Polyethylene (PE) is a widely utilized thermoplastic in manufacturing, especially for packaging solutions like poly mailers and zipper bags crucial for clothing businesses.
Within the PE family, high-density polyethylene (HDPE) and low-density polyethylene (LDPE) are two prominent variants. Understanding the distinctions between these materials is essential for selecting the optimal packaging for your products.
This article will delve into the characteristics of both HDPE and LDPE, comparing their physical properties, chemical resistance, recyclability, and production methods to guide businesses in making informed decisions tailored to their specific requirements.
1. Understanding polyethylene and its variants: HDPE vs. LDPE
Polyethylene (PE) stands as one of the most common plastics globally, valued for its versatility and cost-effectiveness. A thermoplastic polymer (a plastic material that becomes moldable at a certain elevated temperature and solidifies upon cooling), PE finds extensive use in packaging, including films, bottles, containers, and importantly for the apparel industry, poly mailers and bags. The two primary forms relevant to packaging are high-density polyethylene (HDPE) and low-density polyethylene (LDPE).
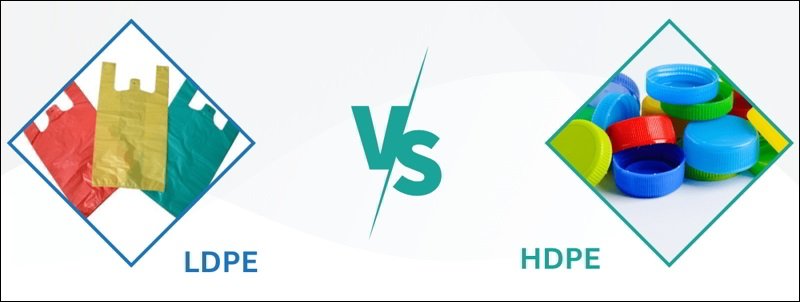
1.1 High-density polyethylene (HDPE)
HDPE is characterized by its linear molecular structure with minimal branching, resulting in a denser material (typically 0.941 g/cm³ or higher). This structure imparts significant rigidity and tensile strength.
Key characteristics: Strong, opaque, good resistance to impacts and chemicals, withstands higher temperatures compared to LDPE.
Common applications: Milk jugs, detergent bottles, shampoo containers, toys, pipes, and some types of heavier-duty bags or liners where puncture resistance is paramount. For clothing businesses, HDPE might be considered for bulk packaging containers or highly durable protective layers, though less common for individual mailers.
Advantages:
- Excellent moisture barrier properties.
- Good chemical resistance (resists many acids, bases, and solvents).
- Higher strength-to-density ratio.
- More rigid and durable.
Disadvantages:
- Less flexible than LDPE.
- Generally opaque or translucent, not typically clear.
- Can be susceptible to stress cracking under certain conditions.
1.2 Low-density polyethylene (LDPE)
In contrast, LDPE possesses a molecular structure with significant branching. These branches prevent the molecules from packing closely together, leading to a lower density (typically 0.910–0.940 g/cm³) and greater flexibility.
Key characteristics: Flexible, often transparent, good toughness, good moisture barrier, chemically inert (non-reactive).
Common applications: This material is frequently used for plastic films, grocery bags, trash bags, food wraps, and crucially for apparel businesses, poly mailers, garment bags, and zipper bags. Its flexibility and relative clarity make LDPE suitable for packaging individual clothing items.
Advantages:
- Highly flexible and easy to stretch.
- Good clarity allows product visibility.
- Excellent moisture resistance.
- Relatively inexpensive and easy to process.
- Good impact resistance at lower temperatures.
Disadvantages:
- Lower tensile strength compared to HDPE.
- Lower temperature resistance; can warp or melt at lower temperatures than HDPE.
- More permeable to gases like oxygen and carbon dioxide.
- Lower chemical resistance than HDPE for some substances.
2. Comparative analysis: HDPE vs. LDPE
Choosing between HDPE and LDPE for packaging, such as poly mailers or zipper bags for clothing, depends heavily on the specific requirements of the application. A direct comparison highlights their distinct advantages.
Feature | High-Density Polyethylene (HDPE) | Low-Density Polyethylene (LDPE) | Relevance for Clothing Packaging |
---|---|---|---|
Density | Higher (≥0.941 g/cm³) | Lower (0.910–0.940 g/cm³) | Affects weight, rigidity, and material usage. |
Strength | Higher tensile strength | Lower tensile strength | HDPE offers better puncture/tear resistance; LDPE is often sufficient. |
Flexibility | More rigid | More flexible, stretchable | LDPE’s flexibility is ideal for conforming mailers and bags. |
Transparency | Translucent to opaque | Can be transparent | LDPE allows product visibility; HDPE obscures contents. |
Temp resistance | Higher | Lower | Important if packages face extreme temperatures during transit/storage. |
Moisture barrier | Excellent | Good to excellent | Both offer good protection against moisture. |
Chemical resist. | Generally better | Good, but less broad | Less critical for typical clothing items, relevant for specialty inks. |
Recycling code | #2 | #4 | Affects disposal options and consumer perception. |
2.1 Physical properties
- Strength and rigidity: HDPE’s tightly packed molecular structure gives superior tensile strength (resistance to breaking under tension) and rigidity compared to LDPE. While this makes HDPE more puncture-resistant, LDPE’s flexibility is often preferred for standard apparel poly mailers as it provides sufficient durability for typical shipping stresses while conforming easily to the shape of the contents.
- Flexibility: The branched structure of LDPE makes significantly more flexible and easier to stretch. This characteristic is advantageous for garment bags and mailers that need to accommodate various shapes and sizes without tearing easily at folds or corners.
- Transparency: LDPE can be manufactured with high clarity, allowing customers or handlers to see the contents without opening the package. HDPE is naturally milky or opaque, which can be desirable if concealing the contents is a priority.
- Temperature resistance: HDPE can withstand higher temperatures before softening (around 120°C or 248°F for short periods) compared to LDPE (around 80°C or 176°F). While relevant in some storage or shipping conditions, standard transit environments rarely exceed LDPE’s tolerance for apparel packaging.
2.2 Chemical resistance
Both materials resist many common chemicals, acids, and bases, making them suitable for containing dyed or treated fabrics without degradation. HDPE generally offers broader resistance, particularly to certain solvents and oils, though this enhanced resistance is rarely a deciding factor for standard clothing packaging unless specialty items or unique printing inks requiring harsh solvents are involved.
2.3 Recyclability and environmental impact
Both HDPE and LDPE are recyclable thermoplastics. HDPE is collected under the recycling code #2, while LDPE falls under code #4. Curbside recycling programs for #4 plastics (films and bags) can be less common than for #2 (rigid containers), although store drop-off programs for LDPE films are widespread in regions like the US.
Choosing materials with clear recycling instructions can align with business sustainability goals and appeal to environmentally conscious consumers. Consider sourcing options that incorporate post-consumer recycled (PCR) content for either material type to further reduce environmental footprint.
Read more:
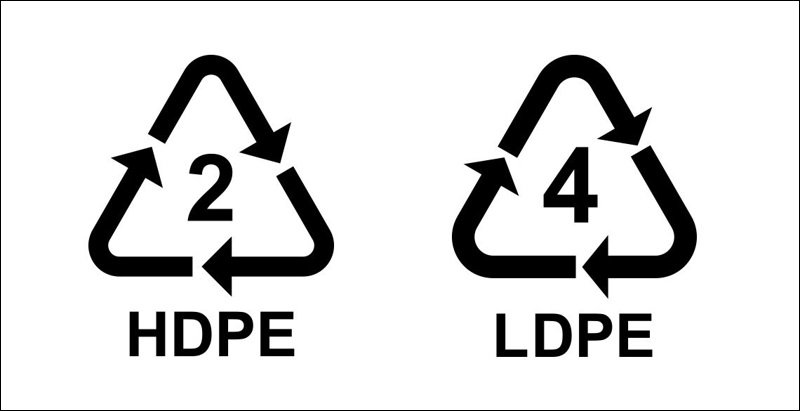
2.4 Production methods and cost implications
Both HDPE and LDPE are processed using similar techniques like extrusion (pushing melted plastic through a die to create films or shapes). However, the specific processing conditions differ slightly. Generally, LDPE film production can be slightly less energy-intensive due to lower processing temperatures.
Raw material costs fluctuate, but LDPE is often marginally less expensive or comparable in price to HDPE for film applications like poly mailers. Factors like film thickness (gauge), additives (like slip agents or UV inhibitors), and order volume will significantly impact the final cost more than the base resin choice in many cases.
Thinner gauge LDPE can often provide adequate protection for clothing at a lower material cost and weight compared to a similarly protective, but more rigid, HDPE bag.
3. Applications in clothing packaging: Choosing the right PE
Selecting the appropriate polyethylene material is crucial for ensuring garments are protected during transit and storage while meeting brand presentation and cost objectives. Based on the characteristics discussed, low-density polyethylene (LDPE) emerges as the most common and often most practical choice for standard apparel packaging needs.
3.1 Poly mailers and garment bags: The case for LDPE
For typical clothing items like shirts, pants, dresses, and accessories, LDPE offers an optimal balance of properties:
- Flexibility: LDPE’s inherent flexibility allows poly mailers to conform easily to the shape of the enclosed garments, minimizing excess volume and potentially reducing shipping costs based on dimensional weight. This flexibility also reduces stress concentration at folds, decreasing the likelihood of tears during handling compared to a more rigid material.
- Sufficient protection: While not as puncture-resistant as HDPE on a thickness-for-thickness basis, standard gauge LDPE poly mailers provide adequate protection against dirt, moisture, and minor abrasions encountered during typical shipping processes. For most apparel items, the extreme rigidity and puncture resistance of HDPE are often unnecessary.
- Clarity options: LDPE films can be produced with excellent clarity, allowing for product visibility if desired. Opaque versions are also readily available if concealing the contents is preferred.
- Cost-effectiveness: LDPE is generally cost-competitive, and its ability to be used in thinner gauges while still providing adequate protection makes it an economical choice for high-volume mailer usage.
- Printability: LDPE surfaces readily accept printing, allowing for branding and customization of mailers and bags.
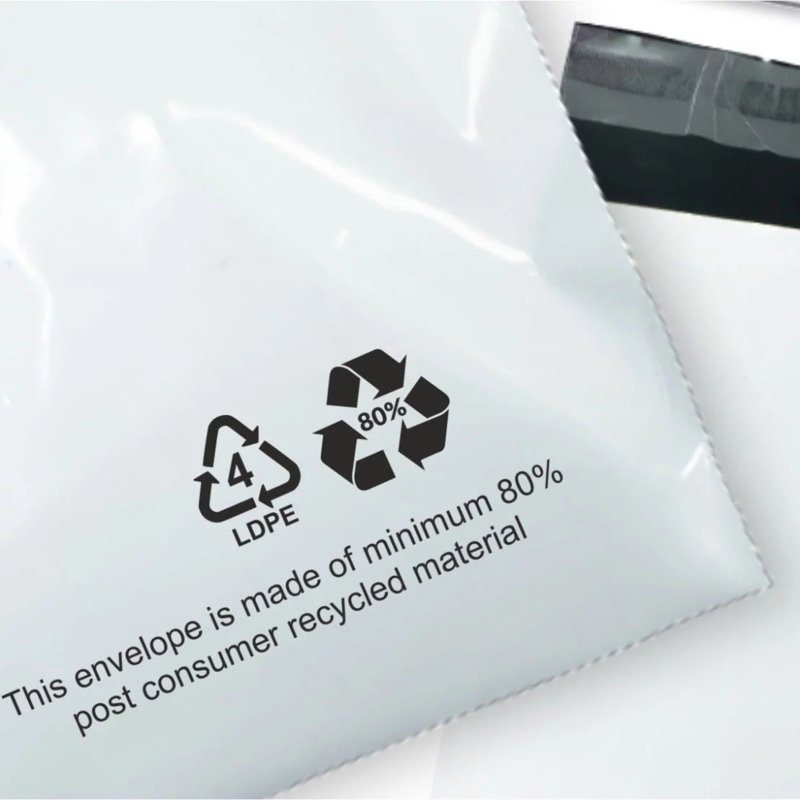
3.2 When might HDPE be considered?
While less common for individual clothing mailers, high-density polyethylene (HDPE) could be considered in specific situations:
- Heavy or sharp items: If packaging unusually heavy garments or items with sharp embellishments (like certain types of belts or heavily studded jackets), the superior puncture and tear resistance of HDPE might offer necessary extra protection.
- Extreme durability requirements: For shipments facing particularly harsh transit conditions or requiring long-term, durable storage solutions where rigidity is an asset, HDPE bags could be an option.
- Opacity is essential: If complete opacity is a primary requirement and standard opaque LDPE options are insufficient, HDPE’s naturally opaque nature might be preferred.
- Specific barrier needs: Although unlikely for standard clothing, if an item requires enhanced protection against specific chemicals or gases beyond what LDPE offers, HDPE’s properties could be beneficial.
3.3 Zipper bags for apparel
Zipper bags used for packaging individual items (like t-shirts for retail display or multi-packs) predominantly utilize LDPE. Its flexibility makes the bag easy to handle, open, and re-close. The clarity of LDPE is often advantageous for displaying the product within.
While HDPE could technically be used, its rigidity would make the bag less pliable and potentially less user-friendly for this type of application. Thicker, more rigid HDPE zipper bags might be found in industrial or hardware contexts but are less common for clothing.
Ultimately, for the vast majority of clothing businesses shipping standard apparel items, LDPE provides the best combination of flexibility, adequate protection, customization options, and cost-effectiveness for poly mailers and garment bags.
Assessing the specific weight, shape, and fragility of the items being shipped, alongside budget considerations and desired presentation (clear vs. opaque), will guide the final decision. Consulting with packaging suppliers can also provide tailored recommendations based on detailed product needs and shipping volumes.
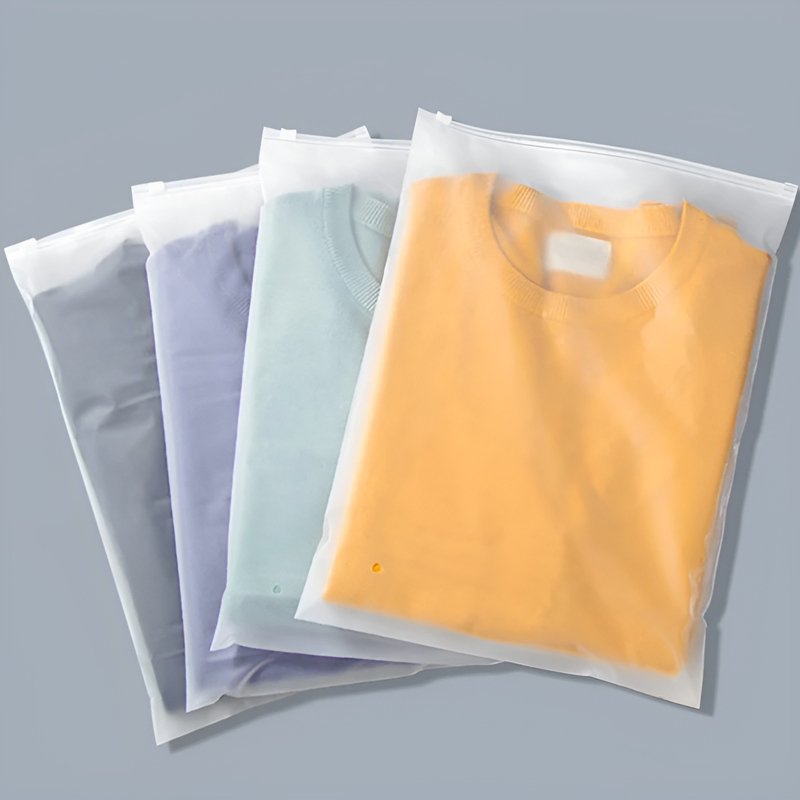
Read more:
Understanding the fundamental differences between high-density polyethylene (HDPE) and low-density polyethylene (LDPE) empowers clothing businesses to make strategic packaging choices. While both are versatile thermoplastics derived from the same monomer (ethylene), their distinct molecular structures lead to significantly different physical properties.
HDPE, with its linear chains and higher density, offers greater rigidity, tensile strength, and resistance to higher temperatures and certain chemicals. However, this comes at the cost of reduced flexibility and natural opacity.
Conversely, LDPE’s branched structure results in lower density, granting superior flexibility, stretchability, and potential for transparency, albeit with lower strength and temperature resistance compared to HDPE.
By carefully considering these factors, clothing businesses can select the polyethylene packaging solution that best protects their products, aligns with their operational budget, and meets customer expectations.