This guide provides apparel businesses with a comprehensive understanding of nylon. Readers will learn about the material’s chemical nature, historical context, key properties relevant to clothing and accessories, common types like Nylon 6 and Nylon 6,6, the basic manufacturing process, diverse applications in apparel, environmental considerations including recycled alternatives, and answers to frequently asked questions. The information aims to help businesses make informed decisions when selecting materials for labels, tags, zippers, and garments.
1. Understanding nylon: Beyond the basics
1.1 What exactly is nylon?
Nylon refers to a family of synthetic polymers known technically as polyamides. As a synthetic material, it originates from petrochemicals, setting it apart from natural fibers like cotton or wool.
The defining feature of its chemical composition involves long molecular chains created from smaller units called monomers. These chains possess repeating amide linkages (-CONH-), which are specific chemical bonds.
Nylon polymers generally have a high molecular weight. A key characteristic is its nature as a thermoplastic, meaning the material softens upon heating and solidifies upon cooling, allowing for melt-processing into various forms. The synthetic origin from petroleum is fundamental to understanding its properties and production.
1.2 A brief history: From stockings to industrial staple
The story of nylon begins in the 1930s with the chemical company DuPont and a research team led by Wallace Carothers. This pioneering work in synthetic polymer chemistry resulted in the synthesis of Nylon 6,6 in 1935, marking the arrival of the first commercially successful synthetic thermoplastic polymer.
Initial commercial applications included nylon-bristled toothbrushes in 1938, but the material gained widespread fame with women’s stockings, introduced commercially in 1940 and quickly dubbed “nylons.” The advent of World War II dramatically shifted production towards military uses; nylon proved crucial for making parachutes, ropes, and tents, largely replacing silk due to supply disruptions and the material’s inherent strength.
Following the war, its use expanded significantly, moving beyond hosiery into broader apparel categories and numerous industrial applications, solidifying its place in the modern textile industry and marking a significant point in synthetic fiber history.
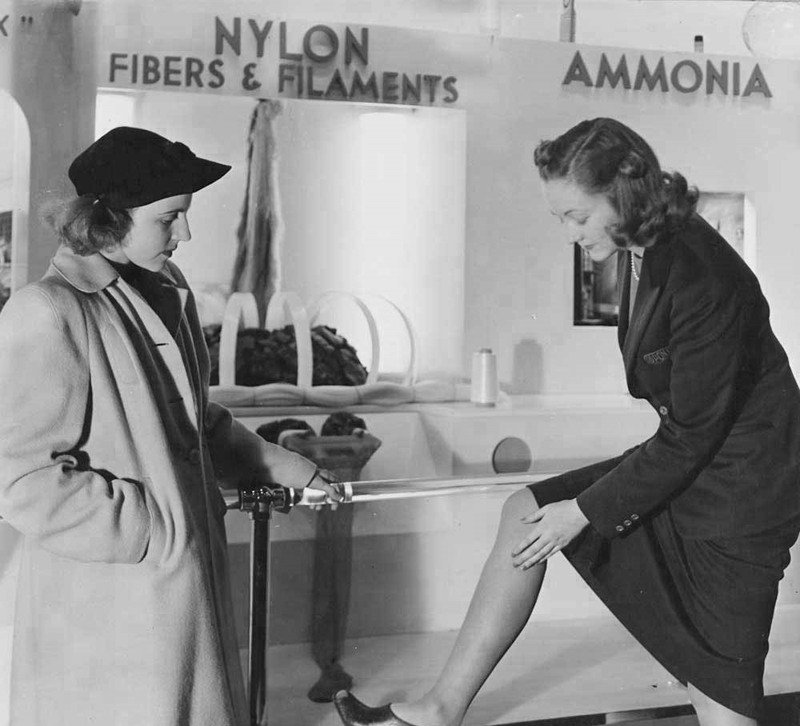
2. Key properties of nylon relevant to your apparel business
2.1 Strength and durability: Why nylon lasts
Nylon exhibits high strength, particularly tensile strength, and exceptional abrasion resistance, meaning the material withstands rubbing and wear exceptionally well. This inherent durability translates directly into longer-lasting products for apparel businesses, especially for items like labels and tags that endure frequent handling, washing, and friction.
The robust nature contributes to fewer customer complaints or returns related to material failure. The material’s toughness arises partly from its molecular structure, which allows for strong hydrogen bonding between polymer chains and the potential for regions of high crystallinity, enhancing overall wear resistance. Garment components made from nylon are known for being tough and hard-wearing.
2.2 Elasticity and resilience: Shape retention matters
A valuable property of nylon is its elasticity, the ability to stretch significantly and then return to its original dimensions. Coupled with good resilience, this means nylon materials maintain their shape well.
Shape retention is crucial for garments designed for movement and flexibility. For accessories like labels or straps, this property ensures they resist permanent distortion even when subjected to pulling or stretching during use or laundering. The process of cold drawing further enhances its stretchability and overall strength.
2.3 Appearance and texture: The look and feel
Nylon fibers can be manufactured to achieve a range of appearances, from highly lustrous to semi-lustrous or completely dull, offering aesthetic flexibility. The typical texture is smooth against the skin. A significant advantage for apparel applications is its good dyeability. The material readily accepts dyes, allowing for the creation of fabrics, labels, and tags in vibrant, lasting colors, which is essential for branding and design purposes.
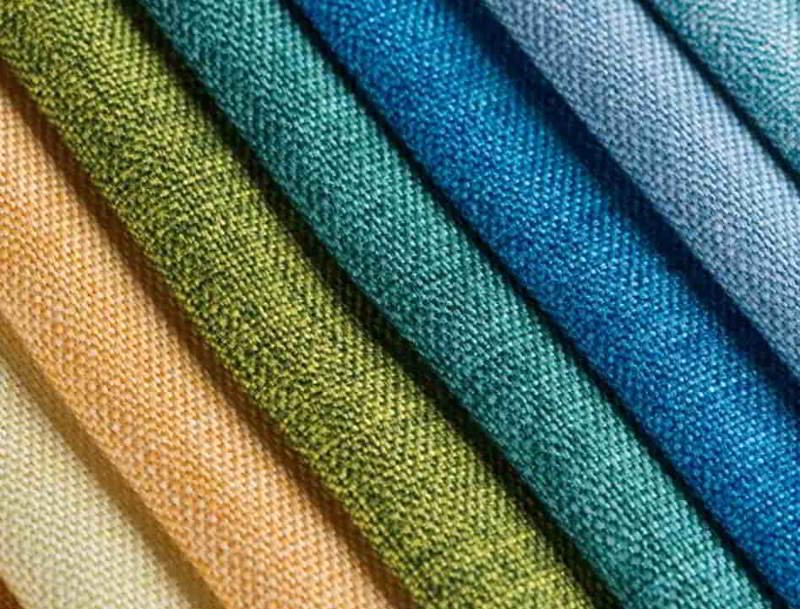
2.4 Heat resistance and melting point
Compared to some other common synthetic fibers, nylon possesses a relatively high melting point. Because of its thermoplastic nature, the material melts when exposed to sufficient heat rather than burning readily like natural fibers.
This characteristic has practical implications for garment care and manufacturing. For instance, care labels must recommend appropriate ironing temperatures to avoid melting the fabric or nylon components. Heat setting processes used in manufacturing rely on this property to impart permanent shape or pleats.
2.5 Interaction with moisture: What to expect
Nylon is described as hygroscopic, meaning its fibers absorb a certain amount of moisture from the surrounding air. While it absorbs more moisture than polyester, it takes in considerably less than natural fibers like cotton or wool.
A positive aspect of this interaction is its relatively quick drying time. However, moisture absorption can slightly alter the material’s dimensions and feel, as absorbed water can act as a plasticizer, making the material slightly more flexible.
Businesses should consider these factors regarding garment comfort and the dimensional stability of nylon labels or trims, particularly in varying humidity conditions. While often described as having good water resistance due to fiber structure and finishes, nylon itself is not inherently waterproof without specific treatments.
2.6 Other considerations: Pilling and static
Two potential downsides sometimes associated with nylon fabrics include pilling and static cling. Pilling refers to the formation of small, fuzzy balls of fiber on the fabric surface, typically caused by friction during wear or washing.
Additionally, nylon can accumulate static electricity, especially in dry environments, leading to static cling. While these factors can influence garment fabric choices, they are generally less critical considerations for standard nylon labels, tags, or zipper tapes where surface friction or prolonged skin contact is less of an issue.
3. Common types of nylon: Nylon 6 vs. Nylon 6,6
3.1 Nylon 6: Characteristics and common uses
Nylon 6 is synthesized from a single monomer called caprolactam through a process called ring-opening polymerization. Key properties of Nylon 6 include excellent dyeability, allowing for deep and vibrant colors, good elasticity and elastic recovery (returning to shape after stretching), and generally a softer feel compared to Nylon 6,6.
It has a slightly lower melting point than Nylon 6,6. Common uses span various industries, including carpeting, apparel (especially where dyeing is critical), and certain industrial applications.
3.2 Nylon 6,6: Characteristics and common uses
Nylon 6,6 is formed from two distinct monomers: hexamethylenediamine and adipic acid. Defining properties include a higher melting point than Nylon 6, greater stiffness or rigidity, and excellent abrasion resistance, making it exceptionally durable.
While it can be slightly more challenging to dye than Nylon 6, Nylon 6,6 generally offers good colorfastness once dyed. Common uses leverage its strength and durability, including performance apparel, industrial parts like gears, tire cords, and frequently, robust printed or woven tags and labels for garments requiring high wear resistance.
Feature | Nylon 6 | Nylon 6,6 |
---|---|---|
Monomer(s) | Caprolactam | Hexamethylenediamine & Adipic Acid |
Melting Point | High (approx. 220°C / 428°F) | Higher (approx. 265°C / 509°F) |
Stiffness | Good | Higher |
Dyeability | Excellent | Good |
Abrasion Resistance | Good | Excellent |
3.3 Briefly mentioning other types
Beyond the widely used Nylon 6 and Nylon 6,6, a broader family of nylons exists, often referred to as specialty nylons. Examples include Nylon 11, Nylon 4,6, and Nylon 12. These variations offer different property profiles.
For instance, Nylon 12 is known for its lower moisture absorption compared to Nylon 6 or 6,6, along with greater flexibility and chemical resistance, suiting it for specific technical applications like tubing or specialty films. Awareness of these other types highlights the versatility within the polyamide family.
Selecting the appropriate nylon type depends on the specific requirements of the label, tag, or accessory. For printed tags and care labels that demand high durability, stiffness, and resistance to heat during garment finishing processes like pressing, Nylon 6,6 is often the preferred choice due to its higher melting point and excellent abrasion resistance.
Nylon 6 might be suitable for softer woven labels where exceptional dye uptake for intricate designs is paramount, or for applications where maximum softness is desired. The printing method and attachment technique should also factor into the decision.
For accessories like webbing for straps or tapes used in zipper bags, the strength and wear resistance of nylon (often Nylon 6,6) make it a reliable material. Providing expert recommendations tailored to the end-use ensures optimal performance and longevity of these essential components. Consideration of application suitability is key.

4. How nylon is made: A simplified overview
The nylon production or manufacturing process generally follows these basic steps in synthetic fiber manufacturing:
- Monomer extraction: The essential chemical building blocks, like adipic acid and hexamethylenediamine for Nylon 6,6, or caprolactam for Nylon 6, are derived from petroleum.
- Polymerization: These monomers are reacted together under controlled conditions to form long polymer chains. This reaction creates the polyamide, often initially as a “nylon salt” which is then further processed.
- Melting: The solid nylon polymer chips are heated above their melting point to create a thick, viscous liquid.
- Extrusion: The molten polymer is forced through a device called a spinneret, which has many tiny holes. As the liquid polymer emerges from the holes, the liquid forms continuous filaments.
- Drawing: The solidified filaments are then stretched, often over heated rollers. This drawing process aligns the polymer molecules parallel to the fiber axis, significantly increasing the fiber’s strength, elasticity, and crystallinity.
- Winding: Finally, the drawn filaments are wound onto spools or bobbins, ready for subsequent processing into yarn, fabric, or other forms.
5. Nylon in apparel: More than just fabric
5.1 Common garment applications
Nylon fabric finds widespread use in various types of apparel. Historically famous for hosiery and stockings, it remains a key fiber in this category. It is also prevalent in activewear and sportswear due to its strength, elasticity, and abrasion resistance.
Swimwear frequently utilizes nylon for its quick-drying properties and stretch. Outerwear garments like jackets and ponchos often incorporate it for wind and water resistance. Lingerie benefits from its smooth texture and strength.
Furthermore, nylon is frequently used in blended fabrics, combined with fibers like cotton, spandex, or polyester to achieve specific performance characteristics, such as enhancing durability or adding stretch to a clothing fabric.
Beyond the main garment fabric, nylon plays a vital role in essential apparel accessories and trims. Common applications include:
- Printed care labels: Often made from nylon taffeta due to its smooth surface for printing, durability through washing, and heat resistance.
- Woven brand labels: Nylon threads contribute durability and a slight sheen to woven labels.
- Hang tags: While the tag itself might be cardstock, the strings or cords used for attachment are frequently made of strong nylon. Sometimes, durable plastic hang tags are themselves molded from it.
- Zippers: The fabric tape alongside the zipper teeth is commonly woven from nylon for strength and smooth operation. Zipper teeth themselves can also be molded from nylon plastic.
- Drawstrings and cords: Used in hoods, waistbands, or bags, these often utilize braided or woven nylon cordage for strength and durability.
- Ribbons and webbing: Decorative ribbons or functional webbing (e.g., for backpack straps, belt loops) frequently employ nylon.
- Reinforcement: Small pieces of nylon fabric may be used internally to reinforce stress points in garments.
- Poly mailers: While less common than polyethylene (PE), some durable poly mailers might incorporate nylon, though PE remains dominant for this application.
These industrial applications within the apparel context highlight its versatility beyond just the main fabric.
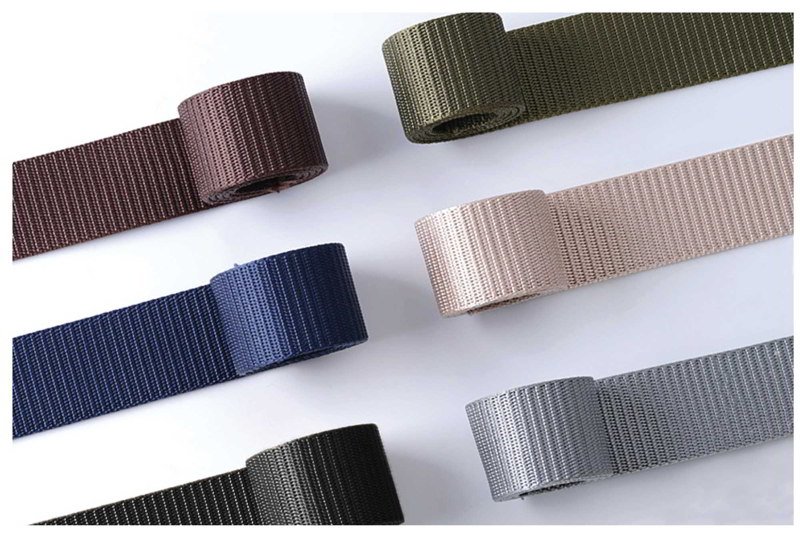
6. Nylon and the environment: Considerations for your brand
6.1 The environmental footprint of nylon production
Traditional nylon production presents several environmental challenges. A primary concern is its reliance on fossil fuels, specifically petroleum, as the source for its core chemical components. Petroleum is a non-renewable resource, and its extraction and processing contribute to resource depletion.
The manufacturing process itself demands significant energy consumption. Furthermore, the production of certain nylon precursors, notably adipic acid used for Nylon 6,6, can release nitrous oxide (N2O), a potent greenhouse gas, into the atmosphere. High water usage, mainly for cooling during manufacturing, also adds to the environmental impact.
6.2 Biodegradability and waste issues
A major end-of-life issue for nylon is that it is non-biodegradable. Conventional nylon materials do not readily decompose in natural environments, persisting in landfills for potentially hundreds of years. This contributes significantly to plastic pollution. Another concern is the generation of microplastics.
Through washing clothes containing nylon fibers or the gradual breakdown of larger nylon items discarded in the environment, tiny plastic particles are released. These microplastics contaminate soil, waterways, and oceans, posing risks to ecosystems and potentially entering the food chain. Ocean debris containing nylon is a substantial problem.
6.3 Recycled nylon (Econyl): A more sustainable option?
In response to environmental concerns, recycled nylon offers a more sustainable alternative. Materials marketed under names like Econyl represent nylon produced from pre-consumer (industrial scraps) and post-consumer waste.
Common feedstocks include discarded fishing nets recovered from oceans, used carpets, and fabric scraps. The recycling process transforms this waste back into high-quality nylon yarn. The key benefits include diverting significant waste from landfills and oceans, reducing the demand for virgin petroleum resources, and generally having a lower carbon footprint and reduced energy consumption compared to virgin nylon production.
While recycled nylon represents a positive step towards a closed loop system and circular economy considerations, acknowledging that the end material is still nylon is important. Recycled nylon provides a better, though not perfect, option for brands seeking sustainable alternatives.
7. Related questions
7.1 Is nylon waterproof?
Nylon fiber itself is not inherently waterproof; it is actually hygroscopic, meaning it absorbs a small amount of water. However, it dries relatively quickly. Fabrics made from tightly woven nylon yarns can exhibit good water-resistance, causing water to bead up and roll off initially, especially if treated with a water-repellent finish.
To achieve true waterproof performance, nylon fabrics typically require a special coating or membrane layer. Therefore, a distinction exists between water-resistant and waterproof.
7.2 Does nylon shrink when washed?
Generally, nylon possesses good dimensional stability and is resistant to shrinking, particularly when compared to natural fibers like cotton or wool. If care instructions are followed, especially regarding washing temperature, significant shrinkage is unlikely.
However, exposing nylon garments or accessories to excessively high heat during washing or drying can potentially cause some shrinkage or damage the fibers. Adhering to recommended care guidelines, which usually specify cool or warm water and low heat drying, helps maintain its shape and size.
7.3 Can nylon labels be printed on easily?
Yes, nylon is very well-suited for printed labels and is a common material choice, particularly for care labels. Materials like nylon taffeta offer a smooth, consistent surface that readily accepts print using methods like thermal transfer printing.
The resulting print is typically durable and able to withstand repeated washing and wear. Its combination of printability, durability, and heat resistance makes nylon labels a practical option for apparel businesses needing reliable garment identification and care instructions.
Both nylon and polyester are durable synthetic fibers frequently used for tags and labels in apparel. Choosing between them involves considering subtle differences. Nylon often provides a slightly softer hand-feel and generally boasts superior abrasion resistance.
Polyester typically exhibits lower moisture absorption, meaning it dries even faster and is less affected by humidity changes. It also tends to have better resistance to stretching and shrinking than nylon, and superior UV resistance, making it less prone to fading from sunlight exposure.
The best choice for tags depends on the specific priorities – whether softness and abrasion resistance (nylon) or moisture management, dimensional stability, and UV resistance (polyester) are more critical for the application.
Read more:
Nylon stands out as a highly versatile synthetic polyamide, valued for its exceptional strength, durability, and elasticity. These key benefits make it suitable for a wide array of apparel applications, extending beyond fabrics to essential business supplies like labels, tags, ribbons, and zipper components.
Understanding the property differences between common types, such as Nylon 6 and Nylon 6,6, allows businesses to select the most appropriate variant for specific needs, balancing factors like heat resistance, dyeability, and stiffness.
While appreciating its functional advantages, awareness of the environmental considerations associated with its production and disposal is crucial. Exploring options like recycled nylon presents an opportunity to mitigate some environmental impact.
For expert guidance on selecting the right nylon labels, tags, and accessories for your brand, contact Packlove. We’ll help you find the perfect solution to match your product’s quality and performance needs.