Moving from a single successful sample to full-scale production presents a significant hurdle for many small clothing businesses: achieving consistent sizing across an entire size range. Inconsistent fit can frustrate customers, lead to increased returns, and damage your brand’s reputation.
Mastering professional size grading (the process of scaling a base pattern to different sizes) is therefore crucial for customer satisfaction, efficient manufacturing, and ultimately, sales success. This guide will equip you with the essential knowledge of what size grading entails, why accurate apparel sizes are vital, the methods used, how to apply grade rules effectively, and how to integrate this process into your production workflow.
1. What exactly is size grading in apparel?
1.1 Defining size grading: more than just resizing
Size grading is the systematic process used in apparel production to proportionally increase or decrease a perfected base size pattern (the initial pattern developed in a specific sample size, like Medium) to create a complete size range (e.g., XS, S, M, L, XL).
Crucially, this is not simply making everything uniformly bigger or smaller. Effective size grading applies specific increments based on established principles of how human bodies change proportionally between sizes. This ensures the original design intent, fit characteristics, and style lines are maintained across all sizes offered. The goal is a consistent fit experience for every customer, regardless of the size they purchase.
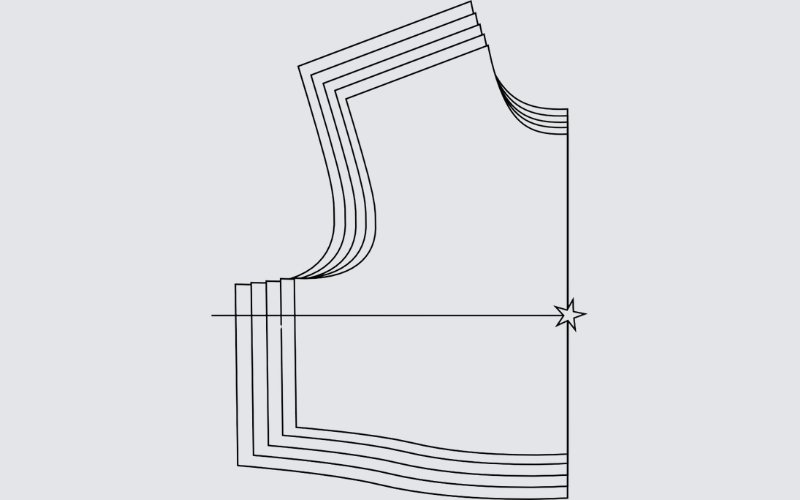
1.2 Why consistent garment fit through grading is non-negotiable for clothing brands
Implementing proper size grading practices is fundamental for several key business reasons:
- Ensures consistent garment fit across the entire size range, meeting customer expectations.
- Significantly reduces customer returns stemming from poor or unpredictable sizing.
- Builds brand trust and fosters customer loyalty; buyers feel confident purchasing knowing the fit will be reliable.
- Is essential for efficient apparel production, providing clear specifications for manufacturers and minimizing errors.
- Allows brands to cater effectively to a broader customer base by offering a comprehensive and well-fitting size range.
1.3 Clearing confusion: size grading vs. pattern alteration
While both involve changing patterns, size grading and pattern alteration serve distinct purposes:
Size Grading: Focuses on creating multiple standard sizes for production. Changes are applied systematically to all relevant measurement points across the pattern based on pre-defined formulas (grade rules) to maintain the garment’s overall proportions and intended fit style across the size range.
Pattern Alteration: Involves changing specific points or areas on a pattern (usually the base size) to address individual fit issues or achieve a custom fitting. Examples include performing a Full Bust Adjustment (FBA), lengthening a sleeve, or adjusting the rise on trousers for a particular person or fit model. The goal is not to create a standard size range but to perfect the fit for one specific instance or correct a design flaw.
Feature | Size Grading | Pattern Alteration |
---|---|---|
Purpose | Create a range of standard sizes for production | Achieve custom fitting or fix specific issues |
Scope of Change | All relevant points changed proportionally | Specific points/areas adjusted |
Outcome | Full size range (S, M, L, etc.) | Adjusted pattern for one size/individual |
Applies To | Base pattern to create multiple sizes | Usually the base pattern or individual pattern |
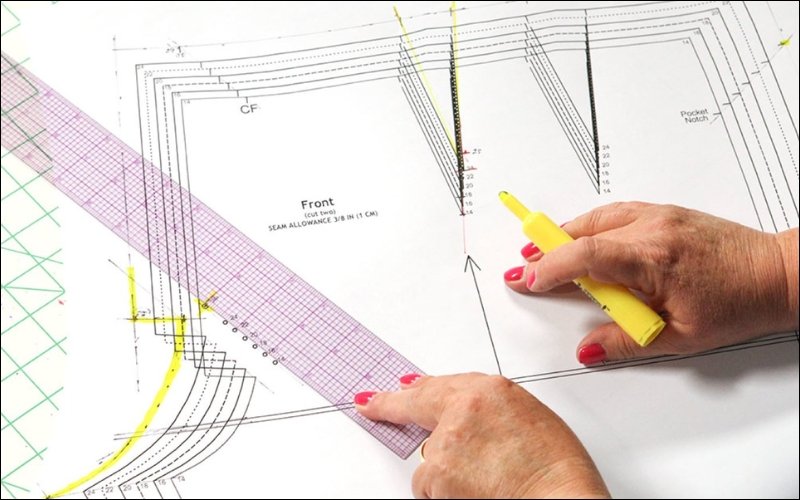
2. The building blocks: Understanding grade rules and measurement specs
2.1 Decoding grade rules: The formula for size changes
Grade Rules are the core formulas dictating how a pattern grows or shrinks between sizes. They specify the exact amounts, known as grading increments, that are added or subtracted at each key measurement point on the pattern.
These increments are not arbitrary; they are carefully calculated to reflect average body proportions and how different areas of the body change relative to each other (for example, the chest circumference typically increases more significantly between sizes than the neck width).
Brands either develop their own proprietary grade rules based on their target customer or adopt established industry-standard rule libraries to achieve consistent size changes.
2.2 Identifying key points of measurement (POMs)
Points of Measurement (POMs) are precisely defined locations on a garment where specific garment dimensions are taken. These measurements provide the quantitative data needed for grading and quality control. Establishing clear POMs is essential for creating accurate specification sheets (spec sheets) and ensuring consistency between the designer’s intent and the factory’s output. Common POMs for a basic T-shirt include:
- Chest Width (measured 1″ below armhole)
- Waist Width
- Bottom Opening/Sweep Width
- Body Length from HPS (High Point Shoulder)
- Sleeve Length (from shoulder seam)
- Across Shoulder (seam to seam)
- Armhole (measured straight or curved)
- Neck Width (seam to seam)
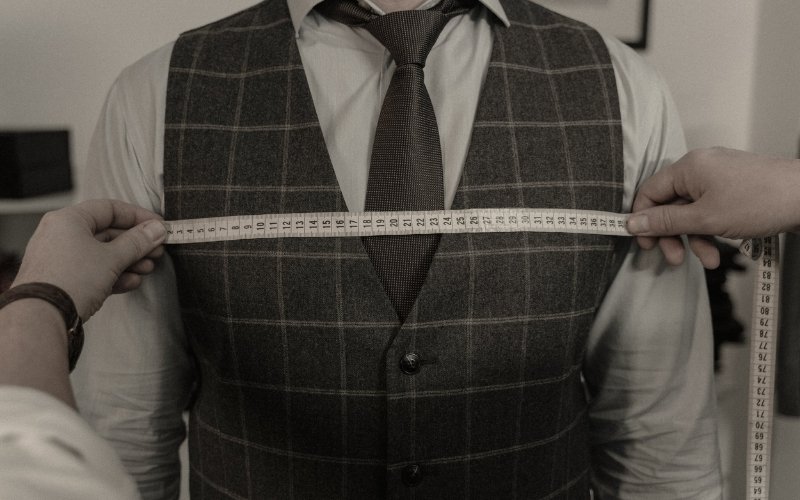
2.3 Creating your graded measurement specification sheet
The Graded Measurement Specification Sheet, often shortened to Graded Specs or referred to as a Size Specification Sheet, is a critical document that tabulates the target measurement for every defined POM across the entire size range.
This chart is created by applying the chosen grade rules to the approved base size measurements. For instance, if the base size Medium T-shirt has a chest measurement of 20 inches and the grade rule dictates a 1-inch increase per size (flat measurement), the Large would spec at 21 inches, and the Small at 19 inches. This sheet becomes an integral part of the Tech Pack, communicating precise dimensions to manufacturers.
Point of Measurement (POM) | S | M | L | Tolerance |
---|---|---|---|---|
Chest Width (1″ below armhole) | 19″ | 20″ | 21″ | +/- 1/2″ |
Body Length from HPS | 27″ | 28″ | 29″ | +/- 1/2″ |
Sleeve Length from Shoulder | 7.5″ | 8″ | 8.5″ | +/- 1/4″ |
Across Shoulder | 17″ | 18″ | 19″ | +/- 1/4″ |
2.4 A practical look at tolerances: allowing for minor manufacturing variations
Measurement tolerance refers to the acceptable deviation (+/-) from the target measurement listed on the spec sheet. Tolerances are a practical necessity in garment manufacturing because achieving exact dimensions on every single piece is unrealistic due to inherent manufacturing variations.
Factors like fabric stretchiness, slight differences in sewing machine tension, cutting variations, and the human element in handling materials mean minor discrepancies will occur. For example, a spec sheet might list a chest measurement of 20″ with a tolerance of +/- 1/2 inch, meaning any garment measuring between 19.5″ and 20.5″ at that POM is considered within the acceptable range.
Tolerance levels depend on the brand’s quality standards, the garment type, and the specific POM.
3. How is size grading done? Common methods & choosing yours
3.1 Traditional routes: manual pattern grading techniques
The cut and spread method
The Cut and Spread method is a form of manual pattern grading. This technique involves strategically cutting the base pattern along predetermined lines. These pattern pieces are then spread apart (to increase size) or overlapped (to decrease size) by amounts dictated by the grade rule amounts.
Finally, the new outline is traced onto fresh paper, smoothing curves and ensuring seam lines match. Basic tools like rulers, scissors, and paper are sufficient, but requires careful execution.
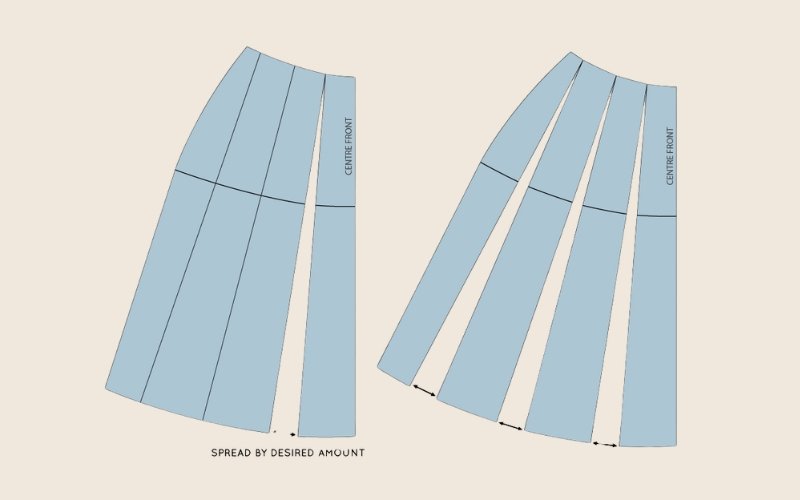
The pattern shifting method
Another manual pattern grading technique is the Pattern Shifting method. With this approach, the base pattern is placed on paper, and key points are shifted outwards or inwards, upwards or downwards according to the grade rules. The entire pattern outline is then retraced using these shifted points to create the new size. Specialized grading rulers can aid in maintaining accuracy during the shifting process.
3.2 The modern approach: digital pattern grading
Advantages for efficiency and accuracy in apparel manufacturing
Digital Pattern Grading, also known as Computer Grading, utilizes specialized CAD software (Computer-Aided Design) to perform the grading process electronically. This method offers significant advantages, especially for commercial apparel manufacturing:
- Speed and Efficiency: Digitally grading patterns, particularly complex ones or those with extensive size ranges, is substantially faster than manual methods.
- High Accuracy and Consistency: CAD software applies grade rules precisely, minimizing human error and ensuring consistency across all sizes.
- Easy Modification and Storage: Digital patterns are easily stored, retrieved, and modified if adjustments are needed.
- Integration: Digital patterns integrate seamlessly with automated cutters, plotters, and other modern apparel manufacturing technologies.
- Industry Standard: Most professional factories and pattern makers now primarily use computer grading.
3.3 Manual vs. digital: selecting the right grading method for your business
Choosing the appropriate grading method depends on several factors relevant to small business needs:
Manual grading:
- Pros: Lower initial investment if performed in-house (though time is a cost), potentially suitable for very simple styles or extremely small production runs.
- Cons: Time-consuming, requires skilled hands for accuracy, prone to inconsistencies, difficult for complex patterns, not compatible with most modern factory workflows.
Digital grading:
- Pros: Essential for efficient size scaling, yields high accuracy and consistency, easily shared with factories, industry standard, better for complex designs.
- Cons: Requires investment in software or outsourcing costs (which is common for small businesses), necessitates digital pattern files.
For most small businesses aiming for professional production and growth, digital grading (often outsourced to a specialist or service provider) is the recommended approach due to its efficiency, accuracy, and compatibility with apparel manufacturing partners, despite the initial or ongoing cost. The required volume and complexity of garments also heavily influence this decision.
4. Integrating size grading into your production pattern workflow
4.1 The importance of your base size / sample size selection
The foundation of accurate grading lies in the perfection of the Base Size pattern, which is typically the Sample Size used for initial fittings and approvals. The fit, proportions, and measurements of all subsequent graded sizes directly depend on the quality of this base pattern.
Therefore, it is absolutely critical to conduct thorough fit testing and make all necessary adjustments to finalize the base size before commencing the grading process. Any fit issues present in the base size will be amplified across the entire size range. Ideally, the base size should represent the middle of your target size range (e.g., Medium in an S-M-L range) or reflect the measurements of your core customer profile.
4.2 How grading fits into your tech pack
The Graded Measurement Specification Sheet is a non-negotiable component of a comprehensive Tech Pack (Technical Package). The Tech Pack serves as the master blueprint for your garment, containing all necessary details for production.
Including the graded specs ensures that the pattern maker and the factory have the exact target dimensions for every size you intend to produce. This standardized communication minimizes misunderstandings and errors, ensuring everyone involved in production is working from the same set of precise instructions for factory communication.
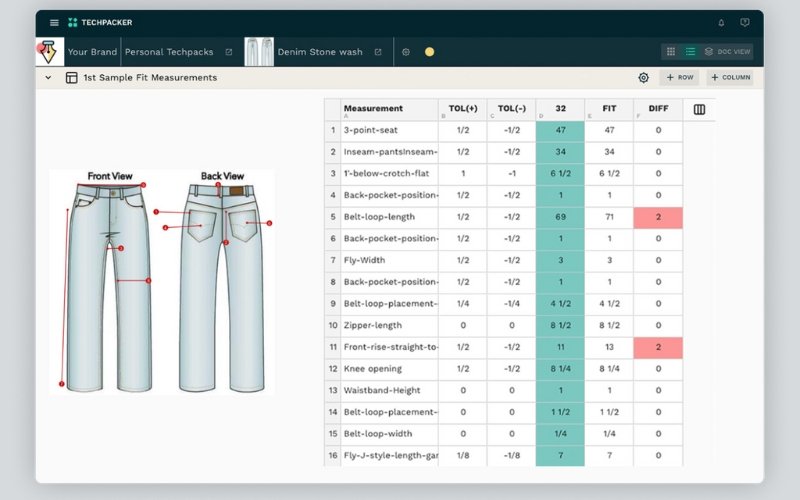
4.3 Collaborating effectively: working with pattern makers and factories on grading
For small businesses often outsourcing pattern making and grading, clear communication with external partners is key. Here are tips for effective collaboration:
- Provide a fully finalized and approved base pattern (digital format preferred by most).
- Supply a complete Tech Pack including clear base size measurements and Points of Measurement (POMs).
- Discuss and confirm the grade rules to be used. Either provide your brand’s established rules or agree upon using the pattern maker’s / clothing manufacturer’s standard rules or relevant industry standards.
- Clearly specify the full required size range (e.g., XS – XXL).
- Request to review the graded pattern nest (all sizes layered) or at least the completed graded spec sheet before any production samples are cut.
- Maintain open and clear communication with your pattern maker or factory contact throughout the process. Address questions promptly.
5. Practical tips for developing your brand’s grade rules
5.1 Aligning with your target customer demographics and garment style
Effective Grade Rules should reflect both your target customer and the specific garment style. Consider the general body type characteristics prevalent in your customer demographic (e.g., juniors, contemporary misses, plus size, tall).
The intended fit intent also plays a role; grade rules for a deliberately oversized sweatshirt might differ slightly from those for a sharply tailored blazer. Similarly, grading might be approached differently for very stretchy knitwear versus structured woven fabrics, influencing ease allowances.
5.2 Researching body measurement data and competitor apparel sizing
Developing grade rules doesn’t happen in a vacuum. Start by referencing standard body measurement charts (like those from ASTM International or other regional standards bodies) relevant to your target market. These provide a baseline understanding of average body dimensions.
Additionally, analyze the apparel sizing, fit, and measurement specifications of successful direct competitors targeting a similar customer. Understanding how their garments measure can provide valuable context and help align your sizing with general customer expectations in your niche.
5.3 Considering fabric properties in your grading process
While the core grade rules provide the primary increments, experienced pattern makers often subtly adjust these or the ease allowances (the difference between body measurements and garment measurements) based on fabric properties.
A very stretchy knit (stretch fabric) might require slightly different grading increments or less ease compared to a rigid, non-stretch woven fabric to achieve a comparable perceived fit across sizes. The fabric’s weight and drape can also influence how the garment hangs and behaves on different body sizes. Acknowledging this nuance is part of refining the grading process, though the primary rules remain the foundation.
6. Related questions
6.1 What’s the typical cost range for pattern grading services?
The pattern grading cost can vary significantly based on several factors. Complexity is a major driver – a simple T-shirt with few pattern pieces and POMs will cost less to grade than a complex jacket with many details. The method used also matters; digital grading services often price per size graded (e.g., $10-$30 per size) or per style (e.g., $75-$250+ for a full size range), though these are very broad estimates.
The experience and location of the grading provider, whether grading is bundled with initial pattern making, and the required turnaround time also influence the pricing. It is always best practice to obtain quotes from several potential providers based on your specific garment and requirements.
6.2 Is it advisable to grade patterns across significantly different size categories?
Generally, grading across categories that represent fundamentally different body proportions is not recommended for achieving optimal fit. For instance, simply grading a standard Misses size 14 pattern up multiple times is unlikely to result in a well-fitting Plus Size garment, as fat distribution and body shape change significantly.
Similarly, grading a children’s sizing pattern up to adult dimensions (or vice-versa) ignores the dramatic proportional shifts during growth. The best practice is to develop separate base blocks (foundational patterns) and distinct grade rules specifically optimized for each major size category (e.g., Children’s, Juniors, Misses, Women’s/Plus, Men’s) your brand intends to serve. Simple grading might work for adjacent sizes within the same category, but not across major demographic shifts.
6.3 What are some common pitfalls or mistakes to avoid when implementing size grading?
Several common mistakes can undermine the effectiveness of size grading and lead to fit issues:
- Grading from an ill-fitting base size: If the initial sample doesn’t fit correctly, grading will replicate those flaws across all sizes. Base size fit perfection is paramount.
- Using incorrect or inconsistent grade rules: Applying the wrong increments or varying rules randomly leads to unpredictable sizing. Grade rules accuracy is crucial.
- Not considering garment style or fabric: Applying generic rules without accounting for fit intent (e.g., fitted vs. loose) or fabric stretch can distort the design across sizes.
- Ignoring key POMs or having inaccurate base measurements: Missing crucial measurement points or starting with faulty base specs guarantees flawed graded specs. Accurate POMs are essential.
- Making excessively large jumps between sizes: Attempting to grade directly from a Small to an XXL in one step, rather than incrementally, can distort proportions.
- Poor communication with the pattern maker/factory: Ambiguity or lack of clarity regarding rules, specs, or the base pattern invites errors. These are significant grading pitfalls.
Read more:
Mastering size grading is an indispensable step for any apparel brand aiming for professionalism and customer satisfaction. This process involves systematically scaling a perfected base size pattern using specific rules and methods—either traditional manual techniques or, more commonly today, efficient digital CAD systems.
The output, documented clearly in the Graded Measurement Specification Sheet within the Tech Pack, ensures clear communication with manufacturers. Ultimately, investing the effort to achieve consistent sizing across your product line directly translates to increased brand trust, enhanced customer loyalty, and a significant reduction in costly returns. It’s a foundational element of building a successful and reputable clothing business.
Ensuring your garments fit perfectly is step one; let My Pack Love help with the finishing touches like custom labels and packaging that reflect your quality.