognize the craftsmanship in every weave.